Credit achievement rate
XX%
Upgrade to LEEDuser Premium to see how many projects achieved this credit. Try it free »
LEEDuser’s viewpoint
Frank advice from LEED experts
LEED is changing all the time, and every project is unique. Even seasoned professionals can miss a critical detail and lose a credit or even a prerequisite at the last minute. Our expert advice guides our LEEDuser Premium members and saves you valuable time.
Credit language
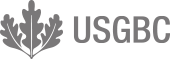
© Copyright U.S. Green Building Council, Inc. All rights reserved.
Requirements
Select 1 of the 3 compliance path options described below. Project teams documenting achievement using any of the 3 options are assumed to be in compliance with EA Prerequisite 2: Minimum Energy Performance.
Option 1. Whole building energy simulation (3-21 points)
Demonstrate a percentage improvement in the proposed building performance rating compared with the baseline building performance rating. Calculate the baseline building performance according to Appendix G of ANSI/ASHRAE/IESNA Standard 90.1-2007 (with errata but without addenda1) using a computer simulation model for the whole building project. Projects outside the U.S. may use a USGBC approved equivalent standard2. The minimum energy cost savings percentage for each point threshold is as follows:New Buildings |
Existing Building Renovations |
Points |
---|---|---|
12% |
8% |
3 |
14% |
10% |
4 |
16% |
12% |
5 |
18% |
14% |
6 |
20% |
16% |
7 |
22% |
18% |
8 |
24% |
20% |
9 |
26% |
22% |
10 |
28% |
24% |
11 |
30% |
26% |
12 |
32% |
28% |
13 |
34% |
30% |
14 |
36% |
32% |
15 |
38% |
34% |
16 |
40% |
36% |
17 |
42% |
38% |
18 |
44% |
40% |
19 |
46% |
42% |
20 |
48% |
44% |
21 |
- Compliance with the mandatory provisions (Sections 5.4, 6.4, 7.4, 8.4, 9.4 and 10.4) in Standard 90.1-2007 (with errata but without addenda) or USGBC approved equivalent.
- Inclusion of all the energy costs within and associated with the building project.
- Comparison against a baseline building that complies with Appendix G of Standard 90.1-2007 (with errata but without addenda) or USGBC approved equivalent. The default process energy cost is 25% of the total energy cost for the baseline building. If the building’s process energy cost is less than 25% of the baseline building energy cost, the LEED submittal must include documentation substantiating that process energy inputs are appropriate.
OR
Option 2. Prescriptive compliance path: ASHRAE Advanced Energy Design Guide (1 point)
Comply with the prescriptive measures of the ASHRAE Advanced Energy Design Guide appropriate to the project scope, outlined below. Project teams must comply with all applicable criteria as established in the Advanced Energy Design Guide for the climate zone in which the building is located. Projects outside the U.S. may use ASHRAE/ASHRAE/IESNA Standard 90.1-2007 Appendices B and D to determine the appropriate climate zone.Path 1. ASHRAE Advanced Energy Design Guide for Small Office Buildings 2004
The building must meet the following requirements:- Less than 20,000 square feet (1,800 square meters).
- Office occupancy.
Path 2. ASHRAE Advanced Energy Design Guide for Small Retail Buildings 2006
The building must meet the following requirements:- Less than 20,000 square feet (1,800 square meters).
- Retail occupancy.
Path 3. ASHRAE Advanced Energy Design Guide for Small Warehouses and Self Storage Buildings 2008
The building must meet the following requirements:- Less than 50,000 square feet (4,600 square meters).
- Warehouse or self-storage occupancy.
OR
Option 3. Prescriptive compliance path: Advanced Buildings™ Core Performance™ Guide (1-3 points)
Comply with the prescriptive measures identified in the Advanced Buildings™ Core Performance™ Guide developed by the New Buildings Institute. The building must meet the following requirements:- Less than 100,000 square feet (9,300 square meters).
- Comply with Section 1: Design Process Strategies, and Section 2: Core Performance Requirements.
- Health care, warehouse or laboratory projects are ineligible for this path (for NC & CS Projects).
- 1 point is available for all projects (office, school, public assembly, and retail projects) less than 100,000 square feet (9,300 square meters) that comply with Sections 1 and 2 of the Core Performance Guide.
- Up to 2 additional points are available to projects that implement performance strategies listed in Section 3: Enhanced Performance. For every 3 strategies implemented from this section, 1 point is available.
- The following strategies are addressed by other aspects of LEED and are not eligible for additional points under EA Credit 1:
- 3.1 — Cool Roofs
- 3.8 — Night Venting
- 3.13 — Additional Commissioning
Pilot ACPs Available
The following pilot alternative compliance path is available for this credit. See the pilot credit library for more information. EApc95: Alternative Energy Performance Metric ACPWhat does it cost?
Cost estimates for this credit
On each BD+C v4 credit, LEEDuser offers the wisdom of a team of architects, engineers, cost estimators, and LEED experts with hundreds of LEED projects between then. They analyzed the sustainable design strategies associated with each LEED credit, but also to assign actual costs to those strategies.
Our tab contains overall cost guidance, notes on what “soft costs” to expect, and a strategy-by-strategy breakdown of what to consider and what it might cost, in percentage premiums, actual costs, or both.
This information is also available in a full PDF download in The Cost of LEED v4 report.
Learn more about The Cost of LEED v4 »Frequently asked questions
See all forum discussions about this credit »Addenda
For our project, a high rise condominium tower, we are considering providing at move-in, full coverage, insulated, automated blinds on the interior of the building as part of the energy use reduction design strategy. These blinds will be built-in, non-optional, and fully automated with a manual override to allow occupants to override the automatic settings. The alternative would normally be owner provided blinds with a wide range of characteristics, but not likely to include the heavy, insulated blinds envisioned by this energy measure. We are considering sizing the design cooling and heating so that comfort can be maintained most effectively by using the blinds. Cooling reduction will probably include some venting between the fenestration and the interior blinds so that heat that enters the glazing does not stay in the space. Can we take credit for automatic shading by using the DOE2.2 shading inputs so the energy impacts are integrated with the rest of the model? ASHRAE 90.1-2004 Appendix G indicates that manual shades and blinds not be modeled in the baseline or the design. Automatic blinds or shades can be modeled for the design, and the baseline description does not say if these are to be modeled or not. For this energy measure, variations in model schedules between the design and baseline, with clearly stated assumptions and documentation, would be the appropriate way to model the difference in the operation of blinds between the design and baseline. Other inputs would account for differences in the design blinds and typical owner blinds including R-value, and shading coefficient. Please clarify whether we can capture the efficiency benefits of this strategy within our EAc1 model, and if so, the modeling requirements per the questions above and any other factors that might apply.
The project team is seeking clarification regarding how to document the savings achieved from automated shading. ASHRAE 90.1-2004 Appendix G does allow credit in the Proposed Building model for automated shading devices, including automated blinds. No manual or automated window shading devices should be modeled in the Baseline Building model. If the energy software does not have the capability to model automated shading devices, the assumptions used for defining automated shading schedules should be clearly documented. Also, if the automated shading devices include a manual override for user control, the assumptions regarding percentage use of the automated controls should be clearly stated. Applicable Internationally.
We have multiple new projects on the University of Colorado at Boulder\'s campus all seeking LEED certification which will be serviced by a new heating and cooling plant, also seeking LEED certification. The schedule of the projects is such that the earliest building complete will be complete and occupied approximately one year prior to the completion and start up of the new heating and cooling plant. Although this project is completely designed to be serviced by the new plant (and the drawings will reflect this), the project schedules will create a lapse where the building will have to be serviced by a temporary means until the new heating and cooling plant is operational. The current plan is to utilize temporary chillers and boilers. We believe it is appropriate for our energy model and all other LEED submittals to reflect the final connection to the CUP and not the temporary equipment. Please confirm this approach is acceptable. In addition, please clarify whether the temporary equipment must be commissioned to satisfy EAp1. The new CUP will be commissioned as well as all "downstream" equipment at each building in accordance with the May 28, 2008 CUP memo.
The project team is requesting permission to use the designed central plant specifications for EAc1 Option 1 and all LEED submittals versus the temporary plant that will be connected to the newest building on campus seeking LEED certification. The project team has also requested exception from the EAp1 requirement for commissioning the temporary equipment. The permanent equipment intended for the campus central plant may be used in submitting for EAc1 if the project team provides a letter on owner letterhead stating that the permanent central plant is fully funded. Please also include in the letter a comparison of the schedule of completion for the building in question to a schedule of completion for the central plant. Additionally, if the intent is to use this for other prerequisites and/or credits, this letter should address adequately how the requirements for all credits and prerequisites are being met effectively. However, the temporary equipment shall not be exempt from meeting the requirements of EAp2 - Minimum Energy Performance or EAp1 - Fundamental Commissioning, as this temporary equipment will be in operation for at least one year, if not more. It is necessary that the project team meet those requirements, i.e., a basic minimum level of energy performance and fundamental building systems commissioning for even the temporary equipment.
The project is an existing landmarked building in NYC pursuing LEED Core & Shell certification. Specifically, the building will undergo a gut rehab of all its floors. The building is currently served by four CFC chillers. To increase the energy efficiency of the building, and to obtain the two EAc1 points, the building plans to replace the CFC chillers with efficient chillers that also comply with the requirements of EAc4 Enhanced Refrigerant Management. Energy modeling projects that chiller replacement will result in $48,200/year energy cost savings. The cost of replacing chillers is high, because piping and ducting added over the years to the mechanical room are making the removal of the chillers impossible without changes to the MER. The cost of replacement including changes that would be needed for piping, controls and modifications to existing mechanical room is estimated to be 4-5 million dollars, resulting in a simple-payback above 80 years. Under LEED-EB, the Ozone protection prerequisite recognizes that if replacing chillers is not economically feasible, or if the simple-payback of the replacement is greater than 10 years, an alternate compliance path would be acceptable. The path recommended is that the CFC-based refrigerants be maintained, and the annual leakage be reduced to 5 percent for the life of the units (the requirements for LEED-EB). We believe that this indicates that flexibility can be granted when economic conditions are adverse, and would like to propose that such flexibility to granted to the LEED CS EAc1 in this particular case. Chiller replacement in this building is not economically feasible, but the owner has committed nonetheless to phase in new chillers over the period of 5 years. The 5-year period is primarily due to the large economic burden required by a replacement that does not have a reasonable payback. Computer modeling projects that with this replacement the Core & Shell will meet the 2 credit requirement for EAc1. We propose that replacing the chillers over 5 years is much better than retaining the current chillers, both for energy use and for ozone-depletion reasons - even with care for CFC leakage. With the owners committed to phasing in the new non-CFC chillers within 5 years, will this be acceptable to use the new, planned chillers for meeting the 2 point requirement for EAc1?
Phasing in of new, non-CFC chillers within 5 years appears to meet the intent of EA prerequisite 3 on Fundamental Refrigerant Management. Prior to phase-out, the annual leakage of CFC-based refrigerants must be reduced to 5% or less using EPA Clean Air Act, Title VI, Rule 608 procedures governing refrigerant management and reporting. EAc1, Energy Performance Optimization, should not include the future chillers. This is covered by Appendix G, section G1.3 (p.169), which states that parameters relating to future components shall be identical in determining the baseline and proposed building performance. Applicable Internationally.
There is significant confusion, and seemingly contradictory LEED Interpretations on the required methodology for addressing “purchased” on-site renewable energy, and/or purchased biofuel that is not considered on-site renewable energy within the LEED energy model. For renewable fuels meeting the requirements of Addendum 100001081 (November 1, 2011) or other purchased renewable fuels, how should purchased on-site renewable energy be treated in the LEED energy model? How should purchased bio-fuels (meaning it I not fossil fuel but is used in a similar manner to bio-fuel) be treated in the energy model?
For any on-site renewable fuel source that is purchased (such as qualifying wood pellets, etc.), or for biofuels not qualifying as on-site renewable fuel sources that are purchased, the actual energy costs associated with the purchased energy must be modeled in EA Prerequisite 2: Minimum Energy Performance and EA Credit 1: Optimize Energy Performance, and the renewable fuel source may not be modeled as "free", since it is a purchased energy source.
For non-traditional fuel sources (such as wood pellets) that are unregulated within ASHRAE 90.1, use the actual cost of the fuel, and provide documentation to substantiate the cost for the non-traditional fuel source. The same rates are to be used for the baseline and proposed buildings, with the following exception: If the fuel source is available at a discounted cost because it would otherwise be sent to the landfill or similarly disposed of, the project team may use local rates for the fuel for the baseline case and actual rates for the proposed case, as long as documentation is provided substantiating the difference in rates, and substantiating that the fuel source would otherwise be disposed of.
When these non-traditional fuel sources are used for heating the building, the proposed case heating source must be the same as the baseline case for systems using the non-traditional fuel source, and the project team must use fossil fuel efficiencies for the Baseline systems, or provide evidence justifying that the baseline efficiencies represent standard practice for a similar, newly constructed project with the same fuel source.
Updated 8/7/17 for rating system applicability.
Can we take credit for a demand ventilation system for an automotive service area?Essentially we propose to model the service area in the Baseline Cases at 100% outside air at 1.5 CFM/sq.ft. during occupied periods to meet ASHRAE 62.1. We plan to model the service area in the Proposed Case with typical storage ventilation rate. See rationale below to validate our assumptions.We further propose to model this energy efficiency measure in the standard credit energy models (not as an exceptional calculation) as part of the Baseline and Proposed Cases in order to accurately account for the differences in ventilation load. The differences are based on outside air conditions which change throughout the year and they also impact the supply air unit and fan sizes. The simulation program must size the equipment for the Baseline Case at the peak load and model it use 8760 hours in the year. ASHRAE 62.1 lists a specific minimum ventilation rate for automotive service areas at 1.5 CFM/sq. ft. Ventilation reduction controls are not stated in Ashrae 62.1, nor are they mandated in ASHRAE 90.1-2007. The governing Mechanical Code (International Mechanical Code) optionally permits the use of approved automatic detection devices to control the required ventilation fans and/or make-up air systems. Large make-up air systems providing 100% outside air are still readily available and utilized in order to meet the mandated code. We have utilized the following assumptions for modeling energy usage:Baseline Case - The exhaust ventilation system is modeled to operate at 1.5 CFM/sq.ft. during occupied hours per occupancy schedule. The modeling software automatically sizes the air conditioning system to operate as a 100% outside air system as the total CFM requirement exceeds the design load amount. The unoccupied fan cycle does not include the ventilation and only operates to maintain unoccupied thermostat set point.Proposed Case - The exhaust ventilation system is modeled to be non-operational at any time. We make this assumption based on calculation and witnessed operation at like facilities with the identical control system in place. We have calculated carbon monoxide production based upon maximum estimated daily vehicle round trips through the service area. Eighteen service stalls with an average of 3 vehicles per day and 1 minute round trip drive time yields an estimated total vehicle drive time in the service area to be 54 minutes. The average modern vehicle with catalytic converter produces approximately 150 CFM of exhaust airflow at idle to slow speed containing approximately 1,000 PPM of carbon monoxide. 150 CFM X (0.1%) = 0.15 CFM of carbon monoxide production. The requirement to engage the exhaust ventilation system is 50 PPM of carbon monoxide. The volume of the space is 236,900 cu.ft. and would require 11.845 cu.ft. of carbon monoxide to engage the system. This would require 78.97 minutes of continuous operation without any dilution in a facility this size which exceeds the estimated maximum vehicle operation time of 54 minutes by 30%. The air conditioning equipment serving the area provides 800 CFM outside air and is equivalent to a complete air change twice a day and therefore doubling the daily total required operation time to 157.94 minutes. Operation of vehicles for diagnostic testing is excluded as there is a separate tailpipe extraction system in place to remove all exhaust during testing. Calculations are no substitute for actual conditions. We have interviewed service managers as to the operations of the emergency exhaust system controlled with a CO monitor system. The feed back is overwhelming that the emergency system is never engaged during normal operation. The technicians in these facilities have been trained in the control systems operations and do not desire to have their "conditioned" air purged from the building due to excessive operation of the vehicles within the space.
A project team cannot be awarded credit for demand controlled ventilation in an automotive service area, due to concerns over contaminants, and possible effects on indoor evironmental quality. As there is no current accepted methodology, the potential human health risks outweigh the energy savings.
Our project consists of multifamily rental units. We are performing the energy model using TRACE 700, a program that meets ASHRAE Standard 140-2004: Building Thermal Envelope and Fabric Load Tests. TRACE 700 does not have the capability of modeling domestic hot water energy usage. In order to account for domestic hot water energy usage we are proposing to use the Department of Energy sponsored Lawrence Berkeley National Laboratory calculation methodology. The spreadsheet can be found at www.doa.state.wi.us/docs_view2.asp?docid=2249. This spreadsheet estimates the energy consumption of water heaters based on power source, energy factor, and recovery efficiency. In addition, the spreadsheet estimates the energy reductions associated with hot water consumption of Energy Star clothes washers and dishwashers. According to the CIR ruling dated 4/25/2007, credit cannot be taken for low flow fixtures accounted for in WE credit 3. However, clothes washers and dishwashers are not accounted for in LEED NC v2.2 WE credit 3. An exceptional calculation in accordance with Appendix G will be provided to demonstrate energy savings for the Energy Star appliance itself. In addition, we believe the reduction in the amount of hot water required by Energy Star clothes washers and dishwashers should be accounted for in the water heating calculation. The basis for these calculations found at http://hes.lbl.gov/hes/aboutwhm.html will be uploaded as supporting documentation. 1. Can we use the Lawrence Berkeley National Laboratory spreadsheet since TRACE 700 does not model energy consumption for domestic water heaters? 2. Can the energy savings for the reduced hot water consumption for Energy Star clothes washers and dishwashers be accounted for in the domestic hot water energy consumption calculation?
The applicant is asking for confirmation that LBNL spreadsheet calculations can be used to document domestic hot water use and asking if hot water savings resulting from Energy Star clothes washers and dishwashers can be accounted for in the exceptional calculation. 1. It seems that the LBNL spreadsheet calculations are an appropriate method for calculating domestic hot water use and for documenting the energy savings associated with Energy Star equipment. However in order to be accepted as an exceptional calculation, be sure to include a detailed narrative with all assumptions and supporting calculations with the submittal. 2. Yes, energy savings for reduced hot water consumption can be counted in DHW energy calculation. ***Please note, this CIR was updated on 7/10/2009.***
Our project is being considered for re-registration from LEED-CS v2.0 to LEED-NC v2.2. The building is 65,762 GSF with 48,664 SF of total leasable space. 25,997 SF (53%) of the building has been leased, designed, and under construction. However, the remaining 22,667 SF (47%) is unleased shell space. The unleased shell space is outside of the project scope and there is no design currently underway for this to complete work in this area. In order to pursue EA Credit 1 (Optimize Energy Performance), our engineers would like guidance on how to create their energy model based on our building situation of 53%-to-47% leased vs. shell spaces. It is their intention to model the unleased shell space as if the space were "upfit" to the same standard as the leased portion of the building. This standard would be described in a tenant improvement guidelines provided to future tenants. Please verify this method is acceptable or provide an alternate method for energy modeling.
The applicant is requesting clarification regarding energy modeling of shell spaces that do not yet include tenant fitouts. This topic has been extensively addressed in the published erratum for LEED-CSv2.0 (http://www.usgbc.org/ShowFile.aspx?DocumentID=3334), as well as previous CIR rulings (CSv2.0 Rulings dated 05/27/2008, 04/25/2008, 04/23/2008, 04/24/2008, 02/11/2008, 11/28/2007, 12/5/2007, 11/14/2007, and 05/30/2007). For LEED-CS, tenant guidelines alone are not sufficient to verify energy efficiency measures incorporated into future leased space. The published erratum indicates that documentation should be provided including lease or sales agreements verifying that 100% of the leased square footage complies with the credit requirement, and a statement signed by the owner / developer verifying that all leases and/or sales agreements will comply with the credit requirements. For future leased spaces, the letter from the owner / developer is only required if efficiency measure improvements beyond ASHRAE 90.1-2004 are reflected in the future leased spaces (e.g. improved lighting power density, improved HVAC efficiency, etc.). Applicable Internationally.
We seek approval of the following energy analysis approach for a project registered under LEED-NC v2.2, after June 26, 2007. The project is a ballpark located in Climate Zone 5A. A majority of the concession stands and restrooms located on the concourses will only be used for ballgames from April through September. Traditionally, space unit heaters are installed for freeze protection of the plumbing systems and building finishes during unoccupied periods. These unit heaters would have a heating output between 3.4 Btu/h ft2 and the maximum allowance of 15 Btu/h ft2 listed in Table 3.1 of ASHRAE/IESNA Standard 90.1-2004, so the spaces would technically be considered semiheated. The spaces would be maintained at a minimum setpoint of 45 degrees F to ensure that none of the pipes freeze. We are considering implementing an energy conserving operational procedure. The plumbing systems would be drained down during the off-season from October through March when freeze potential exists. This practice requires special design consideration for ease of the drain down procedure. The concession stands and restrooms would require no space heating equipment, thereby eliminating space heating energy. The drain down practice requires special effort from building operations staff, and we believe that a commitment to such effort warrants consideration in the energy analysis. The energy savings are quantifiable and provide an environmental benefit. The drain down practice allows elimination of additional insulation and building materials that also provides an environmental benefit. Therefore, we propose to classify these concession stand and restrooms located on the concourses as semiheated spaces. The baseline insulation would be modeled as semiheated; the baseline heating setpoint would be modeled at 45 degrees F. The proposed spaces would be modeled as unconditioned.
The applicant is proposing that the proposed design be considered an unconditioned space in the energy simulation due to the application of a drain down procedure. The proposed approach is not acceptable. ASHRAE 90.1-2004 Table G3.1 Number 10(c) states that an electric heating system must be modeled in the proposed case even if a heating system is not provided in the baseline case. Note that several CIRs address modeling requirements of unconditioned and semi-heated spaces, including a CIR dated 10/3/2008 that confirms unconditioned spaces must be modeled with a heating system.
The project is a high-rise residential building that is being applied under LEED-CS certification. Living units are being designed without air-conditioning system, since generally the people use natural ventilation during summer. Building spaces with regular occupation, such as bedrooms and living rooms, will be furnished with operable windows only, without mechanical systems. Therefore, under ASHRAE Standard 90.1 the entire building would be defined as unconditioned space, and the envelope does not need to comply with mandatory provisions of that Standard. Following this interpretation, the scope of work for this project would be limited to sections 7, 8, 9 and 10 of ASHRAE Standard 90.1, as the building will be provided with: service water heating; power distribution systems; lighting systems for common areas; and electric motors (stairs ventilators, water pumps and sewage pumps). In order to achieve the minimum energy performance prerequisite needed for LEED certification, only the lighting system for common areas and the service water heating were identified by the design team as the scope of work to be treated under ASHRAE Standard 90.1 and modeling rules of appendix G. This CIR is to clarify three questions: 1. Is this building eligible to certification under LEED, even without HVAC system? 2. If affirmative, the minimum energy performance has to be achieved only for those systems that will be provided by the owner, i. e., lighting system for common areas and service water heating? 3. Can natural ventilation be used as an energy efficiency strategy to achieve the minimum energy performance, in similar way as discussed in a CIR posted in 03/22/2007 (through an Exceptional Calculation Methodology)?
1) Yes, the project is eligible for LEED certification. 2) Yes, the minimum energy performance and energy savings only applies to systems supplied by the owner. PLEASE NOTE that this project must comply with the mandatory provisions (Sections 5.4, 6.4 (when applicable), 7.4, 8.4, 9.4, and 10.4) of ASHRAE 90.1-2004, which includes the Building Envelope. Section 5.1.2.2 of ASHRAE 90.1-2004 clearly states that "spaces shall be assumed to be conditioned space and shall comply with the requirements for conditioned space at the time of construction, regardless of whether mechanical or electrical equipment is included in the building permit application or installed at that time." 3) Yes, natural ventilation can be used as an energy efficiency strategy to achieve minimum energy performance through the Exceptional Calculations Methodology approach outlined in CIR Ruling 3/22/2007. Credit achievement is contingent on the submittal documentation and compliance with the stated method to the satisfaction of the certification reviewer. Please be sure to submit the documentation outlined in the CIR in order to determine compliance during LEED certification. Applicable Internationally.
Our LEED project consists of two office buildings of approximately 160,000 sf each plus a central refrigeration plant and parking deck. All buildings will be submitted as one LEED project. The project is currently under construction. The energy model for the project was constructed using Trace700 and is a comprehensive model of all three structures. In addition to the 20% energy savings already being reflected in the model, substantial energy savings will be realized by the investments the Owner has made in advanced energy efficiency measures such as daylighting through a central atrium and interior glazing, raised floor thermodynamics and a hybrid HVAC system. Due to limitations of the Trace700 modeling software, the contributions of these sophisticated energy efficiency measures are not currently reflected in the modeled energy savings. To support the ongoing operations of the building, the Owner has invested in a measurement and verification system, which per EA Credit 5, will include measurement of all electrical power panels, lighting panels broken into interior and exterior lighting, and all hvac equipment. The M&V system will measure and trend demand and consumption of electricity, water and natural gas on an hourly basis for all hours of the year. The project cannot bear the added expense that would be required to perform extensive hand calculations, daylight models or to use more sophisticated energy modeling software, but we would like the Owner to be recognized with LEED points for the contribution that their investment in energy efficient design strategies represents. We would like to incorporate the actual measured performance of the lighting, power, and HVAC systems into the Trace700 model. We propose to delay our LEED application at the end of construction and with all buildings in operation, to measure the building systems performance for 3 to 6 months through the M&V devices. We would then substitute values from the measured performance into the design case energy model. The data would be input on a watt/sqft, kw/cfm, btu/hr, cfh, or gal/min basis. We believe that using measured performance data in the creation of the final design case model would be a cost-effective, accurate means of accounting for the contributions of sophisticated energy efficiency measures, and request permission to use this approach on our project.
The CIR is asking if actual logged energy use data being collected for EAc5 can be used to more accurately represent the proposed building energy use for EAc1, with the caveat that the project certification will be held up until this data has been collected and the energy model has been calibrated. It should be noted that incorporating measured data into an energy model is a strategy fraught with many technical challenges. USGBC encourages project teams to use energy models as a design tool. That said, the proposed technique is acceptable, provided the following conditions are met: [1] One full year\'s worth of energy use data must be included to account for seasonal effects. Additionally, this gives time for the commissioning of the facility to be completed and the "bugs" worked out of the system. [2] The collected energy data cannot be directly compared to the baseline modeled energy data. Instead the collected data should be used to populate the inputs to the energy modeling program (ie- plug loads, lighting densities, etc). This is because modeling programs inherently contain assumptions and methodologies that do not directly correspond to actual building energy use. By still running a simulation for the baseline and proposed cases, these discrepancies effectively cancel each other out. [3] The applicant must be able to show that the occupancy schedules, building set points, and intended use of the facility are the same in the baseline and proposed case. [4 The baseline energy simulation must utilize a weather file that represents the same metrological conditions that occurred during collection of the energy use data. [5] Submit all documentation required for an Exceptional Calculation Methodology, as described in ASHRAE 90.1-2004 Appendix G. Applicable Internationally.
Our client is a Real Estate Investment Trust (REIT) that focuses on the development and ownership of grocery anchored retail centers. They own over 450 retail centers nationwide with over 60 million square feet of gross leasable area. They are interested in adopting a company-wide toolkit that provides consistency in their decision making process as it pertains to energy efficiency and overall sustainable/green strategies, including a minimum of LEED-CS2.0 certification. The main objective of this inquiry is related to the development of a methodology for earning EAc1 points, based upon a customized set of prescriptive energy efficiency measures determined through the energy modeling of five prototypes in eight climate regions that are demonstrated to effectively bring about minimum efficiencies to earn at least two EAc1 points. Currently, our client has developed five different prototype buildings that are distinct to each of the five markets/regions that they work in: Northeast, Southeast, Central, Southwest, and Northwest. Below is an outline of the modeling methodology and a description of the documentation that would be provided for certification review. We would like to propose the following prescriptive methodology for each prototype building, in lieu of performing individual energy modeling for each project seeking LEED certification under LEED-CS v2.0 rating system. If the approach is not acceptable, then we would like to receive guidance from the USGBC as to what aspects would need to be modified to obtain approval. Methodology: Develop a customized process and methodology for identifying the most appropriate energy saving strategies for all core & shell prototype projects. The approach is to use ASHRAE 90.1-2004 Appendix G modeling methodologies to investigate various energy efficiency measures for each of the five markets and prototypes and develop and compile a list of prescriptive building related measures that mirrors ASHRAE\'s Advanced Energy Design Guides (AEDG) Recommendation Table, but is customized to this developers specific project prototype approach. The intent is that only freestanding new construction core & shell buildings with individual HVAC systems are eligible. Projects that utilize energy supplied from district or centralized energy sources, e.g. district plant, would not be allowed to use this approach and must follow LEED guidance for projects using district supplied energy. Each market sector will be sub-categorized, as required, to correspond to one of ASHRAE\'s 8 climate zones. All prescriptive measures will be categorized to a prototype, a climate and to an orientation. The orientation will be determined by which way the building\'s main entryway is facing. All of the adopted prescriptive measures will be generated and evaluated using eQuest DOE2 energy modeling software. The software exceeds ASHRAE Appendix G minimum simulation software criteria. For consistency, the building\'s prescriptive measures will be grouped to correspond similarly with ASHRAE\'s AEDG structure. Below is an outline of how the building components with be grouped and categorized: Envelope: Roof, Walls, Floors, Slabs, Doors, Vertical Glazing, and Skylights Lighting: Interior and Exterior Lighting HVAC: HVAC, Economizer, Ventilation, Ducts Service Hot Water: Service Hot Water Heater LEED Submission: The documentation that would be provided to USGBC for LEED certification review would consist of the following: A signed LEED Submittal Template declaring an alternative compliance path has been followed. A copy of a CIR or other documentation from the USGBC approving the alternative compliance path. A narrative describing the modeling methods and supporting that they conform to ASHRAE 90.1-2004 A comparison summary table demonstrating that the energy measures implemented in the project correspond with the required prescriptive measures. Any additional documentation necessary to support the claimed energy savings. This customized approach for EAc1 will result in meeting both the intent and the performance requirements of the credit. Can we proceed with this approach and if not, how would we need to modify this approach to be acceptable to the USGBC?
The project team is requesting that five standard energy models based on a design \'prototype\' from five different regions be acceptable documentation for all prototype projects from that owner/developer currently pursuing LEED certification in lieu of creating energy models for each project in line with the requirements for EA Credit 1. Each individual project will have energy use/cost variations depending on objects other region and system type. Energy use and cost is greatly impacted by: building orientation, elevation, average solar gain, utility rates, local code requirements, and more. A snapshot prototype energy model will not adequately describe the energy requirements of all projects in the same region, and an individual energy model must be submitted for each building pursuing certification. Applicable Internationally.
For a building with two tenants, only one of whom is currently building out the space, is it necessary to include the space to be occupied by the future tenant within the project boundary?
Because the tenant space comprises less than 50% of the total building area, the project should pursue certification under LEED for New Construction and include the tenant space in the credit calculations. For unfinished tenant spaces, tenant guidelines must be provided. Applicable internationally.
We are requesting clarification regarding what percentage of a building must be open 24 hours for the building to be considered a 24-hour facility. ASHRAE 90.1-2004, Section 6.5.6.2 requires condenser heat recovery for preheating service hot water for facilities operating twenty-four hours per day, when the total installed heat rejection capacity of the water-cooled systems servicing the building exceed 6,000,000 Btuh, and the design service water heating load exceeds 1,000,000 Btu/h. Our project is a large retail complex which most likely exceeds the total installed heat rejection and service water heating loads listed. However, only 17% of the complex (a large arcade facility) is open 24 hours per day. The rest of the complex will be closed for a portion of each day. We believe we are exempted from the heat recovery requirement since the domestic water heating loads are mostly coming from the areas of the building that are not open 24 hours, and since only a fraction of the complex is open 24 hours per day. We would like confirmation that our interpretation is correct.
The applicant is asking to confirm their interpretation of a specific ASHRAE 90.1-2004 requirement. If the capacity that serves the 24 hour facility (described as 17% of the project) is below the ASHRAE defined limits for installed heat rejection capacity and service hot water heating loads, then the project does not need to follow the requirements of ASHRAE 90.1-2004 Section 6.5.6.2. If the capacity is greater than the defined limits, then the project must follow the requirements.
Our project is a 65,000 SF injection molding manufacturing facility and office near Detroit, MI. The project consists of 10,000 SF of air-conditioned office space, and 55,000 SF of air-conditioned manufacturing space, which includes injection molding equipment, as well as occupied assembly areas. The energy required for the manufacturing process exceeds 85% of the facility\'s total energy load. To achieve the 14% minimum energy savings, process load energy savings must be taken into account. As a result of the high energy loads associated with the manufacturing process, as well as the energy not falling under ASHRAE 90.1-2004, an exceptional calculation method must be established for the manufacturing area. Both the office area and the manufacturing area are conditioned. Space cooling in these areas will be achieved through constant volume rooftop units, and will be modeled through a standard energy modeling software like Trane Trace 700. The manufacturing process includes injection molding machinery which is cooled through a chiller & cooling tower assembly. The load on the chiller and cooling tower will not fluctuate (except for operational and non-operational hours, which will be achieved through a schedule). The chiller and cooling tower performance will be run in a separate energy model using this constant load to determine the overall energy used based on the outdoor air conditions throughout the year. The Chiller and cooling tower energy used will then be input into the original model as annual process energy. The Chiller and Cooling Tower efficiencies for the baseline will be based off ASHRAE 90.1-2004 minimum standards. The injection molding equipment proposed is state-of-the-art and very energy efficient compared to the standard injection molding machinery that is the industry standard. Using the client-provided operational times for the equipment we will be able to estimate the total energy used by this injection molding equipment, as well as the total energy that would be used by industry standard equipment. This will be used to determine the annual energy for both the baseline and the proposed design. We will then input these amounts into the original energy model as annual process energy. For comparison purposes, we also have a similar plant by the same client that uses the industry standard machines. By comparing the amount of equipment and square footage of this plant, we can achieve a very accurate idea of how much energy the new plant is saving. All calculations showing how the machinery energy was determined, and results of planned field monitoring, will be explained in an excel spreadsheet. Equipment descriptions and energy loads will be shown for all machines that will be used, as well as for comparable industry standard machines. Once the process equipment, both baseline and proposed, have been input into the overall energy model as process loads, the standard reports issued from the model will be used for the LEED Reports. In addition, we will provide the sub-energy models of the process equipment that is weather-based. Please confirm that our assumptions and method of calculating the process energy load for both the base and proposed design cases are acceptable for EAc1.
The applicant is requesting acceptance of the proposed energy modeling methodology for a process dominated project. While the overall process for exceptional calculations seems reasonable, the applicant must make the following changes to the calculation methodology: 1. Include all loads in the same model and not in two separate models. This will allow the models to accurately reflect any interactions between the process loads and the space conditioning loads. 2. Provide a side-by-side comparison of the industry standard equipment, its age with the new proposed equipment and define an energy efficiency metric for each piece of equipment (e.g. kWh/ pound of material processed). Also provide list of modifications that make the new equipment more efficient. 3. Provide detailed utility bills from the comparison facility for reference. 4. Provide the operation schedules for the facility and the equipment. Please note that while this Credit Interpretation Ruling provides guidance on the exceptional calculation methodology, the actual savings and credit available for the strategies will be determined only during the review of the actual documentation. Applicable Internationally.
Our project is a new-construction library building, in a northern climate, with 5-stories underground (below grade) and 1 story above ground with a dome-shaped glass wall/roof structure. The glass dome is egg-shape in design (if the egg were on its side half buried in the ground), and encompasses one floor of occupied circulation and office space. The 5-stories underground will serve as climate-controlled mechanized book storage and retrieval, with little regularly occupied space. The project is designed and located to be in good standing for LEED certification, though the glass wall/roof design creates some questions about obtaining the minimum of 2 credits under EA Credit 1. We have spoken with a USGBC representative who recommended that we consider the three following assumptions when we compare the baseline energy model to the design case model. We would like to clarify whether these assumptions are correct with regard to building compliant energy models for this project. 1) The underground 5-stories of the building will be primarily climate controlled book storage, which we feel is a very energy efficient approach to design. We assume that for the energy model, our baseline building will be an above ground building (6 stories total) with typical wall construction. 2) The glass dome structure that serves as the ground floor walls and roof has clear viewing fenestration from grade to 14 feet. The dome is a total of 35\' tall. None of the fenestration is "vertical" glazing, it is at an angle that would deem it a skylight under a strict interpretation of ASHRAE 90.1-2004, though the dome is serving as a combined roof and wall structure. We propose treating the first 14 vertical feet of glazing as wall area (with 100% glazing according to ASHRAE 90.1-2004) in the design-case energy model, and the remaining vertical feet of dome area (from 14\' to 35\') as skylight (100% skylight, according to ASHRAE 90.1-2004) in the design-case energy model. 3) If the first 14 vertical feet of glass is treated as wall area in the design-case model, it would then represent a given percentage of wall glazing in the baseline energy model (represented as an above-ground building). To achieve a 14% improvement in the performance of the designed building, the design-case energy model will still be challenged by the ASHRAE 90.1-2004 allowance of a maximum 5% skylight area on the baseline energy model -against which we will be comparing our design-case model that has 100% of the roof area as a skylight. To summarize, this project is in good standing for LEED certification but we require clarification on our assumption that the baseline-case building would be an above-ground structure, that the first 14\' vertical feet of angled dome fenestration be treated as wall area in the design-case model, and that this respective area of fenestration would be used as wall glazing on the baseline model.
The applicant is seeking a variance in the manner in which the baseline and proposed buildings can be modeled for a very specific design condition. The following responses address the numbered items in the request. 1. The proposed approach is not acceptable. Please note that the modeling methodology used for this credit is not intended to be used solely to demonstrate compliance, but rather to reward significantly better performance. It is therefore an unfair comparison to model the baseline completely above grade. The below grade wall should be the same in both the baseline and design cases. Comparing the design case to an above grade baseline is not acceptable per the modeling protocol. To demonstrate better envelope performance than that prescribed by ASHRAE 90.1-2004, it is important that the design team make necessary modifications to the proposed envelope design. 2. & 3. Your suggested approach is acceptable. Please note that the baseline model will only have 5% of the roof area as skylight. The applicant must provide surface area calculations in a narrative format to demonstrate that the total area of wall plus roof is identical in both the models.
Our project is subject to ASHRAE Standard 90.1-2013 for code compliance. To pursue Option 1: Whole Building Simulation, is there a methodology for documenting additional energy performance for LEED v4 projects regulated by ASHRAE Standard 90.1-2013?
Yes, projects applying Option 1: Whole Building Simulation, and regulated by ASHRAE Standard 90.1-2013 may document additional energy performance improvement under LEED v4 EA credit Optimize Energy Performance as described below. The Appendix G modeling method must be used for the LEED submission, even if the Energy Cost Budget method is used to document local code compliance.
Projects may calculate the Equivalent ASHRAE 90.1-2010 Performance improvement as:
Equivalent performance Improvement = % better than ASHRAE 90.1-2013 + Additional Percent Savings
Projects subject to the v4 2024 update may apply the additional percent savings to each metric (cost, source energy, greenhouse gas emissions)
Where Additional Percent Savings is shown in Table 1:
Table 1: Additional Percent Savings for ASHRAE 90.1-2013
Project Type1 Additional Percent Savings
NC-Office 5%
NC-Retail (except restaurant/grocery) 5%
NC-School 6%
NC-Health Care 3%
NC-Restaurant / Grocery 3%
NC-Hospitality 5%
NC-Warehouse 1%
NC-Multifamily 3%
NC-All Other 2%
CS-Office 3%
CS-Retail (except restaurant/grocery) 3%
CS-School 6%
CS-Health Care 1%
CS-Restaurant / Grocery 2%
CS-Hospitality 3%
CS-Warehouse 0%
CS-Multifamily 1%
CS-All Other 1%
CI-Office 3%
CI-Retail (except restaurant/grocery) 4%
CI-School 6%
CI-Health Care 2%
CI-Restaurant / Grocery 3%
CI-Hospitality 4%
CI-Warehouse 0%
CI-Multifamily 1%
CI-All Other 2%
1 Mixed use buildings shall use the weighted average Additional Percent Savings based on the gross enclosed floor area associated with each building type. Unfinished spaces not submitted in the CS rating system shall use the CS values. Data center space must always be considered “All Other”.
***Updated March 1, 2024 to align with changes in the LEED v4 Energy Update
Many projects in Europe are connected to highly efficient district energy systems. However, the EAp2/EAc1 Option 2 guidance provided in the "Treatment of District or Campus Thermal Energy in LEED V2 and LEED 2009 - Design & Construction" (DESv2) document is not well-suited for the complex interconnected district energy systems with multiple fuel sources that are common in Europe. Many European countries already make use of the Primary Energy Factor (PEF) as a means of evaluating district energy performance and building energy performance. Is there an alternative compliance path available to document EAp2/EAc1 credit for the district energy system using the Primary Energy Factor in lieu of the DESv2 Option 2 compliance path?
An alternative EAp2/EAc1 compliance path is available to document the energy performance for complex interconnected district energy systems in Europe using the Primary Energy Factor and the greenhouse gas emissions associated with these systems. The Sweden Green Building Council developed an approved method, "Treatment of European District Energy Systems in LEED" (available November 1, 2012), which may be used in lieu of EAp2 Option 2 of the "Treatment of District or Campus Thermal Energy in LEED V2 and LEED 2009 - Design & Construction" guidance. This compliance path is currently available for projects located in Europe only. The guidance is located at Note: The "Treatment of District or Campus Thermal Energy in LEED V2 and LEED 2009 - Design & Construction" (DESv2) is Optional Guidance for LEED 2009 projects. However, project teams that use the guidance must apply all relevant portions of the guidance. The alternative compliance path outlined in the "Treatment of European District Energy Systems in LEED" may only be used to replace Option 2 of the EAp2/EAc1 Energy Modeling Path defined in the DES v2 guidance. Project teams that opt to use the "Treatment of European District Energy Systems in LEED" method must comply with all other applicable requirements of the DES v2 guidance such as those defined for EA Credit 3, EA Credit 4, EA Credit 5, etc. Applicable Internationally; only for projects located in the Europe region.
This project is pursuing EA Credit 1, Option 2. We are using the "Advanced Energy Design Guide for Small Office Buildings" (Achieving 30% Energy Savings over ASHRAE 90.1) in lieu of energy modeling, as allowed in LEED NC-2.2. Under the section for "Envelope / Vertical Glazing / Exterior Sun Control (S, E, and W only)", the recommendation for our climate zone (5) is a projection factor of 0.5 for a window with an SHGC of 0.46. Rather than providing exterior shading, we are proposing to use a window with a lower SHGC that will achieve similar performance. This approach is based upon Table 5.5.4.4.1 "Solar Heat Gain Coefficient Multipliers for Permanent Projection" from ASHRAE 90.1-2004, that lists multipliers for projection factors to meet Solar Heat Gain Coefficient requirements. To achieve a Projection Factor of 0.50, Table 5.5.4.4.1 gives an SHGC multiplier of 0.67 to arrive at the adjusted SHGC. The design guide requires an SHGC of 0.46 with a projection factor of 0.5 for our climate. Multiplying the SHGC of 0.46 by 0.67 gives an adjusted SHGC of 0.28. This project is proposing to use a window that meets the SHGC of 0.28 and eliminate the need for exterior projections.
The project team has requested an alternate compliance path for documenting fenestration performance in conjunction with the "Advanced Energy Design Guide for Small Office Buildings." This alternate compliance path would allow exterior shading to be omitted from the project by decreasing the SHGC. The compliance approach outlined above is acceptable. Please use the projection factor for ">0.50-0.60" (0.61) rather than the projection factor for >0.40-0.50 (0.67) described above. Also, provide a narrative with the submittal referencing this CIR, and documenting the revised SHGC requirement for the project\'s climate zone, as well as the installed SHGC. * Note: The ASHRAE Energy Design Guide for Small Office Buildings" was developed based on ASHRAE 90.1-1999, and the corresponding "SHGC Mulipliers for Permanent Projection Factors" table for ASHRAE 90.1-1999 is in Table 5.3.2.3. Applicable Internationally.
Our project is a cold dark shell, suburban retail development registered for LEED NC certification in 2008. The project is a group of eight buildings being submitted for a single LEED certification for the project. Only 3% of the project is core and shell space. Other than this small CS percentage, Tenants\' scope of work includes wall insulation, HVAC systems and interior lighting for the leased area in the project. Tenants will install these components related to EA credit 1. Tenants are not yet under agreement and details of their improvements are not yet known. We intend to meet the intent of EAc1 in part by inserting requirements in the lease agreements for energy optimization of the Tenant installed energy systems and wall insulation levels. We will also provide modeled solutions to Tenant\'s to help guide their initial analyses. Would the USGBC TAG please clarify whether the stipulations of Tenant Sales/Lease Agreements, which are permitted to be used in conjunction with compliance for EAc1 under the LEED-CSv2.0 Rating System, Addendum 2 and errata dated 11/2/2007, are to be modeled identically in the Proposed/Design and Baseline energy models for the tenant spaces, or if Tenant requirements are permitted to be modeled only in the Proposed/Design energy model (while holding the tenant spaces to the standard minimum performance criteria of ASHRAE 90.1-2004 for the Baseline energy model)? CIRs subsequent to the errata allowing the use of Tenant Sales/Lease Agreements have given contradictory or unclear indications on this matter: Some CIRs appear to indicate that baseline and proposed assumptions for Tenant scope must be equal: CIR 5/27/08 - All buildings are to be modeled per ASHRAE 90.1-2004, LEED-CSv2.0 EA Credit 1 and Appendix 2. For items out of owner\'s control, the parameters for the proposed and the baseline models must be maintained as identical. CIR 4/23/08 - Tenant installed HVAC systems are assumed to be identical to the baseline system Other CIRs appear to suggest that lease agreement requirements can be incorporated in the proposed building energy model: CIR 11/14/2007 - It is acceptable to use Core & Shell building efficiency improvements and tenant leasing efficiency requirements to achieve the minimum energy efficiency requirements. LEED-CS errata for EAc1 (dated November 2, 2007) allows a project to meet the EAc1 credit requirements by incorporating tenant sales or lease agreements requirements as part of the tenant scope of work and should be reflected in the project energy model. CIR 11/28/07 - It is acceptable to include the future design for tenant lighting per published erratum. Submit typical lease/sales agreements clearly highlighting the lighting requirements, per the modeling for this credit, that need to be met, as well as how these requirements will be enforced. And other CIRs seem to contradict the above suggesting only Owner installed systems are to be modeled: CIR 4/25/08 - Minimum energy performance and energy savings only applies to systems supplied by the owner. ASHRAE 90.1-2004 clearly states that "spaces shall be assumed to be conditioned space and shall comply with the requirements for conditioned space at the time of construction, regardless of whether mechanical or electrical equipment is included in the building permit application or installed at that time." CIR 8/27/2007; if the work performed is not within the core and shell scope, it can be excluded from the all relevant prerequisite and credit calculations and should be modeled as energy neutral. Given the limited scope of work in the Core & Shell scope of work in our project, is it acceptable to incorporate energy efficiency minimums in the proposed building energy model based on required performance thresholds stated in the tenant leasing agreement documents? Secondly, should we assume that all aspects of the LEED NC App. Guide for Multiple Buildings and Campus Projects can be applied to this LEED CS project? Specifically for EAc1 the AGMBC states, "To receive a single rating for a group of buildings, use a weighted average for the group of buildings based on their conditioned square footage, or aggregate the data into one PRM calculation, so that performance is achieved by buildings of varying sizes within a certifying group. Each building must still meet EA Prerequisite 1 and may receive its own rating if that is desired." If the AGMBC does not apply to our CS project, is it acceptable for our team to analyze energy optimization using a single energy model with appropriate aggregated areas, orientations and loads for all eight of our buildings?
As per the LEED-CS errata dated 11/2/2007, tenant lease agreements are acceptable to claim credit in the Proposed Case models. The applicant should note these requirements are part of the tenant lease and intended to be strictly enforced by the landlord/ owner. In addition, this Core and Shell project may follow the guidance in the LEED-NC AGMBC for EAc1.Update April 15, 2011: Please note that all 2009 projects seeking multiple buildings guidance must refer to the 2010 Application Guide for Multiple Buildings and On-Campus Building Projects, located here: https://www.usgbc.org/ShowFile.aspx?DocumentID=7987Update April 15, 2011: Please note that all 2009 projects in multiple building situations must follow the 2010 Application Guide for Multiple Buildings and On-Campus Building Projects, located here: https://www.usgbc.org/ShowFile.aspx?DocumentID=7987. 2009 project teams should check this document for up to date guidance on all multiple building issues. Applicable Internationally.
Background: Our project is a 3 story, 16,500-sq.ft. addition to an existing 3 story, 84,000 sq.ft. building. The existing building is predominately laboratory space with some office space. The addition will be of similar use. The heating and cooling of the existing building is served by a central utility plant which provides chilled water and hot water via a steam boiler and heat exchanger. It is proposed that the addition also be served by the central plant. The central plant serves several other buildings on the site as well. In order to make a decision on whether we would like to obtain LEED registration on just the new addition or on the entire building with the new addition, a preliminary building simulation is being modeled. For the ASHRAE baseline, the system is modeled as a "System 3 - PSZ-AC" (packaged rooftop, constant volume, direct expansion, and fossil fuel furnace) per table G3.1.1A of ASHRAE 90.1-2004. Though the combined building size would categorize building with addition as a "System 5 - Packaged VAV w/ Reheat.", section G3.1.1(c) mandates conforming to the requirements of System 3 as an exception due to the special pressurization relationship/ cross-contamination requirement of the laboratory. Interpretation Request: Little is stated in ASHRAE 90.1 2004 on the most appropriate way to model a system that has chilled water and hot water heat supplied from a central plant. However, there are a few CIRs concerning similar circumstance that allude to it such as the 1/27/2004-2/24/2004 EA1.1 CIR. In it, it is stated that "While the situation described is not using purchased chilled water or steam, this HVAC description for the budget building is the closest to the proposed design and should be used for the energy modeling purposes." This approach for the budget building model is quite workable since the building owner has costs available for both chilled water and heating hot water. However, the baseline is modeled as a DX cooling and gas fired furnace. Is it appropriate to model the budget building with chilled water and heating hot water, when the baseline model is using neither of these? If not, how should the baseline and budget building be modeled?
The applicant is requesting clarification regarding modeling methodologies for projects which include a central utility plant. Note that the USGBC published a document titled "Required Treatment of District Thermal Energy in LEED-NC version 2.2 and LEED for Schools" in May of 2008 located at the following website: http://www.usgbc.org/ShowFile.aspx?DocumentID=4176 Please refer to this guidance document, which is also referenced in a CIR dated 5/28/2008. Also note that the exception in ASHRAE 90.1-2004 Section G3.1.1 Exception (c) is only applicable for zones that have special pressurization requirements. All zones of the building or addition that do not meet the exception requirements must be modeled using System 5 - Packaged VAV w/ Reheat in the baseline. Applicable Internationally.
The project is a restaurant, where the main Energy Conservation Measure (ECM) is the implementation of an air conditioning system in the kitchen with focus on the thermal comfort in the occupied areas. The building as a whole is divided in two different occupied zones: dining room and kitchen - food preparation. The dining room is fully air conditioned by a rooftop system. Another rooftop was designed to the kitchen. The kitchen space has two distinct thermal zones: the occupied zone, where people work; and the equipments zone, where the equipments are installed. In order to minimize the influence of high internal heat loads from equipments and considering that only the occupied zone must be maintained within acceptable thermal conditions, the mechanical engineer has defined a strategy where the air distribution system guarantees this condition. Diffusers were installed in order to supply the cooled air mainly in the occupied zone. The equipments zone has an exhaust system only. The heat exchange between occupied and equipments zone was considered in the HVAC design, but the focus of the project was the thermal conditions in the workstation only. For the baseline simulation we are considering the total heat gain of the kitchen (people and equipments). Thus, the conventional system modeled in the baseline provides air conditioning for the entire kitchen. For the proposed design model we are considering the air distribution system analogous to an UFAD system, where only the heat gain of the occupied zone is accounted in the total cooling load. Therefore, in the proposed design model, only the occupied zone is conditioned (cooled), though considering a fraction of the heat gain from equipments zone. The heat and mass transfer between occupied and equipments zone were considered to represent the air distribution system in the proposed design. Computer simulation has shown that the strategy applied in this project provides energy cost savings about 10% when compared to a conventional air distribution system in the baseline. To achieve the prerequisite of energy performance, other 4 p.p. of energy cost savings will be achieved with additional strategies, such as an energy efficient lighting system and a solar heating system for hot water supply. This CIR is to confirm that the modeling assumption described above is acceptable to achieve points under EAc1, considering the modeling of a task air distribution system for the proposed design and a conventional system for the baseline.
The applicant is requesting confirmation on the modeling methodology under EA Credit 1 for a restaurant kitchen area. The project team\'s proposed design will exhaust heat gain from kitchen equipment so that it does not add to the space cooling load. This design is considered standard practice, and as a result, no additional energy savings credit can be claimed. Applicable Internationally.
Background: Our project is the 25,000 sf expansion of a school campus including three new buildings - two 1-story structures and one 2-story structure. Our goal is to lower energy use as much as possible, including the selection of process load appliances with low energy use. All of the new spaces in the three new buildings are complete build outs, except four classrooms in the 2-story structure that are being built out as core and shell spaces only. These classrooms will be a low-scale lab environment, metal shop, wood shop or some very light work shop component as yet not defined and will be finished as a future tenant improvement. The scope of our current project does not include the installation of any plug or process load equipment for the core and shell space, only HVAC (heating and basic ventilation only, none for process equipment) and lighting shall be installed. The overall core and shell area of this project is relatively small (3000sf) compared to the overall project area. Proposed Modeling Strategy: For the purposes of documenting the baseline and proposed energy use of this combined full build out and core and shell project, we propose the following methodology. For all completely built out spaces, create a model with baseline energy use including process loads at 25% of total baseline building energy use. The proposed case for the fully built out spaces would have the envelope, systems, lighting and process loads modeled as designed, with documentation available for the new process loads. For the core and shell spaces, since these do not have any associated plug or process loads to be installed at this time, we propose to create a separate model for these spaces that only addresses envelope, lighting, domestic hot water and HVAC systems. This model would provide baseline and proposed case annual energy use for these non-process load related components. Once the annual energy use figures are available for both the full build out and core and shell spaces, it is proposed that the baseline energy use figures be added together for both cases to achieve an overall baseline energy use for the project. Similarly, the proposed case annual energy use would be the combined proposed energy use of the fully built out and core and shell spaces. In this way, an accurate representation of the scope of the project can be modeled for both baseline and proposed cases. Request: Please confirm that the following approaches are acceptable to accurately demonstrate the condition of the proposed building. 1. Is it acceptable to keep the baseline process load energy cost at 25% of the baseline total energy cost, while modeling and inputting the actual installed process loads for the proposed case? This would allow the building to achieve some credit for specifying lower energy use plug and process load equipment than a baseline case. Note that the proposed process energy costs may or may not be 25% of the total energy cost, and may or may not be equal to the process energy load for the baseline case. 2. Is it acceptable for the core and shell spaces to not include process loads in the total energy cost for either the baseline or proposed cases? This would most accurately reflect the project condition. Process loads would be included in the model simulation for the purpose of demonstrating heating and cooling load compliance only, but would be separated out when determining total energy cost for the core and shell spaces. 3. Is it acceptable to create two separate building models for the project, one for the full build out portion of the project and a separate model for the core and shell portion? The core and shell model would exclude process energy cost from its total energy cost. Is it acceptable to sum the total energy costs of the full build out and core and shell spaces to achieve the total project energy cost?
The questions will be addressed in the order that they were presented: [1] It is acceptable to vary the design case process load to reflect energy efficiency measures (ie Energy Start Appliances) that affect the process energy load. This is considered an Exception Calculation Method (ECM) and thus full documentation should be provided justifying the differences and highlighting the assumptions and inputs that were used to create both the baseline and design case process energy loads. It is not allowable to use the default 25% process load value for the baseline case if the proposed case process energy has been inputted piece-by-piece (for example, by inputting the energy usage for each computer, copier, etc.). Instead the baseline model must also have piece-by-piece inputs using identical input power and energy rating as the proposed case unless the applicant can demonstrate that the proposed equipment represents a significant verifiable departure from documented conventional practice. In that case, the values for conventional practice may be used for the baseline equipment with the same use schedule as the proposed case. [2] It is NOT acceptable to ignore process energy usage in future build-out spaces. The LEED Core & Shell Reference Guide provides some guidance in how to address future build-out spaces, though it is more geared to address tenant-leased spaces. Key concepts to follow for future build out spaces include, but are not limited to: [A] Model receptacle and other loads (process) based on estimates for the building type. Table G-B of the ASHRAE 90.1-2004 User\'s Manual (note, this is not the same document as the ASHRAE 90.1-2004 Standard) provides acceptable receptacle power densities, occupancy densities, and hot water usage for varying occupancy types. [B] Use the same values for receptacle and process loads in both the baseline and design cases for the future build-out spaces. [C] If default values cannot be found for certain occupancy types, make reasonable estimates based on modeling and design experience. Please note where these values were used and what estimates are based on. [3] Separate building models for the full build-out and core and shell portions of the project are not recommended. Energy usage calculations are compromised when the model is broken apart because, among other issues, the model is no longer able to apply diversity factors across all project spaces or properly size systems based on peak demand. It may be permissible to separate portions of the model for an ECM, but this is only in the case that limitations in the modeling software prevent adequate representation of the design. If this is the case, full ECM documentation will need to be provided, as described in ASHRAE 90.1-2004 G2.5. Applicable Internationally.
ASHRAE 90.1 does not allow credit for air leakage reduction. However, it does indicate that windows are allowed to have 1 cfm per square foot air leakage (at 0.30" water.) The windows we are using in this project are very high performance, with significantly lower air leakage rates. The manufacturer has supplied test results indicating the tested air leakage rate. Further, we are using a blower door and infra-red camera simultaneously to locate and seal any air leaks in the window system that result from installation. We propose to take credit for this air leakage reduction, with the following methodology:The tested air leakage rate at 0.30" can be established for the windows as installed, based on manufacturer\'s data, and for the base case windows based on ASHRAE 90.1. Both these values will be extrapolated to expected winter heating season air leakage rate, using the LBL correlation for blower door test data. We have run two blower door tests, and will use the most recent (during which most of the air leakage has been taken care of) test data to establish the relationship between the air leakage rate at 0.30" static pressure (75 Pa) and the average heating season air leakage rate, which is calculated at the building pressure established by the LBL correlation, which is based, in part, on the exposure of the building to wind. In this case exposure is significant, as the building is fully exposed on the west side of the building to windows ranging from south to west to north. We then propose to run the base case building, in the energy modeling, using TRACE, with the air leakage rate for the windows established in the above manner. The building as built would be modeled with zero air leakage rate. Preliminary estimates indicate that the difference in overall extrapolate natural air leakage rates in 0.04 air changes per hour, at typical heating season winter conditions. Blower door guided air leakage reduction: A significant effort at air sealing is part of the energy saving strategy for this building. With the location noted above, air leakage reduction is particularly important. Two blower door tests with simultaneous infrared scanning, have been completed. The first identified a number of areas that were not complete as designed. Most of these were completed by the time of the second test, and a number of areas were identified during the second test that, in my opinion, would not have subsequently been air sealed had this procedure not been in place. A list of further items was developed from this second air leakage test, and this list has been circulated by the GC to responsible parties, who will sign off when they have completed the items. When those items are complete, a third, and hopefully final, blower test will be conducted.We propose to take credit in our energy calculations for the air leakage reduction between the second and third blower door tests, using the LBL correlation to extrapolate to typical heating and cooling season air leakage rates, as described in number 2 above. The extrapolated seasonal air leakage rate reduction would be applied to the base case building. For example, if the extrapolated air leakage reduction were 0.1 heating season air changes per hour from blower door test #2 to test #3, we would assign 0.1 ACH to the base case building and zero air leakage to the building as built.We feel that this third round of testing and air leakage reduction is well beyond typical attention paid to air leakage, that air leakage control is particularly important in this very cold (7700 degree-day) climate and at this exposed site, and that we have demonstrated a method using accepted principals to quantify the savings. Blower door test results and LBL correlation spreadsheets for each test would be provided as part of the submission. We would also submit the list of items to be air sealed as part of the final air leakage reduction package. Windows and air leakage reduction together: We propose to add the two air leakage reductions - from window improvements and blower-door-guided air leakage reduction. For example, if the blower-door-guided heating season air leakage rate reduction were 0.1 ACH and the window air leakage reduction were 0.04 ACH, the base case building would be modeled at 0.14 ACH and the building as built at 0.0 ACH.)
**Updated 7/1/2015 with applicability to corresponding EAp2 prerequisites.
Advanced air sealing is a strategy that can lead to measurable energy savings, particularly in cold climates. Although this measure is outside the scope of ASHRAE 90.1 modeling protocol, you may be able to make a case for the significance of this strategy in improving energy performance. However, this will require clear and thorough documentation in order to be considered under the requirements of this credit. The following guidelines are provided to help strengthen your approach:(1) Provide manufacturer\'s air leakage test results that use the same testing protocol as that by which ASHRAE identified the baseline for window air leakage.(2) Use a typical infiltration rate as a baseline, and reduce it by the amount of improvement you can document or estimate from the air sealing strategies employed. Do not use zero infiltration in the model, as this is not a realistic assumption. A zero infiltration strategy would over-emphasize the percentage of overall energy use reduction represented by infiltration improvements.(3) Include required fresh air ventilation rates (per ASHRAE 62) in both the proposed and baseline model results.(4) Provide clear documentation of air sealing strategies and blower door test results, corrected for wind and temperature effects, to clarify anticipated air sealing performance.(5) Provide documentation which clarifies the percentage of energy savings attributed to the air sealing strategy, as opposed to other energy performance measures incorporated into the building. Applicable Internationally.
**Updated January 1, 2014
Advanced air sealing is a strategy that can lead to measurable energy savings, particularly in cold climates, though its effectiveness is especially dependent on the quality of construction and cannot easily be predicted during the design phase. Recognizing this, the ASHRAE 90.1 committee developed Addendum ag to Standard 90.1-2010, which establishes guidelines for claiming energy savings that result from reduced infiltration in Appendix G. The approved change allows credit only for buildings that complete envelope pressurization testing in accordance with ASTM E779. The appendix establishes a baseline air leakage rate of 0.40 cfm/ft2 (2.03 L/s•m2) at 0.3 in. wc (75 Pa) pressure differential compared to the measured leakage results in the proposed building.
Projects wishing to claim energy savings from advanced air sealing may do so given they meet the following requirements:
1. Utilize Addendum ag to Standard 90.1-2010 to document savings.
2. Provide clear documentation of air sealing strategies and air leakage results from ASTM E779-10 Standard Test Method for Determining Air Leakage Rate by Fan Pressurization, including confirmation that all testing criteria defined in the standard have been met.
3. Provide documentation that clarifies how energy savings from reduced air leakage has been estimated from the ASTM E779 test results and identifies the percentage of energy savings attributed to the air sealing strategy, as opposed to other energy performance measures incorporated into the building.
Per ASHRAE 90.1 Appendix G, in order to model an addition excluding the existing building, the HVAC system must be completely separate. Is it acceptable to model the addition separately if it shares steam to hot water heat exchangers with the existing building, but the air handling system is completely independent?
It is acceptable to model the addition separately. Applicable internationally.
This Credit Interpretation Request is in reference to a 92,000 square foot office building and research laboratory that includes a 5000 square foot data center. To obtain credits for Optimized Energy Performance, we plan to estimate the energy consumed using Option 1-Whole Building Energy Simulation as outlined in ASHRAE 90.1, Appendix G. The LEED modeling protocol sets the process load as 25% of the total building energy load. Credit Interpretation for Energy and Atmosphere EAc11 dated 11/3/2006, ruling #5 \'addresses setting the process load at 25% of total energy by default, unless it is a process dominated building\'. The portion of non-regulated energy consumed by the data center equipment and the research laboratory will exceed 50% of the total building load and will dominate the total building energy use. The large non-regulated process load of the data center and research lab will unfairly minimize the percentage of total energy savings applied to the regulated loads. In order to fairly evaluate energy savings of the enhanced building and systems, as well as utilizing photovoltaic arrays, we plan to exclude the energy consumed by the equipment associated with the data center and research laboratory from the energy simulation calculations. It is noted that with the process equipment in the labs and the data center equipment loads, this percentage of energy derived from the PV array will be very small. Is this the proper approach, or should we use the default process load of 25% of the total building load, or the actual loads for these systems?
The project is requesting clarification regarding modeling procedure for buildings where process energy constitutes a large portion of the total building loads. According to Appendix G, Table G3.1.1, "all end-use load components within and associated with the building shall be modeled." The "default" process energy of 25% defines the minimum percentage of process energy that should be modeled for a typical building. However, buildings that exceed this percentage should model the process energy as designed in accordance with the Appendix G requirements. For buildings that are lower than this percentage, the LEED submittal must include supporting documentation substantiating that process energy inputs are appropriate. This process energy may not be removed from the model during post-processing, and must be included when calculating the Baseline Performance, Proposed Performance, and Percentage Improvement. For buildings where process energy constitutes a large portion of the total load, the Baseline HVAC assumptions listed in Appendix G allow for substantial energy improvements for a well-designed HVAC system. According to Exception to G3.1.1, System 3 or 4 (a packaged single zone system) shall be modeled for any space that has occupancy or process loads that vary significantly from the rest of the building, including peak thermal loads that differ by at least 10 Btu/h-ft^2. Therefore, for a building with a large data center, the HVAC energy savings potential relative to the Baseline design is far greater than for a similar office building without a large data center. As a result, the percentage energy savings for a good design may be comparable between the two cases even though the process energy costs as a percentage of total energy are significantly different. Applicable Internationally.
The project is a metal recycling facility primarily used for shredding and separating metal to be recycled. The building is a very process intensive facility containing many large motors - the largest of which is 4,000 HP. ASHRAE Standard 90.1, Appendix G - Table G3.1, section 12 states that for the baseline: "Other systems, such as motors covered by Section 10, and miscellaneous loads shall be modeled as identical to those in the proposed design. Where there are specific efficiency requirements in Section 10, these systems or components shall be modeled as having the lowest efficiency allowed by those requirements." Because such a large portion of the facilities energy consumption will result from the large motors (greater than the 200 HP upper limit of Section 10) it will be difficult to obtain any appreciable improvement over the baseline performance if the baseline large motors (> 200 HP) are to be modeled with the same efficiencies as the proposed design. For these motors that exceed the 200 HP, would it be acceptable to use the minimum efficiencies for 200 HP motors as outlined in Section 10 for the baseline building performance? Or is there another way that we can take credit for using high efficiency motors? Additionally, the project is planning on incorporating many other sustainable features into the project that will allow for us to achieve a Silver, and possibly a Gold rating. However, if 2 points must be achieved from EA credit 1 in order to be certified, then it does not look like we can become certified despite all of the other LEED points we could achieve. Do we need to receive a minimum of 2 points under this credit to be eligible to certify the project under LEED NC version 2.2?
The applicant is seeking guidance regarding how to meet the two-point minimum required for EAc1 for a process-load dominated building. Per CIRs dated 3/23/2007 and 10/24/2008, process loads for the entire facility must be included in the energy simulation. Per the CIR dated 3/23/2007, the baseline HVAC system may be modified according to Exception to G3.1.1(b) in ASHRAE 90.1-2004. Per a CIR dated 10/24/2008, the project team may want to consider attempting to document energy savings for process energy use. The project should use the Exceptional Calculation Methodology (ECM) outlined in ASHRAE 90.1-2004 Section G2.5 to document process energy savings. If attempting to demonstrate process energy savings, the ECM must include calculations and reasonable assumptions for motor efficiency in baseline and proposed cases. Applicable Internationally.
ENERGY & ATMOSPHERE: Minimum Energy Performance (EAp20) 4/30/2005 - Credit Interpretation Request The Saranac is a renovation and historic preservation of a 4 story hotel. The building will be converted into a multi-use facility that will include housing, offices, symposium space, theater and restaurant uses. The building is designated as a contributing structure to the Downtown Spokane National Historic district. the building is also on the local Historic Register and is subject to review of the local Landmark Commission. The design restrictions will result in restoring the storefront and primary elevations to 1900 era appearance. In our case the entire building will be renovated but the esterior appearance of the building will remain largely unchange with the exception of the addition of exterior sun shades on the non-primary elevations. The building systems will be replaced. Can the buildings existing envelope chariteristics be used to extablish the energy usage baseline per ASHRAE 90.1 (Section 4.1.2.2)? 5/23/2005 - Ruling Yes. As established in the EAp2 CIR Ruling dated 3-11-03 and ASHRAE 90.1 Sections 4.1.2.2, the historical facade is exempt from minimum energy performance. Section 11.4.2 also states "for existing buildings, the budget building design shall reflect existing conditions prior to any revisions that are part of this permit." _________________________________ Based upon this CIR I have a question about our current project, the renovation of an existing mill building into spec office space. Please note that the mill building is "specifically designated as historically significant by the adopting authority or is listed in \'The National Register of Historic Places\' or has been determined to be eligible for listing by the US Secretary of the Interior" per ASHRAE 4.2.1.3. I would like to confirm the following: 1. This CIR which was filed for a New Construction project applies to a Core and Shell project. Please confirm. 2. We believe this CIR allows us to use the original facade/envelope conditions to set our minimum energy performance as required for EA Prerequisite 2. Please confirm. 3. We believe this CIR allows us to run our energy model using the original facade/envelope design conditions to set the baseline for energy model comparison with the renovated facade/envelope design. Please confirm. 4. When we compare the original envelope against the renovated envelope (which can only consist of new windows and added roof insulation per the Historic Registry guidelines) our energy performance, based upon cost, increases by 23%. -We believe that this means we meet EA Prerequisite 2. Please confirm. -We also believe that under credit EA-1 we would qualify for 6 points as this is an Existing Building Renovation. Please confirm.
Based on the information provided, it appears that the requirements for EAp2 have been met and if this project achieves 23% savings in energy, incumbent on verification of documentation submitted during the review process, it would qualify for 6 points for an existing building renovation. In response to the questions raised: 1. This particular CIR, which was filed for a New Construction project, can be applied to a Core and Shell project. 2. Yes, the referenced CIR and ASHRAE 90.1-2004 Section 4.2.1.3 Exception (a) allows the project to meet the minimum energy performance requirements of EAp2. 3. This issue is unrelated to the original CIR, but the approach is acceptable under the requirements of ASHRAE 90.1-2004 Table G3.1 No. 5, (f) under Baseline Building Performance, which states that "for existing building envelopes, the baseline building design shall reflect existing conditions prior to any revisions that are part of the scope of work being evaluated." Applicable Internationally
LEED Core and Shell projects are is allowed to show energy savings associated with tenant improvement measures if documented in the lease agreement. Can anchor tenant leases, were executed well before the start of design, also be used? As a result of timing issues, it is not always practical to include specific energy efficiency measures in the lease agreement. Many of our tenants, especially supermarkets and other anchors, are extremely interested in energy efficiency and include these measures in their build-outs. All of these measures are documented in the tenants' construction drawings, which are typically completed simultaneously with the core and shell drawings. We desire to be able to include tenant energy efficiency measures that are documented in the tenants' construction drawings in the LEED for Core and Shell energy model. We would argue that this approach has more certainty and credibility than measures documented in the lease agreement. We would be using measures in permitted, final construction drawings, not requirements that were agreed to during lease negotiations. Please confirm that the LEED for Core and Shell project can include energy efficiency measures documented in the tenant's final construction drawings as part of the LEED for Core-and-Shell energy model.
The energy efficiency measures for tenant spaces documented in the tenant's final construction drawings can be used as part of the LEED Core and Shell energy model if the tenant signs a letter confirming that the final construction documents will be implemented as designed; that any modifications to the final construction documents will be evaluated for their impact on energy efficiency; and that the overall efficiency savings contributed by the tenant improvements will be maintained between the final construction documents and the construction phase. Applicable internationally.
The project consists of a single story 6,300 sf office building attached to a 160,000 sf manufacturing facility. The issue is how to model the heated only manufacturing area. The requirements from ASHRAE 90.1-2004, Appendix G state, "all conditioned spaces in the proposed design shall be simulated as being both heated and cooled even if no heating or cooling system is to be installed." Furthermore, "where no cooling system exists or no cooling system has been specified, the cooling system shall be identical to the system modeled in the baseline building design." These ASHRAE 90.1 requirements indicate that the proposed Constant Volume, 100% Outdoor Air, Gas-Fired, Make-Up Air Unit would need to include the baseline Variable Volume, 100% Outdoor Air, Chilled Water, Packaged Rooftop Unit for cooling. Current industry energy modeling software, approved by ASHRAE 90.1, cannot model this system for a single space. It also is unrealistic to compare the proposed Make-Up Air Units to a VAV w/Reheat System in a manufacturing facility. Our design team suggests that any heated only space should be modeled as heated only (no cooling) for the proposed and baseline model. This is mainly because if it were possible to model the "imaginary" cooling system for heated only spaces it would provide the project with unwarranted energy credit or debit. Specifically, if the loads were reduced between each simulation, for reasons such as improved insulation, the project could use less electricity and therefore gain energy credit from a cooling system that does not exist. Please advise if our recommended procedure to model "heated only" spaces is acceptable, and if not, what is the USGBC\'s recommended method to comply with ASHRAE 90.1-2004 requirements in this instance?
The proposed modeling procedure does not comply with the requirements of ASHRAE 90.1-2004, Appendix G, which is the referenced standard for the purpose of the credit. Table G3.1, #10(d) states clearly: "(d) Where no cooling system exists or no cooling system has been specified, the cooling system shall be identical to the system modeled in the baseline building design." There isn\'t sufficient information about the design HVAC system provided in the request, to identify the correct baseline system configuration. If indeed there is no simulation tool that is capable of modeling the systems, the Exceptional Calculation Method (Section G2.5, Appendix G) should be employed. Table G3.1, # 13. Modeling Limitations to the Simulation Program states clearly "If the simulation program cannot model a component or system included in the proposed design explicitly, substitute a thermodynamically similar component model that can approximate the expected performance of the component that cannot be modeled explicitly." Applicable Internationally.
Our project is a Graduate University located in Saudi Arabia dedicated to the research of alternative fuels and renewable energy. The entire campus will be New Construction and will consist of research labs, lab support areas, administration buildings, a library, a commons building, food service, an auditorium, conference rooms, lecture halls, offices and public areas. The Campus will also contain a Greenhouse structure. Since the ASHRAE Standard 90.1-2004 does not apply to buildings or portions of buildings that use energy primarily for commercial of industrial processes, our project team is proposing that the energy use in the greenhouse would most likely be considered process related load for the Performance Rating Method. Energy use in the greenhouse will not be used for occupant comfort. Please confirm that this approach is acceptable.
The applicant is requesting clarification regarding whether energy used in a greenhouse that is part of a campus application should be considered process load using the ASHRAE 90.1 Performance Rating Method. Any of the energy end-uses in the greenhouse that are deemed necessary for the comfort of occupants (e.g. ambient lighting, spot cooling, etc.) should be reported as regulated end-uses. Space conditioning equipment and lighting used primarily to support plant growth functions should be reported as Process energy in the EAc1 template Tables 1.8.1 and 1.8.2. Please be sure to separately report the process space conditioning energy from other process equipment energy. Treatment of Envelope: If the primary function of the building envelope for the greenhouse is to achieve the solar and thermal conditions required for plant growth, the envelope may be excluded from the prescriptive requirements of ASHRAE 90.1; and the envelope should be modeled identically in the Baseline and Proposed Case. [Note: this does not extend to other building types, such as manufacturing facilities, or others, where the envelope is not directly tied to meeting the process functions]. Treatment of Lighting: Lighting should be modeled using the Space-by-Space or Building Area Method, and should apply any applicable exceptions provided for in Chapter 9. For example, Section 9.2.2.3 specifies "lighting for plant growth or maintenance" as unregulated lighting, which should not be included in the interior lighting power allowance (this lighting must have a separate control device (Section 9.4.1.4(e)). This lighting still should be included in the energy model as process lighting, and should be modeled identically in the Baseline and Proposed Case. Treatment of Space Conditioning: If the space conditioning / humidity control systems are primarily designed for maintaining the conditions required for plant growth, and are not used to maintain occupant comfort, the space conditioning system type and controls should be modeled identically in the Baseline and Proposed Case. Mandatory equipment efficiencies from Tables 6.8.1A-J, and any other mandatory measures from Chapter 6 with their applicable exceptions do apply to the Greenhouse space conditioning systems. The baseline case process air conditioning system should be modeled as meeting the minimum equipment efficiencies from Chapter 6. The proposed case should be modeled with as-designed equipment efficiencies. An informed determination can only be provided during LEED certification review if the requirements ASHRAE 90.1 Section G2.5 guidance are satisfied (i.e., provide theoretical and empirical information verifying accuracy). Applicable Internationally; Saudi Arabia.
This project is to renovate 300,000 square feet of an old factory and convert to a distribution center. The owner strongly desires to be sustainable and will use many sustainable features whether or not LEED certification is sought. We will use high efficiency lighting and high efficiency infrared heaters, but no cooling. If we use the ASHRAE appendix G, we have to model the baseline cooling system for the baseline and the proposed. Since the cooling energy will be much larger than the heating energy the 14% reduction from ASHRAE will not be possible. This force the project to be penalized for energy never actually used. In this case we feel that the ASHRAE standard does not rationally apply. This project will reuse a large facility and incorporate significant sustainability features and we would not like to be excluded because the ASHRAE standard does not apply logically to this facility. Is there any alternative method for compliance in this situation?
The project has requested clarification regarding the use of the ASHRAE Baseline requirements in Appendix G. Although a cooling system must be modeled in both the Baseline and Design case, there are no requirements for Temperature Setpoint. Therefore, both cases may have the Cooling Temperature Setpoint elevated such that both systems do not ever run and thus does not consume any energy. Applicable Internationally.
The project is a major renovation of primarily the common areas in a 37-year old, one and two story, multi-tenant retail mall. The mall was originally designed, permitted and built as an open air mall where the tenants were grouped into multiple buildings with common areas open to the sky between them. During the 1980s, these common areas were enclosed using separate structural and mechanical systems. The total building area inside the LEED boundary is 500,575 sf. The common areas encompass 145, 282 sf. The tenant areas are aggregated in sectors from 20,000 sf to 50,000 sf and separated by one and two hour fire rated exit corridors (the common area of the mall). Both the common and tenant areas of the mall are independently conditioned with multiple small, air-cooled, roof-top systems ranging from 1 to 20 years of age. One of the main goals of the project is to decrease the building\'s energy and carbon footprint by incorporating an extensive HVAC upgrade package to the common areas and requiring all new leases to incorporate sustainable guidelines including HVAC equipment that exceeds ASHRAE 90.1. Question: Will it satisfy the requirements of CS EA Prerequisite 2 and EA Credit 1 to classify the tenant spaces and common areas of an existing multi-tenant retail mall as separate adjacent buildings similar to the requirements found in the LEED for Multiple Buildings under NC v2.2 for the purposes of determining the baseline HVAC system type(s) as defined in ASHRAE 90.1 Table G3.1A? Proposed Interpretation: The design team proposes to classify each tenant sector and the common area as separate campus buildings at the location of the fire rated partitions for the purposes of establishing the baseline HVAC system type. This would allow the baseline HVAC system types for the tenant areas (75,000 sf &
The applicant is requesting clarification regarding the term "building" as it applies to energy efficiency modeling for a multi-tenant retail mall that was previously converted from an outdoor mall to an indoor mall with indoor common areas. From the description provided above, it appears that the retail mall should be classified as a single building: the common areas are directly connected to all of the retail spaces and/or the retail spaces are connected to one another; significant transfer of air is likely between the retail spaces and the common area spaces; and the use of the building (as a retail mall) is consistent throughout the whole project. There was no strong justification provided by the applicant to justify why the retail spaces should be considered as separate buildings. Therefore, the project should be considered a single building. Applicable Internationally.
Ours is a project in India wherein we plan to use high efficiency centrifugal chillers. We have a query on fixing the standard COP which needs to be considered in the baseline. As per the ASHRAE 90.1 2004 standard, for centrifugal chillers of capacities more than 300 TR , the baseline efficiencies are selected as per the table 6.8.1C, when tested under ARI 550/590 conditions. For chillers which operate outside the ARI conditions i.e. non standard conditions, ASHRAE 90.1 2004 refers to a sliding chart as per table 6.8.1J given in page 53. This chart also shows a calculation to arrive at K (adj) factor which has to be multiplied with the COP std (i.e. 6.1) to arrive at COP (adj) as per the site conditions. Accordingly, for our project, we have made a detailed calculation. The building would have centrifugal chillers of capacities 400TR, 600TR and 820TR and the operating site conditions are as follows: Leaving chilled water temperature : 44 deg F Entering condenser water temperature : 90 deg F We have arrived at the K (adj) factor based on the calculations shown in page 53 of ASHRAE 90.1 2004 as follows: BASELINE COP CALCULATION FOR CENTRIFUGAL CHILLERS COPadj = Kadj x COPstd Where, COPstd = 6.10 Kadj = 6.1507 - 0.30244(X) + 0.0062692(X)2 - 0.000045595(X)3 X = Condenser DT + Lift Condenser DT = Leaving Condenser Water Temperature (Deg F) - Entering condenser water temperature (Deg F) Lift = Entering Condenser Water temperature (Deg F) - Leaving Chilled Water Temperature (Deg F) X = Condenser DT + Lift = (100 - 90) + (90 - 44) = (10) + (46) = 56 Kadj = 6.1507 - 0.30244(X) + 0.0062692(X)2 - 0.000045595(X)3 = 6.1507 - 0.30244(56) + 0.0062692(56)2 - 0.000045595(56)3 = 0.86 COPadj = Kadj x COPstd = 0.86 x 6.10 = 5.28 NPLV CALCULATION : NPLVadj = Kadj x NPLVstd Where, NPLVstd = 6.40 NPLVadj = Kadj x NPLVstd = 0.86 x 6.40 = 5.50 We need clarification as to whether a COP of 5.28 at 100% load and NPLV of 5.5 can be considered as the basecase efficiencies while carrying out energy simulation for the building.
The applicant requests confirmation regarding their calculation methodology for determining the efficiencies of the Baseline chillers. The calculation methodology provided above is not correct, because it does not take the required operating conditions for the Baseline Case plant equipment into account. Per the requirements of Appendix G, the Baseline Chilled Water Loop shall be modeled with a chilled water design supply temperature of 44 deg. F, and a return water temperature of 56 deg. F (G3.1.3.8); Condenser water shall be 85 deg. F or 10 deg. F approach to design wet-bulb temperature, whichever is lower, with a design temperature rise of 10 deg. F (G3.1.3.11). For a project >= 240,000 square feet, 2 centrifugal chillers minimum shall be modeled with chillers added so that no chiller is larger than 800 tons, all sized equally (G3.1.3.7). These conditions described for the Baseline Case model are standard ARI 550/590 test conditions; therefore, the efficiencies modeled for the Baseline case should reflect the minimum efficiencies given in Table 6.8.1C, and should not reference the values given in Table 6.8.1J. Please note for Energy & Atmosphere Prerequisite 2 (EAp2) that there is also a mandatory requirement within ASHRAE 90.1-2004 that the installed equipment in the proposed design must meet the minimum efficiencies given in the 6.8.1 Tables. The calculation methodology described above is the correct calculation methodology to determine the mandatory performance that the chillers must meet in order to meet for EAp2. Applicable Internationally; India.
Can the baseline model for refrigerated facilities be determined based on the IARW/IACSC Energy Modeling Guideline for Cold Storage and Refrigerated Warehouse Facilities as an exceptional calculation methodology under Appendix G?
Yes, project teams may use the IARW/IACSC Energy Modeling Guideline for Cold Storage and Refrigerated Warehouse Facilities as an exceptional calculation methodology when ASHRAE 90.1-2010 is used for compliance with EA Prerequisite Minimum Energy Performance. This guideline may not be used when an equivalent code is used for compliance unless approved by a project-specific Credit Interpretation Ruling. The following additional requirements apply:
1. Refrigerant type may not be used as an efficiency measure.
2. Table 1.4 must be completed for both the portions of the building complying with the IARW/IACSC Guideline as well as those following the standard ASHRAE 90.1 Appendix G requirements
3. If ASHRAE 62.1-2010 Addendum L is applied using the IARW/IACSC Guideline, it must be applied consistently throughout the project submittal.
4. Projects applying the IARW/IACSC Guideline may apply LEED Interpretation 10237 in order to claim energy savings for refrigeration equipment efficiency as an exceptional calculation methodology.
Internationally applicable as follows: The guidance applies to compliance paths using ASHRAE standards and cannot be applied to projects using an equivalent local code. Project teams wishing to apply this to an equivalent local code must obtain approval through a project-specific credit interpretation ruling.
This ruling supersedes the following LEED Interpretations: LI 5178, LI 2301, and LI 2026.
Is a model required to use the prescriptive Tables 5.5-1 to 5.5-8 for the existing envelope thermal parameters for all spaces converted from unconditioned to conditioned, or in the baseline model, could you use the existing thermal parameters regardless of changes in space conditioning as per Appendix G Table3 G3.1.5 and LEED Reference Guide for Green Building Design and Construction?
Section G3.1.5 assumes that the space type classification for the space has not changed. If the applicant is changing an unconditioned space to a conditioned space, the applicant must model a minimally compliant envelope as per tables 5.5-1 to 5.5-8 in the baseline models. Applicable internationally.
Project is pursuing EA Credit 1 points under OPTION 3 - PRESCRIPTIVE COMPLIANCE PATH: Advanced Buildings Core Performance Guide. The proposed building is a 50,000 sq. ft. office building located in climate zone 3a. According to ASHRAE Standard 90.1 2004 an air-side or water-side economizer is not required, although the project will utilize water-side economizers. Section 2.13 of the Core Performance Guide details performance and operational requirements of air-side economizers but does not mandate the usage thereof. We have three related questions: 1) Must a project have air-side economizers to comply with Section 2.13 of the Core Performance Guide? 2) If an economizer is required, can a water-side economizer be utilized in lieu of the air side economizer. 3) The EAc1 Template does not make provision to document Option 3. What documentation and template format is required in order to document the points claimed under Option 3?
The applicant is requesting clarification to various economizer related issues associated with NBI\'s Core Performance Guide. The following responses address the number items in the request. 1) Yes, air-side economizers must be installed. Section 2.13 of the Core Performance Guide states the purpose of the requirements and criteria are established to ensure the proper performance of outside-air (OA) economizers. 2) No, water-side economizers are not an acceptable equivalent to air-side economizers. 3) It is recommended that for submission a signed LEED EAc1 Submittal Template declaring compliance with Option 3, a document comparing and supporting, at minimum, that prescriptive requirements stated in sections one and two of the Core Performance Guide have been satisfied. Above these requirements, it will be left to the discretion of the team if additional documentation is needed to support credit compliance. Applicable Internationally.
ASHRAE 90.1 sets specific requirements for the building envelope, including meeting all requirements of Section 5.4. Air Leakage, Section 5.4.3, requires sealing, caulking, gaskets and weather stripping of the building envelop to minimize air leakage. For the Barkesdale Dormitory, additional methods were used to minimize air infiltration. Additional barriers, taping, and low leakage panels per ASTM E283-84 (0.06 cfm per square foot of fixed wall at 63.3 mph wind and 1.92 iwg.) were used. Additionally, the building was pressurized to prevent infiltration. A baseline building model is neutral with average construction. With the value added benefit of additional barriers, taping and low leakage panels and pressurization, the Barkesdale Dormitory can be considered a "tight-pressurized construction". These differences could effect the energy calculations. Is this a logical conclusion?
This CIR seeks to use reduced infiltration rates from a superior building envelope as a variable in the energy cost budget calculation for optimizing energy efficiency. The ASHRAE modeling protocol does not allow the infiltration rate to be changed between the budget and the design case. The CIR ruling of 3/11/2003 for EAc1.2 provides some guidelines on how a case might be made for advanced air sealing. The methodology proposed for this project does not address all the issues raised in that ruling and would be insufficient to grant an exception to the modeling protocol. Applicable Internationally.
Our project is a newly constructed, 825,751 square foot automotive manufacturing facility in the midwest. The ventilation requirements for our facility, as set forth by ASHRAE 62.1, Section 2.2 states: "Additional requirements for laboratory, industrial, and other spaces may be dictated by workplace and other standards,.". Industrial facilities in this location fall under the requirements of the Michigan Occupational Safety and Health Administration (MIOSHA). Per MIOSHA\'s, health standards ("Part 520. Ventilation Control"), R325.52007 Exhaust ventilation systems, Rule 7 states : "The minimum rate of exhaust ventilation for places of manufacturing, processing, assembling, maintenance and repair, or storage of material shall be 1 cubic foot of air per minute per square foot of floor area. This amount of exhaust ventilation may be provided by local exhaust, general exhaust, or both. The director may permit a variance if contaminant control is accomplished at a lesser rate of ventilation." MIOSHA has stated that an allowable level of contaminant control for dust/mist particulate would be 5 mg/cubic meter. In an attempt to save ongoing heating, cooling and ventilation expenses, the Owner chose to design the new facility in an innovative manner that could attain contaminant control at a much lesser ventilation rate than the default 1 CFM/SF that is set forth by MIOSHA and used by other automotive manufacturing facilities. The manufacturing facility has set a target of 0.5 mg/cubic meter, significantly lower than the MIOSHA required level of contaminant control. In order to reach this high level of contaminant control, they implemented the following innovative approaches: 1 - For the machining and grinding processes, enclosures were constructed and oil mist/dust collection systems were implemented with HEPA filtration. 2 - For the parts washers, enclosures were constructed and local exhaust ventilation systems were designed to capture contaminants at the source. 3 - For processes using hazardous materials, local exhaust ventilation systems were designed to capture contaminants at the source. 4 - "Dry floor guarding" systems have been implemented in the machine tool enclosures in order to minimize any escaping mist from the process. 5 - Micro-bacteria resistant coolants are used in the plant and biocides and utilized and monitored in order to control the bacterial counts in such systems. These control measures are over and above what is done in a typical, newly constructed manufacturing plant. With these control measures being utilized, extensive testing was done through the manufacturing facility to ensure that MIOSHA (and the much more stringent company requirements) exposure limits were being met. During the testing, the facility was ventilated at a rate of 0.21 CFM per square foot. At this ventilation rate, the facility was far below the company\'s target exposure limits, never measuring higher than a 0.13 mg/cubic meter exposure level. The Owner operates their facility at a ventilation rate of 0.5 CFM per square foot. This adds another level of safety factor to the building design. We are proposing that we run the energy model, in both the baseline and proposed case, with a ventilation rate of 1.0 CFM per square foot. We then intend to use the Exceptional Calculation Methodology of ASHRAE 90.1 to quantify our energy cost savings by lowering the ventilation rate. We intend to re-run our "proposed" model with 0.5 CFM per square foot to determine the cost savings for this exceptional calculation.
The applicant is proposing that energy savings due to ventilation load reduction resulting from several pollutant source control measures be approved as an Exceptional Calculation Methodology (ECM). The use of baseline and proposed case exhaust rates above those required by ASHRAE 62.1-2004 Section 6.2.8 are acceptable per ASHRAE 62.1-2004 Section 2.2 and the requirements specified by Michigan Occupational Health and Safety Administration (MIOSHA). Since it is a non-regulated process load, the project team must establish reasonable assumptions under full operational conditions for the baseline and proposed case. It appears that the project team has put a substantial effort into identifying and controlling sources of indoor pollutants and in an effort to reduce ventilation loads. Additionally, testing has been conducted to verify that the particulate concentrations are well below MIOSHA requirements even at reduced ventilation rates. The proposed documentation of energy savings from ventilation load reductions in the proposed case may be documented as an ECM. Please note that the favorable ruling of this CIR does not guarantee credit acceptance during a review. The project team should provide sufficient documentation to support the proposed ECM. Also note that the ruling is specifically applicable to the project in question due to the substantial efforts made to control sources of indoor air contamination at the source and testing for compliance; the ruling is not necessarily applicable to projects with different circumstances.
This question is in regard to a mixed use series of buildings planning to apply for certification as a LEED CS Campus project. The project is designed to be built containing no interior public common areas. The only common area air conditioned space will be the elevator mechanical room. The interior tenant spaces within the project will be built only to raw shell specifications with no electrical or mechanical fixtures or finishes, lighting or air conditioning. All interior lighting and HVAC equipment for specific tenant areas will be installed by the future tenants. Only exterior project lighting will be provided by the Developer. Therefore, the question is as follows: What is considered baseline for energy use by USGBC in a CS Campus building project, where the core and shell is delivered in a raw shell condition, with no interior lighting or HVAC to be installed by the Developer?
The applicant is requesting clarification regarding what is considered the baseline for energy use in a Core and Shell building where all interior lighting and HVAC systems will be installed by the tenant. Concerns relating to modeling for CS applicants are outlined in the LEED-CS Reference Guide under Core and Shell Modeling Guidelines and Core and Shell Concerns and Calculations. Interior lighting in the baseline building should be modeled using the Building Area method or the Space-by-Space method as defined in ASHRAE 90.1-2004, Table 9.5.1 or 9.6.1. The baseline building HVAC system should be based on Table G3.1.1.A and Table G3.1.1B in ASHRAE 90.1-2004. Where no heating or cooling system exists in the proposed building, or, the system will be installed by the tenant and is unknown, the system characteristics in the proposed building shall be identical to the system in the baseline building design according to ASHRAE 90.1-2004, Table G3.1 (10) and LEED-CS Reference guide. Table G3.1 (10) in ASHRAE also states that, if no proposed heating system exists, the baseline system determined in Table G3.1.1.A should be electric. In addition to HVAC systems and lighting, the project should also include equipment and process energy according to certain requirements outlined in the LEED-CS Reference Guide. It is important to point out that in the case of Core and Shell buildings, not only the baseline, but also the proposed building needs to follow a certain modeling protocol to meet Option 1- Whole Building Energy Simulation in accordance to LEED-CS. Since tenants install all or part of HVAC systems, lighting, equipment etc, and full design might not exist, certain stipulations need to be incorporated in the proposed building simulation as well. In addition, tenant spaces are treated separately to core and shell spaces in the outlined requirements in LEED-CS. Concerns relating to modeling for CS applicants are outlined in the LEED-CS Reference Guide under Core and Shell Modeling Guidelines and Core and Shell Concerns and Calculations. The applicant is recommended to study theses guidelines carefully since these guidelines should be followed in parallel to ASHRAE-90.1-2004, Appendix G. Applicable Internationally.
We request the USGBC confirm our understanding that the 90.1-1999 ECBM and LEED modeling protocol allows us to receive credit for EAc1 energy cost savings for desuperheaters recovering heat from water source heat pump compressors, and using this heat to preheat service water heating, and that this can be done without an Exceptional Calculation, with the supporting discussion below. We understand that the heat recovery method would qualify as site-recovered energy as discussed under section 11.2.3 and its Exception, and is not included in the design energy cost, and the equivalent usage is met in the budget model by the backup energy source, which is electricity. Therefore, the measure is eligible for savings credit and to be modeled differently in the design model from the budget model. The desuperheaters and their heat recovery to service water heating can be readily modeled within eQuest and its computational engine, DOE-2.2, and therefore do not become an exceptional calculation for that reason. Therefore, the measure appears eligible for savings credit, and does not seem to require an exceptional calculation. Is this approach considered acceptable?
The applicant is requesting clarification regarding whether desuperheaters must be modeled using the exceptional calculation methodology when the energy software program used for EAc1 compliance is capable of modeling heat recovery. The exceptional calculation methodology is only required when one of the following conditions are met: 1. The simulation program being used for the LEED EAc1 calculations cannot adequately model a design material or device 2. Input parameters that ASHRAE 90.1 requires to be modeled identically in the budget and proposed case must be modified to show the impact of the efficiency measure (e.g. schedule changes must be used to demonstrate improved efficiency, such as for demand control ventilation). 3. Previous LEED CIRs have mandated the use of the exceptional calculation methodology (e.g. - eQUEST is capable of modeling demand controlled ventilation, but since eQUEST accomplishes this by internally editing schedule values, the exceptional calculation methodology is still required for LEED v2.1 projects). In the case of desuperheaters, ASHRAE 90.1-1999 specifically requires condenser heat recovery to preheat service hot water under certain conditions (Section 6.3.6.2). Since heat recovery is prescriptively required under certain conditions, and since the software is capable of modeling desuperheaters without the use of supplemental spreadsheet calculations, the measure may be modeled without using the exceptional calculation method. The applicant should be sure to include all input assumptions regarding the desuperheaters in the input comparison table, and should provide sufficient information to confirm that condenser heat recovery does not have to be modeled in the budget case under the requirements of section 6.3.6.2. Applicable Internationally.
The project undergoing the LEED process is an 847,218-sf warehouse with 22,776-sf of support offices in the same building. Eight (8) high-efficiency gas-fired rooftop units are proposed for providing heat to the warehouse space to maintain a 54-degree setpoint during the occupied hours of operation and a 50-degree setpoint during unoccupied hours (only heating provided to warehouse). The office area is proposed to be conditioned with high-efficiency gas-fired heating and DX cooling rooftop units serving separate interior and exterior spaces. The heating system for the warehouse is only designed to maintain setpoints intended to protect fire suppression sprinkler piping and other domestic piping systems from freezing during the winter. The heating and cooling system for the office area is designed to maintain temperature set points during the summer and winter for human comfort. The proposed control sequence for the warehouse rooftop units is to start the units two at a time with a dead-band of 3 degrees Fahrenheit - such that if the space temperature set point during winter is not maintained through the use of two units, two additional units will start, etc. The total heating output capacity of the eight (8) rooftop units proposed for the warehouse is higher than the heating load requirements for the purpose of safety and redundancy. The proposed rooftop units are direct-fired 80/20 units that also must be sized to maintain slight positive pressure when the overhead doors are closed. As per load calculations with Trace700 software, the warehouse falls under the semi-heated space category. As per total output capacity (of the direct-fired rooftop units sized for building pressurization), the warehouse falls under the conditioned space category. If we must consider the warehouse as a conditioned space, using Appendix-G of 90.1 performance rating method, the baseline case for both the warehouse and the office space is System #7: Variable Volume with Re-Heat, chilled water cooling and hot water boiler. The use of VAV system #7 as the baseline model for an energy modeling comparison is not reflective of a real-world system for a warehouse building. The proposed system for the warehouse that would need to be modeled in this case would be Constant Volume Rooftop Units with gas heat exchanger and chilled water coils. The proposed office system is Constant Volume Gas-fired Rooftop Units with DX cooling. The system type actually being proposed for this project is commonly used for all warehouses in this country. The energy savings that will be attained from our improved-efficiency of mechanical equipment, reduced lighting power density and improved building envelope performance will only be accurately reported if the proposed design is compared to a realistic baseline. Questions: 1. Can we consider the warehouse as a semi-heated space on the basis of heating requirements per peak load calculations and compare the baseline and proposed cases per the semi-heated space criteria? 2. The ASHRAE Standard 90.1-2004 page G-23 allows a building to be modeled with separate system types for separate occupancies (such as residential and non-residential). Can we treat warehouse and office spaces under separate occupancies and model these spaces with separate system types?
The applicant is requesting a waiver from the requirement of modeling a conditioned space as per ASHRAE 90.1-2004. Please note: 1) A semi-heated space classification is based on the peak output of the equipment installed, and as described in the narrative, this space would not qualify. 2) Yes. If the office area is greater than 20,000 ft^2 of conditioned floor area, the project can be modeled as a separate system as per G3.1.1, exception (a) of ASHRAE 90.1-2004, Appendix G. Applicable Internationally.
For the Blanchard College Center project, we are asking the USGBC to clarify the criteria for declaring whether a building is New or Existing in relation to the available points for this credit. In the specific case of the Blanchard College Center, the project is primarily a gut renovation of an existing historical facility, to which two new additions will be added. The area of the existing facility is approximately 33,403 s.f. The area of the two additions totals approximately 13, 885 s.f. The additions therefore represent approximately 29.4% of the total building area. From a systems standpoint, approximately 95% of the existing shell will be reused, however, there will be new furring/insulation for the walls and roof, new lighting, and new mechanical systems. We are assuming that this facility qualifies as an existing building, primarily because the existing facility represents the majority of the overall square footage of the project. In addition, the efforts to preserve the form and shell of the existing building has restricted the designer opportunities to pursue more aggressive energy reduction strategies (e.g., building orientation, daylighting/ventilation strategies, high performance envelope, etc.). Please clarify that this is the correct assumption for this project.
THIS LEED INTERPRETATION HAS BEEN REVISED AS OF 9/21/06 TO PROVIDE A CALCULATION THAT IS MORE WIDELY APPLICABLE (AND IS EQUIVALENT FOR THIS SCENARIO). To calculate the optimization point table for a project that has both existing and new construction, use the following formula for each line of the table: target percent = (existing SF / total SF) * (existing percent) + (new SF / total SF) * (new percent) *This equation applies to LEED NC v2.0, v2.1, and v2.2 and LEED CS v2.0 ORIGINAL LEED INTERPRETATION 9/5/01: To calculate the optimization point table for a project that has both existing and new construction, use the following formula for each line of the table: existing percent + ((new SF / total SF) * 10) = target percent. Applicable Internationally.
This project is a commercial office building located in New York City on a uniquely shaped parcel of land. The building is located on an asymmetrical triangular shaped lot of 5,549 sq. ft. While the building is six stories tall, the total square footage of the building is only 34,300 sq. ft. This type of building is quite unique to dense urban areas in making the most of a small lot. Due to the fact that this building is unique in terms of its height in comparison as compared to its sq footage, this CIR is asking if an allowance can be made to use a more comparable baseline per ASHRAE 90.1-2004 in the energy model. The following are the baseline building types outlined in ASHRAE 90.1-2004 for selection of Baseline HVAC System Types: - Residential - Nonresidential & 3 floors or Less & < 75,000 sq. f.t or 5 Floors or Less & 75,000 sq. ft. to 150,000 sq. ft. - Nonresidential & More than 5 Floors or >150,000 sq. ft. Per these requirements this small 34,300 sq. ft. building would be using the same baseline system descriptions as significantly larger facilities. We are proposing that because of this discrepancy that the third option of Nonresidential & 4 or 5 Floors & < 75,000 sq. f.t or 5 Floors or Less & 75,000 sq. ft. to 150,000 sq. ft. be a viable baseline for the project to use in the energy model. The systems that differ between the two baselines are as follows: Nonresidential & 4 or 5 Floors & < 75,000 sq. ft. - System 5 Packaged VAV w/ Reheat OR System 6 - Packaged VAV w/ PFP Boxes Nonresidential & More than 5 Floors or >150,000 sq. ft. - System 7 VAV w/ Reheat OR System 8 - VAV w/ PFP Boxes.
The applicant requests an exception to ASHRAE 90.1-2004 Appendix G modeling methodology that would allow the project to model a Baseline HVAC system type that more closely reflects the system type used for similarly-sized buildings. While the project\'s efficient use of land is commendable, the CIR process cannot be used to grant exceptions from ASHRAE modeling requirements. The project team must model the building using the applicable system type determined from the system mapping in Table G3.1.1A. Since the project is less than 100,000 square feet, the project team may opt to document credit compliance using the Option 3 prescriptive compliance path (the Advanced Buildings Core Performance Guide) rather than the Option 1 Whole Building Simulation compliance path. However, if the whole building simulation compliance path is selected, the project must follow all applicable ASHRAE Appendix G modeling protocol. Applicable Internationally.
The purpose of this CIR is to obtain confirmation of what is considered New Buildings vs. Existing Building Renovations within Option 1 of this credit. The project consists of a 120,000 SF existing building, which is part of and connected to other buildings in a corporate campus. The building was recently used for offices, which is the predominate use of the campus. There is no central mechanical plant for the campus-each building has its own mechanical system. The building is being converted to a large data center. The building\'s exterior shell will be retained but the existing mechanical and electrical systems, as well as all interior partitions, ceilings and finishes, will be removed. In short, the building is being gutted. We will be submitting this credit under Option 1: Whole Building Energy Simulation. The mechanical engineer is confident that the building will save at least 7% energy costs but not sure it will achieve 14%. Since we are required to achieve 2 points in this credit to achieve certification, we wish to be certain that the project will be considered Existing Building Renovation for the purpose of awarding points for energy savings.
Because the existing building shell is preserved, this project can apply for EAc1 using the Existing Building Renovations energy cost savings thresholds. Please note that if there are portions of the project that will be new construction, then use the equation provided in the LEED-NC v2.1 CIR Ruling dated 9/5/2001 (and revised on 9/21/06) to determine the appropriate point-thresholds. The equation follows below: To calculate the optimization point table for a project that has both existing and new construction, use the following formula for each line of the table: target percent = (existing SF / total SF) * (existing percent) + (new SF / total SF) * (new percent) Applicable Internationally.
Is there an adjusted point scale and minimum point threshold where applicable for LEED v2009 projects using ASHRAE 90.1-2010?
**July 1, 2016 update:This ruling has been revised to address the LEED 2009 minimum point requirement released 4/8/2016.**
Yes, LEED v2009 projects that demonstrate compliance using ASHRAE 90.1-2010 may utilize the adjusted point scale as shown in the Related Resource "ASHRAE 90.1-2010 Adjusted Point Scale for LEED v2009 Projects", subject to the following limitations:
• All mandatory provisions associated with ASHRAE 90.1-2010 (or an approved alternative standard) must be met in order for the project to use this compliance path.
• The ID+C thresholds shown are only relevant for projects using the Alternative Compliance Path described in LEED Interpretation 10412 that replaces the LEED 2009 requirements for EAp2, EAc1.1, EAc1.2, EAc1.3, and EAc1.4 with a Performance compliance path. All other ID&C projects would use the standard points available from EAc1.1 through EAc1.4 to comply with the 4-point minimum requirements.
• The CS 2009 EAp2-c1 ACP (http://www.usgbc.org/resources/cs-2009-eap2-c1-acp) may not be used in conjunction with this ASHRAE 90.1-2010 ACP. The project team must either use ASHRAE 90.1-2007 Appendix G with the CS 2009 EAp2-c1 ACP or use ASHRAE 90.1-2010 Appendix G without the CS 2009 EAp2-c1 ACP.
For projects that register on or after April 8th, 2016 and are subject to the mandatory Optimize Energy Performance point minimum:
If the project complies with all LEED v4 Minimum Energy Performance requirements for the relevant LEED v4 rating system, the project shall be considered to satisfy the LEED 2009 EA Prerequisite: Minimum Energy Performance mandatory minimum EAc1 points requirements (applicable for projects registered on or after April 8th, 2016), regardless of number of points achieved when applying this LEED Interpretation. The points documented under EAc1: Optimize Energy Performance shall be as shown in the ASHRAE 90.1-2010 Adjusted Points Scale for LEED v2009 for projects following the Performance Path, and zero for projects following a Prescriptive path.
For a project overseas utilizing split systems with heat recovery, confirm that it is acceptable to use a conversion ratio of 0.875 for EER to SEER (equipment outside of North America is only specified in EER), and that JIS, rather than ARI is an approved testing procedure.
The conversion ratio presented (0.875) seems appropriate based on the US EPA conversion. Secondly, the project is requesting confirmation of non standard (ARI) testing methods for the proposed equipment efficiencies. In regard to the non-standard testing methods, assuming the project is using a performance based approach, the proposed equipment is not required to meet any particular efficiency limits; however, the proposed equipment must be modeled appropriately and accurately. Meaning that whatever efficiency and standard is used, the equivalent efficiency and operating conditions must be modeled in the energy simulation software. Applicable internationally.
The project in question is an existing office building of which everything was demolished with the exception of the structure, slabs and roof. The building\'s skin was reconstructed and the mechanical systems were redesigned. The question is regarding the baseline model calculations used in the Energy and Atmosphere Credit 1 - Optimize Energy Performance. The credit requirements for Whole Building Energy Simulation say to use the Performance Rating Method in Appendix G of ASHRAE/IESNA 90.1-2004 to establish baseline building performance. One of the requirements of this standard (G4.1A - Baseline Building Envelope Orientation) states that "the baseline building performance shall be generated by simulating the building with it\'s actual orientation and again after rotating the entire building 90, 180, 270 degrees, then averaging the results." This requirement makes sense when talking about a building in new construction because you have the option to orient the building in such a way as to take maximum advantage of passive solar design, wind currents, etc. With an existing building the existing orientation is already determined so it doesn\'t make sense to establish a baseline off of the average of four orientations. When we model it this way we lose 6% of our energy reduction compared to the design case. We would like to ask if based on the fact that this building\'s orientation was already set because it is a rennovation project, that we can establish the baseline energy model solely off of that building orientation, not the average of all 4.
The applicant is asking if the project can be exempted from the rotation requirement of ASHRAE 90.1 Appendix G. Given the existing nature of the building, it would appear that the existing orientation, as well as the existing envelope would fall under the ASHRAE Appendix G Table 3.1, 5f requirement for Existing Buildings that states: "For existing building envelopes, the baseline building design shall reflect existing conditions prior to any revisions that are part of the scope of work being evaluated" Given that the existing building is already situated as stated in the CIR this set existing condition can be modeled as constant in the baseline. Applicable Internationally.
Our project is a new elementary school ( one-story, 85,940sf ), based on an existing prototype design layout that has been implemented for the last ten years throughout the City of Virginia Beach. This design is similar to Hermitage ES, which previously received certification and is used as an example in LEED for Schools. In keeping with other LEED philosophies, the City elected to re-develop the existing site for this project. Our project includes an existing school building on this pre-developed site. The existing school building and site will remain in operation, until the new building is completed. Since this project includes constructing a new school on an existing site ( with existing building and parking areas to remain in operation ), the project lacks the available land necessary for exploring mechanical systems to optimize energy savings ( such as geo-thermal ). As a result, the building design is struggling to meet the mandatory 2 Credits for EA C1. The Design Team is attempting to achieve the 2 Credits through the available Option: Prescriptive Compliance Path - Advanced Core Performance Guide. Under "Building Configuration" part of this guideline, there is a requirement to analyze three alternate building configurations to determine the most energy efficient configuration. While the design team did not develop three different design configuration concepts ( different footprint layouts ), an energy analysis of the proposed prototype building design layout was performed from all four orientations. The following is a breakdown of the cost comparison findings: 0 Degree Rotation: $ 63,432.00 90 Degree Rotation: $ 63,247.00 180 Degree Rotation: $ 63,300.00 270 Degree Rotation: $ 63,316.00 The results suggest that the annual energy cost difference from low to high between all four orientations is neglible (less than $200 a year). Therefore, the new school building prototype design layout, location and orientation is an energy efficient layout given that this is an existing site, and therefore complies with the essence of USGBC - LEED\'s "general intent" - to develop a building design layout with consideration to energy use and existing site conditions. Please confirm that our approach is acceptable to qualify for the mandatory 2 credits for EA C1.
The project team is asking for confirmation of their approach to one specific requirement of the Advanced Buildings Core Performance Guide. The project team\'s approach of modeling the building in four different orientations because of site restrictions does comply with the Building Configuration requirement of the Advanced Buildings Core Performance Guide. Please note that all other necessary requirements of the referenced standard must be followed in order to earn points for this compliance path. Applicable Internationally.
We are pursuing LEED NC for a high end high rise residence in Tokyo, Japan. We are showing compliance for EA-P2 and energy cost reduction for EA-C1 using the Performance Rating Method (Appendix G - PRM). ASHRAE 90.1 requires that the ratings for fenestration U-values, SHGC, and VLT are determined in accordance with NFRC 100 and 200. We will be using double paned and double paned Low E flat glass produced by AGC (Asahi Glass Co) here in Japan. AGC is one of the largest flat glass manufacturers and the parent company of AGC Flat Glass North America (formerly AFG - American Flat Glass). As this is a very high end residential project, with large glazed surfaces, a great deal of attention was paid to specifying glass in the design. Our issue is that AGC Japan products are rated using the Japanese Industrial Standards (JIS) and not NFRC as required. Although not explicitly stated in Appendix G - PRM, it is our understanding that if products are not NFRC rated, the poor default values provided in Normative Appendix A (Tables A8.1 and A8.2) of ASHRAE 90.1 are required to be used in place of manufacturer provided data for modeling purposes. NFRC rated products are not available in the in Japanese market. We have contacted AGC Japan to inquire if they have knowledge of NFRC rating procedures. Their response was that they do not, and only rate to JIS standards as required in Japan. The Japanese Industrial Standards (JIS) used for determining the solar optical and thermal properties of windows are JIS R 3106 and JIS R 3107. These two standards are stated by the Japanese Standards Association as being equivalent to ISO 9050 (Glass in building - Determination of light transmittance, solar direct transmittance, total solar energy transmittance, ultraviolet transmittance and related glazing factors) and ISO 10292 (Glass in building - Calculation of steady-state U values of multiple glazing). We understand that ISO 9050 and ISO 10292 form the referenced technical basis for ISO 15099 (Thermal performance of windows, doors and shading devices - Detailed calculations) which is the technical standard for determining optical and thermal properties of fenestration assemblies. ISO 15099 in turn defines the technical basis of NFRC 100 and NFRC 200. Other than the requirement for fenestration products being tested in a NFRC approved laboratory, which do not exist in Japan, we believe the JIS rated properties provided by AGC are in compliance with the technical requirements of NFRC standards and thus ASHRAE 90.1. Given this we have the following questions: 1) Can we use optical and thermal properties provided by AGC for Japanese domestically produced flat glass to model performance compliance in eQuest/DOE-2 using the performance rating method? 2) If 1) above is unacceptable, can we substitute optical and thermal properties of similar AGC NA (AFG) glass products for the eQuest/DOE-2 simulations? If the above is unacceptable, we have not identified any other way around this issue other than to import glass or have glass tested in the U.S. Both of these options are costly and not practical, and would deter this and any future LEED NC projects from being undertaken in Japan. In addition, we believe importing from abroad is not environmentally preferable in terms of CO2 impacts associated with transport.
The applicant is requesting the use of optical and thermal properties for fenestration determined by standards other than NFRC 100 and NFRC 200. The Japanese Industrial Standards (JIS) appear to be technically equivalent to the NFRC standards referenced in ASRHAE 90.1-2004. The use of optical and thermal properties determined by JIS 3106 and 3107 represent the actual thermal performance of fenestration products and may be used to determine fenestration parameters for use in the energy simulation. Please note that the NFRC ratings refer to the optical and thermal properties of the whole assembly. When preparing the EAc1 submission, the applicant should confirm that the optical and thermal properties determined by the applicable JIS standards and used in the energy simulation represent the properties of the whole fenestration assembly. Applicable Internationally; Japan.
This CIR is in regards to a 22,000 sf pool addition to an existing high school in upper climate zone 6. The building will contain a high-school sized short course pool in addition to a small therapy pool as well as locker rooms and two small offices and storage areas. The building\'s footprint is approximately square in shape and glazing will be used around the majority of the pool area to allow daylighting. The lighting system in the main area will have three levels of control to adjust for natural daylight to pour in and thus the lighting can be reduced appropriately. For compliance with EA credit 1, the project team decided it would be best practices to comply with the Advance Buildings Core Performance Guide. The team began investigating the Core Performance Guide during schematic design and we are currently just beginning construction documents. All prescriptive requirements from the Performance Guide for the building\'s envelope, lighting system, mechanical systems, domestic hot water, and construction practices either have been met already or will be met prior to completion. The project understands the nature of a prescriptive guide but is asking for a variance based on the following. All SHGC are below the maximum allowable for this climate zone (.3) but we are considering a much clearer glazing on the north-fa
The project team is inquiring as to whether or not they can deviate from one of the prescriptive requirements of the Advanced Buildings Core Performance Guide. Prescriptive Compliance path was included in EAc1 for projects that seek a quick and easy approach to credit compliance without using the whole building energy simulation. This approach may appear to be restrictive to the project team, but all of its requirements must be met exactly as specified. Therefore, it is not acceptable to deviate from a prescriptive measure. Please use Option 1-Whole Building Energy Simulation if the project team seeks more flexibility and/or trade-offs. Applicable Internationally.
Our project consists of two small buildings close to the ocean that will achieve substantial energy savings by incorporating a natural ventilation strategy. No mechanical heating or cooling is intended for either building, with the exception of a small electrical/server room. The building is designed with a very narrow and long floor plate situated perpendicular to prevailing winds in the area. Ventilation openings are consistent with the requirements of ASHRAE 62.1-2004 Section 6.8. The project also meets the requirements outlined in the CIBSE Applications Manual 10: 2005 as referenced in EQc2 for Natural ventilation in non-domestic buildings. Per Title-24 2005 requirements for natural ventilation, the sum of operable windows will be greater than 5% of the floor area of each space that is naturally ventilated. The openings will also be readily accessible to the occupants of each space at all times. Outdoor airflow through the openings in regularly occupied spaces will come directly from the outdoors, not through intermediate spaces such as other occupied spaces or corridors. Openings include operable windows, through-the roof ventilators, and vents between interior spaces. Control mechanisms for the natural ventilation openings are manual. A long, tall hallway situated perpendicular to the prevailing winds will collect heated air and exhaust it the outside. The roof over much of the space is sloped allowing air to enter on the low side and exit on the high side. In all cases, the building is designed to facilitate cross-ventilation with windows low on the walls for drawing the air in, and windows and vents high in opposite walls or on the roof to draw air out. Under ASHRAE 55 definitions, the building spaces are defined as "naturally conditioned spaces, occupant controlled" where the thermal conditions of the spaces are regulated primarily by the opening and closing of windows or vents by the occupants. Since the building will have a limited number of occupants most of the time, manual control of the windows and vents has been determined the most appropriate strategy for the building to allow control over individual thermal comfort. As indicated by ASHRAE 55-2004, section 5.3, the occupants of the space will be engaged in near sedentary activities with metabolic rates ranging from 1.0 met to 1.3 met. The mean monthly outdoor temperature for the project is greater than 50 deg. F, and less than 92.3 deg. F all months of the year, as required under ASHRAE 55-2004, section 5.3 for naturally ventilated buildings. The User\'s Manual for ASHRAE 90.1-2004 Appendix G states on page G-21: The proposed building default cooling system does not exclude natural ventilation from consideration. It just means that the proposed building is modeled as a hybrid system where cooling is provided by natural ventilation when conditions are acceptable and by the default mechanical cooling system when natural ventilation is inadequate to provide thermal comfort. We are requesting confirmation that the following modeling strategy conforms to the requirements of ASHRAE 90.1-2004 Appendix G modeling protocol: 1. EnergyPlus will be used to model the building since the EnergyPlus software has the capability to evaluate energy and comfort parameters tied to natural ventilation. 2. The Exceptional Calculation Methodology will be applied to calculate the natural ventilation savings. 3. The Proposed Design model will be developed to reflect the design parameters for the envelope and lighting. Operable windows will be modeled as fixed, and vents will not be included in the model. Mechanical systems will be modeled identically to the default heating, cooling and fan systems in the Baseline case, except that fans in the proposed case will be modeled as cycling on and off to meet heating and cooling loads during all hours in the proposed case, and will operate continuously during occupied hours in the Baseline Case (per the exception shown in Table G3.1.4). 4. Using the Exceptional Calculation Methodology, The Proposed Design case will be modified to include natural ventilation for all hours when the cooling and heating loads can be met. Operable windows and vents will be modeled as designed. Cooling and heating setpoint temperatures will be identical to those in the Baseline Case. Schedules will be adjusted to switch on mechanical cooling during hours when natural ventilation alone cannot meet the space temperature setpoints. The final model will meet the ASHRAE G3.1.2.2 requirements stipulating that the Proposed Design cannot exceed the Baseline Design unmet load hours by more than 50, and that unmet load hours for the Proposed Design and Baseline Design cannot exceed 300. 5. (Plan B) If the hybrid system cannot be manipulated to meet the unmet load hour requirements within the energy model, hourly output data from a natural ventilation model (having no mechanical cooling) and the Proposed Design model will be combined in a spreadsheet. Each hour where cooling and heating setpoints are met in the natural ventilation model, the hourly results for that model will be used. For all other hours, the hourly results from the Proposed Design Model will be used. 6. An Exceptional Calculation Methodology narrative provided with the EAc1 submittal will document any schedule adjustments and assumptions that were made to develop the hybrid system. The savings will also be included as a separate line item on the EAc1 submittal. Is our proposed energy modeling strategy for natural ventilation acceptable?
The project is requesting approval for the method of modeling natural ventilation as an energy efficiency measure and for taking credit under EA credit 1. Submittals for natural ventilation savings will be evaluated on a case by case basis. The tools and analysis protocol proposed is acceptable for modeling ventilation savings in this instance. Other analysis tools may also be appropriate. To be able to adequately document the process and the results, please be sure to provide in the LEED submittal the following:
- A detailed project description
- Clear identification of the areas that are taking credit for natural ventilation
- A detailed description or references that document the modeling algorithms and/or methodology for the natural ventilation portion of the energy model
- All thermostat, fan, infiltration and other appropriate schedules for naturally ventilated areas
Also, the submitted evaluation must demonstrate that the range of unmet load hours is similar for both the proposed and baseline building, to ensure that savings are not claimed for hours outside of the control parameters. In this case, the project has proposed to meet these peak loads with a hypothetical cooling system in the proposed building.
The project will also need to clearly demonstrate that the operational schedule for the natural ventilation system as modeled aligns with anticipated occupant behavior in terms of scheduled occupancy vs. modeled operation. For example, the model cannot assume that natural ventilation will occur when no one is in the building to operate the system. Because manual control is not addressed by the Appendix G modeling methodology, the manual control features of this project must be submitted under the exceptional calculation methodology for case by case review. The project must be prepared to demonstrate convincingly that a manual control strategy is appropriate and workable for this project. Please also be sure to take credit for this measure as a separate item on the LEED-NC v2.2 Submittal Template. Applicable Internationally.
Project is an undergraduate teaching Science Center consisting of physics, chemistry and biology laboratories, class rooms and faculty offices. Project is to be designed to meet the standards and guidelines of US Army Corps of Engineers (USACE). Army requires EPACT compliance to be measured as a percentage reduction in energy use. Per USACE Army LEED Implementation (January 2008): Performance improvement is based on EPACT energy use reduction percentage (measured in Btu/SF) instead of energy cost reduction percentage (measured in kBtu/year, $/year). Percentage improvement (energy reduction percentage) is calculated as follows: oPercentage improvement = 100* (Base building consumption - Proposed building consumption) / (Base building consumption - Receptacle and Process loads) -USACE equation is different than the one used per LEED-NC v2.2. Per USACE compliance, Receptacle and Process loads are subtracted from the Base building energy consumption denominator. Receptacle and Process loads are included in the numerator. -Building consumption is based on kBtu/year. Compliance Path: Project uses Whole Building Energy Simulation (Option 1) method in conjunction with USACE EPACT energy use reduction percentage calculation to determine energy reduction for EAc1: Performance Rating Method-Alternative Compliance Points. Option 1-Whole Building Energy Simulation requires a percentage improvement in the proposed building performance rating compared to the baseline building performance rating per ASHRAE/IESNA Standard 90.1-2004 (without amendment) by a whole building project simulation using the Building Performance Rating Method in Appendix G of the Standard. From ASHRAE 90.1 Standard and Reference Guide for LEED-NC v2.2, the following items are related to this CIR request: Building performance is to include Receptacle and Process loads in both the numerator and the denominator for the Base Building Performance Performance improvement is based on energy cost savings in $/year Percentage improvement (energy cost reduction percentage) is calculated as follows: o Percentage improvement = 100 * (Baseline Building Performance - Proposed Building Performance) /(Baseline Building Performance) -Building performance is based on annual energy cost in $/year. Clarification requested: Please confirm that government project can be rated in accordance with USACE Army LEED Implementation (January 2008) guidelines and criteria for EAc1 credit - Performance Rating Method-Alternative Compliance Points based on the following: 1.Use energy consumption kBtu/year, not energy cost in $/year, to determine the Performance Improvement. 2.Use the USACE equation to calculate the percentage improvement and use this percentage improvement to determine the number of points for EAc1 - Alternate Compliance.
The project team requested an alternative compliance path for demonstrating energy savings that conforms to the US Army Corps of Engineers (USACE) LEED Implementation (January 2008) guidelines, in lieu of ASHRAE 90.1-2004 Appendix G - Performance Rating Method. Based on the description of the alternative compliance methodology, the approach is not an equivalent method for determining energy savings and is not acceptable. For consistency, projects pursuing compliance Option 1 must comply with ASHRAE 90.1-2004 section G1.1. Appendix G is a modified Energy Cost Budget method and energy savings must be accounted as a percentage of energy cost savings, as dictated in ASHRAE 90.1 Section G1.2. Applicable Internationally.
Is it acceptable for a project to utilize a campus solar farm to achieve points under EAc2, and at the same time utilize rooftop solar panels, tied directly into the building power system, to achieve points under EAc1?
The solar farm can count towards EAc2, while the solar panels can count towards EAc1, and in fact, the PV generated on the building could be counted towards both EAc1 and EAc2 points. Applicable internationally.
Our project consists of a two story retail building. The building is open seven days a week from 9:00 am to 9:00 pm for business. We are requesting clarification regarding the modeling of lighting power density for the Proposed Design Case. In an effort to limit lighting energy usage, the project has developed two completely separate ambient lighting systems, which will NEVER operate simultaneously. A Building Automation System will be used to control the lighting systems, and to ensure that these systems do NOT ever operate in combination with one another. - System 1 consists of the general illumination (ambient lighting) having an overall LPD of 0.53 watts/sf, operational during business hours. - System 2 consists of the emergency/cleaning lighting system having an overall LPD of 0.9 watts/sf (using the ASHRAE 90.1-2004 Building Area Method). This system is a completely separate bank of lighting fixtures, which will only operate during the night for a few hours for housekeeping and maintenance, and during emergencies to provide code required egress lighting. Since the dual lighting systems have been designed for the purpose of limiting energy usage, and since these systems will never operate at the same time, we believe it would be unfair to require the project to model the cumulative lighting power density for the two systems for the "Proposed Lighting Power Density". Instead, we propose to model the lighting power density for the proposed case as two independent interior lighting systems for the building. The lighting power density for each system will then be compared to the base case ASHRAE 90.1-2004 building having a LPD of 1.5 watts/sf, based on the Building Area Method. For example, during store hours, the regulated lighting power would be modeled as 0.53 W/sf versus 1.5 W/sf allowed, and during cleaning hours the regulated lighting power would be modeled as 0.90 W/sf versus 1.5 W/sf allowed. We believe this modeling strategy meets the intent of the LEED v2.1 EAc1 credit by encouraging energy efficient design and controls, and by limiting total building energy consumption and costs.
The proposed modeling strategy does not comply with ASHRAE 90.1-2004. Per ASHRAE 90.1-2004, Section 9; "Exception to 9.1.3: If two or more independently operating lighting systems in a space are capable of being controlled to prevent simultaneous user operation, the installed interior lighting power shall be based solely on the lighting system with the highest wattage." Therefore, the proposed design must be modeled using 0.9 W/sf, for the purpose of the Energy Cost Budget calculation.
The purpose of this CIR is to obtain written confirmation and clarification that the use of TAS 9.0.7 software (by EDSL) can be approved as a energy modeling tool for pursuing EA Credit 1 and EA Pre-requisite 2 After reviewing ASHRAE 90.1-2004 Appendix G section G2, where all requirements are specified, we would confirm that the TAS 9.0.7 computer simulation software tool has the following capabilities: a. 8760 hours per year: TAS is able to simulate on an hourly basis over a total of 8760 year. b. Hourly variations in occupancy, lighting power, miscellaneous equipment power, thermostat set points, and HVAC system operation, deigned separately for each day of the week and holidays: TAS has the capability of adding schedules for all of the above. Different load profile can be created for different times of the day and for different days in the week. The possibility of creating out of hours conditions, nigh time setback temperature, etc. is also available. c. Thermal mass effect: TAS accounts for thermal inertia in the space. d. Ten or more thermal zones: TAS can handle more than ten different thermal zones e. Part-load performance curves for mechanical equipment: TAS is able to simulate part load performance for fans and pumps. TAS can model both constant and variable speed pump systems for primary and secondary. In the air side, different systems can be simulated (i.e. VAV, fancoils, etc) with variation in fan consumption as the load varies. f. Capacity and efficiency correction curves for mechanical heating and cooling equipment: TAS has the capability to incorporate correction curves, even combination of numbers of different types of boilers and chillers within the same project. g. Air-side economizers with integrated control: TAS can incorporate free cooling chillers. It has also the capability to model heat recovery air handling units with by-pass control with an air temperature set point. h. Baseline building design characteristics specified in ASHRAE 90.1-2004 Appendix G section G3: TAS allows the user to build a model for the baseline building using the characteristics specified in G3 and also those in G2.1 (same weather data and same energy rates), although the program does not generate it automatically and it is the user that has to carry out the modeling. 2.0 CIR - Design Energy Builder Energy Plus Modeling Tool Approval Please could you confirm whether the USGBC have approved the use of Design Energy Builder latest Version 2.2 of Energy Plus Software modeling Tool and if this is not the case is the software tool currently accepted by the USGBC.
The applicant is requesting approval to use EDSL TAS 9.0.7 software to document compliance with the energy simulation requirements in EAp2 and EAc1. USGBC does not maintain a list of approved energy modeling software. Instead, the project team must ensure that the simulation tool satisfies the requirements of ASHRAE 90.1-2004 Appendix G Section G2. The Design Builder energy simulation and visualization tool incorporates the EnergyPlus simulation engine. EnergyPlus should meet the ASHRAE 90.1 Appendix G Section G.2.2 requirements. Applicable Internationally.
The project in question will be a core & shell warehouse building. The first sixty feet inside the loading dock doors is considered a staging area. Due to the nature of this space, this area will remain an open area, without walls or storage racks, regardless of the tenant layout. Our core & shell warehouse project developer/owner proposes to install skylights in the perimeter zone (staging area) of the facility to afford the tenant daylighting in the loading areas of the facility. In addition, the developer/owner will install a daylighting control system with photosensors (minimum one per perimeter zone and tenant) in the core & shell facility. Tenant design guidelines will require that the tenant connect their installed lighting in these perimeter zones to the daylighting control system. Appendix G of ASHRAE 90.1-2004 states that the proposed case may take advantage of daylighting controls when installed. The ambiguity and thus our question lies in the case when the tenant will install the lighting but the owner has provided both a building envelope congruent with interior daylighting design strategies and a control system that will reduce electric lighting automatically due to the available daylight. With regards to Energy & Atmosphere Credit 1, Appendix G of ASHRAE 90.1-2004 and a core & shell building, can the proposed case energy model account for the electric lighting savings (lighting designed and installed by the tenant) that result from use of daylighting controls (provided by the owner) in conjunction with the installed skylights (provided by the owner)? In our model, the savings and skylights will be restricted to perimeter zones only.
The proposed case can account for the electric lighting savings from daylighting controls relative to the allowed lighting power density as long as connecting the installed lights to the daylighting controls is required in the tenant lease agreement. Please see the LEED-CS errata posted on November 2 for details on the tenant sales and lease agreement credit compliance path. Applicable Internationally.
Clarification is requested regarding whether garage demand control ventilation may be modeled for credit. Garage Ventilation is not addressed by ASHRAE 90.1 – 2007, Appendix G, therefore if savings is claimed it must be modeled as an Exceptional Calculation Measure (ECM). Garage demand control ventilation is increasingly becoming standard practice in newly constructed buildings. In order to take credit for this measure as an ECM, it must be demonstrated that the proposed design goes beyond standard practice.
ECMs must be approved by the Rating Authority. As the Rating Authority for LEED projects, the GBCI will accept an ECM for garage demand control ventilation under the following circumstances:
1) Baseline case shall meet the requirements of ASHRAE 90.1-2010, Section 6.4.3.4.5 Enclosed Parking Garage Ventilation. Baseline fan volume shall be based on the minimum required ASHRAE 62.1 parking ventilation rates of 0.75 cfm / square foot. Baseline system fan power shall be calculated at 0.3 watts per CFM.
2) Proposed case shall reflect the actual design. Evidence shall be provided documenting that demand control ventilation strategies are sufficient to automatically detect contaminant levels of concern in parking garages (for example, Carbon Monoxide, Particulates, VOCs, etc. and NO2) and modulate airflow such that contaminant levels are maintained below specified contaminant concentration as identified in ASHRAE 62.1-2010 Addendum d. Evidence shall also be provided that contaminant sensors are placed in space in an appropriate manner for detection of contaminant in question, included in the building commissioning plan upon installation, and then calibrated yearly following installation.
The contaminants of concern that must be monitored may be limited to CO if a narrative is provided justifying how the controls will also help to limit NO2, VOCs and PM2.5 concentrations. The narrative should address how the parking garage minimum exhaust flow rate and/or the minimum fan run time (if applicable) are maintained, and provide clarification that other contaminant levels are expected to remain low based on that design. Note that NO2 would also be expected to be monitored in garages where more than 20% of the vehicles are anticipated to be diesel-fueled.
Note: though it does not need to be addressed specifically in the narrative, the project team must confirm compliance of all ASHRAE 62.1 mandatory measures, including the measure addressing “Buildings with Attached Parking Garages” requiring limitation of vehicular exhaust into adjacent spaces. .
3) If other activities occur in the garage area, the ventilation for these uses shall be in addition to garage vehicle ventilation.
4) Proposed case shall be modeled such that a minimum air flow of 0.05 cfm/square foot is maintained.
5) A narrative shall describe all Baseline and Proposed case assumptions included for this measure, and the calculation methodology used to determine the projected savings. The narrative and energy savings should be reported separately from the other efficiency measures in the LEED Form.
6) No more than a 75% fan energy savings shall be claimed for this measure.
UPDATED on 01/05/18 for rating system version applicability and in Section (2) to clarify that not all contaminants of concern must be continuously monitored.
Many projects in Europe are connected to highly efficient district energy systems. However, the EAp2/EAc1 Option 2 guidance provided in the "Treatment of District or Campus Thermal Energy in LEED V2 and LEED 2009 - Design & Construction" (DESv2) document is not well-suited for the complex interconnected district energy systems with multiple fuel sources that are common in Europe. Many European countries already make use of the Primary Energy Factor (PEF) as a means of evaluating district energy performance and building energy performance. Is there an alternative compliance path available to document EAp2/EAc1 credit for the district energy system using the Primary Energy Factor in lieu of the DESv2 Option 2 compliance path?
An alternative EAp2/EAc1 compliance path is available to document the energy performance for complex interconnected district energy systems in Europe using the Primary Energy Factor and the greenhouse gas emissions associated with these systems. The Sweden Green Building Council developed an approved method, "Treatment of European District Energy Systems in LEED" (available November 1, 2012), which may be used in lieu of EAp2 Option 2 of the "Treatment of District or Campus Thermal Energy in LEED V2 and LEED 2009 - Design & Construction" guidance. This compliance path is currently available for projects located in Europe only. Note: The "Treatment of District or Campus Thermal Energy in LEED V2 and LEED 2009 - Design & Construction" (DESv2) is Optional Guidance for LEED 2009 projects. However, project teams that use the guidance must apply all relevant portions of the guidance. The alternative compliance path outlined in the "Treatment of European District Energy Systems in LEED" may only be used to replace Option 2 of the EAp2/EAc1 Energy Modeling Path defined in the DES v2 guidance. Project teams that opt to use the "Treatment of European District Energy Systems in LEED" method must comply with all other applicable requirements of the DES v2 guidance such as those defined for EA Credit 3, EA Credit 4, EA Credit 5, etc. Applicable Internationally; only for projects located in the Europe region.
This credit interpretation request is regarding the baseline system selection. The project is a campus classroom/laboratory building in Grand Junction, CO. The proposed building HVAC system is composed of distributed water source heat pumps served by a district geothermal condenser water loop. The district geothermal system has enough ground wells such that nearly all condenser heating and cooling loads will be met. However, there are gas fired boilers and cooling towers in place that will help to maintain loop temperatures during peak heating and cooling conditions. Our confusion is that the campus district cooling and heating system falls under the document, "Required Treatment of District Thermal Energy in LEED-NC version 2.2 and LEED for Schools." However, this document does not address the case of a district condenser water loop. If we were to follow Appendix G ignoring the fact that the building is served by a district condenser water loop, the system falls under the category of a hybrid system and ASHRAE 90.1-2004 Appendix-G dictates that the baseline system should be System 5 - Packaged VAV w/ Reheat. When we compare the baseline and proposed systems, this appears to be a clear case of fuel-switching. The proposed system is 90% or more electric heating, while the baseline system is 100% natural gas heating via hot water boilers. We are proposing to use the "Energy Cost Budget" method for determining the baseline system as detailed in ASHRAE 90.1-2004 section 11. Based upon figure 11.3.2 in ASHRAE 90.1-2004, the baseline system would be System 6 -Heat pumps on a condenser loop with boilers and fluid coolers. Note 7 of Table 11.3.2.A describes System 6 and the water-source heat pumps assumptions. We would use the electricity and gas rates paid by the campus in both models rather than following Steps 1 and 2 in the document, "Required Treatment of District Thermal Energy in LEED-NC version 2.2 and LEED for Schools." The air distribution system in both models would be through distributed heat pumps served by the condenser water loop.
The applicant is requesting guidance for a building which receives condenser water for Heat Pumps within the building from a district geothermal loop (with supplemental cooling tower and boiler operation). The applicant is requesting that the system be removed from the "District" energy guidelines as well as the Appendix G Baseline system type and be allowed to use the ASHRAE Energy Cost Budget (section 11) methodology to define the Baseline system. It appears, based on the description, that the building does not fall under the District Energy requirements, in that it is not provided with cooling or heating from a district source, but rather provided with condenser water which feeds heat pumps that produce the cooling and heating within the building. As such it is not required to follow the methodology defined in the "Required Treatment of District Thermal Energy in LEED-NC version 2.2 and LEED for Schools." The project is also requesting exemption from the ASHRAE Appendix G system definition and to instead use the ECB method. According to LEED protocol, all projects following ASHRAE must use the Appendix G methodology, therefore this request is denied. The entirety of the Appendix G protocol must be used, including the Baseline system definition as determined by Table G3.1.1A. The project team may decide to pursue exceptions to this Table as identified in the "Exceptions to 3.1.1" portion of Appendix G, however it is uncertain if these will apply to the project. It would appear that the project should compare the design as described, to the appropriate system identified in Table G3.1.1A.
This project is a major renovation to the existing building envelope (new skin added, new windows) and to the common area part of a tenant occupied office building. We have received approval from the USGBC to use LEED for New Construction. The core space lighting (elevator areas, lobby, restrooms, conference rooms), ductwork and finishes will be modified but the central air handling system and air cooled chiller and the tenant spaces will be only minimally altered. The question has been posed by the building manager regarding if they need to replace the tenant lighting in the space as the tenant space is not in the scope of work for the project. According to the ASHRAE 90.1-2004 users guide, if you were to replace more than 50% of the lighting fixtures in the building, you would have to meet ASHRAE 90.1-2004 lighting requirements, which, based on our analysis of what the base case and current design is in terms of lighting power density for this office building, means the building managers would have to replace all the tenant lighting with T8, 25 Watt lamps. However, if we replace less than 50% of the lighting in the building, we are not dictated by ASHRAE 90.1-2004, unless the renovation increases installed lighting power. However, according to the LEED Reference Guide for the prerequisite EAp2, lighting applies to all lighting installed on the building site including interior and exterior lighting. If the total installed interior lighting power is lower than the interior lighting power allowance calculated using ASHRAE 90.1-2004, the project complies. These two statements contradict each other if there is less than 50% of the lighting replaced, but the LEED Reference Guide does refer to the ASHRAE 90.1 users manual as a reference. Please advise on what to assume for the tenant space lighting power density in both the base case ASHRAE 90.1-2004 compliant building and the design case if less than 50% of the lighting is replaced.
According to the requirements of the ASHRAE 90.1-2004, Appendix G Table G3.1 section 6, for the proposed case, if a complete lighting system exists, the actual lighting power needs to be modeled. Applicable Internationally.
We are working on this LEED NC 2.2 project in Beirut, Lebanon. To secure the minimum mandatory 2 points under EA Credit 1, we need to follow Option 1 - Thermal Modeling Simulations as it is the only available option for buildings above 100,000 square feet. After a lot of time spent attempting to gather local climatic data, we were unable to obtain a proper Weather Data File for Beirut which is fully accurate, has all the necessary climatic parameters, and is usable to undertake Option 1 Thermal Modeling Simulations. This is due to the last 35 years of unstable political situation / war in the country, resulting in a lack of proper weather data tracking and monitoring. Is it acceptable in such circumstances to select another city in the region with a very similar weather pattern, and use its weather data file for the simulations? We have selected the city of Larnaca, in Cyprus as in our opinion it represents the closest proxy for Beirut given the following: 1) Same climatic classification - Zone 3 as per ASHRAE 92.1 2) Same Mediterranean climate 3) Coastal city as Beirut 4) Its proximity to Lebanon 5) Very close latitude as Beirut: The latitude of Beirut is 33
The project has requested clarification regarding the use of an alternative weather file for a location that does not have weather data. Based on the given circumstances, it is an acceptable approach to select a weather data file that closest resembles the project location in climatic classification including average temperature, climate conditions, and latitude. Due to improved resources and computer simulation tools, it is possible to customize a weather file for a location. Some resources can be found here - http://apps1.eere.energy.gov/buildings/energyplus/cfm/weatherdata/weathe... and http://apps1.eere.energy.gov/buildings/energyplus/weatherdata_sources.cfm Applicable Internationally; Lebanon; Cyprus.
This Project involves the construction of a Testing Facility for High Volume Low Velocity circulation fans. The building consists of a 1940 S.F. General Office Area, a 1940 S.F. Shop Area, and a 40550 S.F. Testing Area with a 50\' joist height. The Testing Area will have in it at most (4) four High Volume Low Velocity circulation fans operating at the same time. The building will have no transient occupants, and a maximum of (6) six employees that will occupy the entire building during normal business hours. This CIR is in reference to the Testing Area. 1. Testing Area: As part of the USGBC New Construction & Major Renovation Version 2.2, the building is required to meet ASHRAE 90.1 2004 (Energy Standard for Buildings Except Low-Rise Residential Buildings), and ASHRAE 62.1 2004 (Ventilation for Acceptable Indoor Air Quality). In accordance with ASHRAE 90.1 2004 the Testing Area is given a baseline LPD (Lighting Power Density) of 1.4 W/SF as is standard for a Laboratory. The only reference in ASHRAE 62.1 2004 (Ventilation for Acceptable Indoor Air Quality) with regard to a Laboratory is listed in Table 6-1 under "Educational Facilities" - "Science Laboratories". The classification that most closely matches the actual use of the space in the Testing Area for ventilation purposes is a Warehouse, since the population density is low (6760 SF/Person), and the area will never contain "Laboratory" chemicals, "Laboratory" exhaust hoods, Make-Up air or a population density on par with an Educational Facility Science Laboratory. The Ventilation and Exhaust requirements for a Science Lab are (3) three times that of a Warehouse, and subsequently (3) three times the energy cost. Since the "actual" usage of the Testing Area fits the lighting energy requirements of a Laboratory (ASHRAE 90.1 2004) and the ventilation requirements of a Warehouse (ASHRAE 62.1 2004), can the design team consider this space as such for calculations, or does the requirement to stay consistent with room classifications supersede actual building function?
The applicant is requesting to use the lighting power calculations for one space type and ventilation calculations for a different space type. The ventilation quantities for the Testing facility appear to be associated with process issues associated only with the tests being run, not ventilation requirements associated with Standard 62.1-2004 requirements for indoor air quality. The project team should model the ventilation the same in the Baseline and Proposed Case, and should model the lighting power density requirements based on the closest space type from the ASHRAE Space-by-Space method.
Background: Our project is a 28,000 sf, two-story MBA educational and office building on a college campus. Our goal is to achieve up to 10 points under the EA c1.2 category. To that end, we are committed to reducing process loads, along with the other measures in the integrated building design to reduce overall energy use. This project primarily has office equipment as the majority of its process energy use. In order to reduce process load energy use in the building, a concerted effort has been made by the client to specify low energy use equipment, including EnergyStar rated equipment, in the building. Our strategy had been to collect all of the nameplate energy data available for the equipment, and enter this data into our proposed case model. However, it appears that nameplate data is not the best indicator of actual energy use from equipment. Numerous ASHRAE research projects confirm that nameplate data rarely reflect the actual power consumption of office equipment, and furthermore that the ratio of nameplate to power consumption also varies widely, from 25 to 50% of nameplate for equipment less than 1000W (ASHRAE Research project RP-1005, Hosni et al. 1999). Further plug load reduction strategies being considered include using occupancy sensor controlled power strips, which will allow monitors and other devices to be turned off when the occupants are not present. Proposed Strategy: Actual measured data of power draw from process uses would be the best data to use to model energy use, however this data is not readily available during design. In the rare case where we do have access to the same equipment to that which would be installed in the project, we would propose to measure the power draw from this equipment and use these results for the proposed case model. In most circumstances though, this is not a practical approach. The 2005 ASHRAE Fundamentals Handbook has looked at this issue in regards to how office equipment produces heat, for the purposes of more accurately assessing cooling loads for sizing HVAC systems. In their work, it is assumed that actual power consumption of the equipment is equal to the total radiant plus convective heat gain from the equipment. The Handbook proposes using two different strategies for determining \'actual\' power consumption and heat gain from office equipment (see highlights in attachments). 1. In cases where only nameplate ratings are available, they suggest that "Generally if the nameplate value is the only information known and no actual heat gain data are available for similar equipment, it is conservative to use 50% of nameplate as heat gain and more nearly correct if 25% of nameplate is used." 2. Much better results are gained, per the Handbook, by considering heat gains based on the type of equipment. ASHRAE publishes a series of tables in the 2005 Fundamentals Handbook documenting energy rates for multiple types of equipment (Chapter 30, Tables 5 through 10). Note that these tables provide information limited only to certain types of equipment. In regards to occupancy sensor controlled devices, the 2005 California Title 24 energy code allows for a reduction in task lighting energy use of 20% when controlled by occupancy sensors, which is based on their studies of the impact of this technology on energy use. Similarly, we would expect a 20% reduction in energy use for plug loads controlled by occupancy sensors in an office environment. Request: Please confirm that the use of measured power draw data from equipment is acceptable for modeling their process loads, when access to the same equipment is available during design. In cases where this is not available, please confirm that the use of the data published by ASHRAE in case #2 above shall be acceptable for equipment that is covered by their tables, and a factor of 25% used per case #1 for all other cases. If occupancy sensor controlled power strips are used for plug load devices, please confirm that those devices connected to the power strip can be modeled as having a 20% annual power savings. References: 2005 Building Energy Efficiency Standards SECTION 146 - PRESCRIPTIVE REQUIREMENTS FOR SERVICE WATER HEATING SYSTEMS (a) Calculation of Actual Indoor Lighting Power Density. The actual indoor lighting power of the proposed building area is the total watts of all planned permanent and portable lighting systems (including but not limited to, track and flexible lighting systems, lighting that is integral with modular furniture, workstation task lights, portable freestanding lights, lights attached to workstation panels, movable displays and cabinets, and internally illuminated case work for task or display purposes), subject to the following specific requirements and adjustments under Subsections 1 through 6. 4. Reduction of wattage through controls. The controlled watts of any luminaire may be reduced by the number of controlled watts times the applicable factor from TABLE 146-A if: TABLE 146-A LIGHTING POWER ADJUSTMENT FACTORS TYPE OF CONTROL TYPE OF SPACE FACTOR Occupant sensor with "manual ON" or bi-level automatic ON combined with multi-level circuitry and switching Any space ?? 250 square feet enclosed by floor-to-ceiling partitions; any size classroom, corridor, conference or waiting room 0.20 2005 ASHRAE HANDBOOK- FUNDAMENTALS page 30.8 to 30.10 Office Equipment - Nameplate vs. Energy Use Table 8 - Recommended Heat Gain for Typical Computer Equipment. Table 9 - Recommended Heat Gain for Laser Printers and Copiers
The CIR is requesting approval of an Exceptional Calculation Method (ECM) proposed to document the energy savings from selecting energy efficient appliances and equipment to reduce plug loads in the facility. Though the CIR specifically refers to how to calculate the proposed case energy usage, it is equally important to input correct baseline energy usage. In order to claim savings on process load equipment and appliances, actual measured energy use data must be obtained from both the baseline equipment and the proposed equipment. Project teams can conduct these studies themselves or can cite other studies of identical equipment. The same use schedules must be applied to each equipment type in both the baseline and proposed case. ASHRAE 90.1-2004 Appendix G Table G3.2 shows power adjustment percentages for automatic lighting controls. Though this table is not intended to address other systems controlled by occupancy sensors, it would be acceptable to use the 10% power adjustment indicated in the table for buildings greater that 5,000 SF for all systems controlled by occupancy sensors. Alternately, if there is published, credible data available demonstrating energy savings for equipment controlled by occupancy sensors, then the demonstrated values may be used, as long as the study is referenced (or preferably provided). Applicable Internationally.
The project is a retail shopping center. The developer proposes to seek Core & Shell (CS) LEED certification, and to encourage, but not require, tenants to seek Commercial Interiors (CI) certification. The interpretations requested apply to EA Credit 1, Option 1, Whole Building Energy Simulation, also referred to as Building Energy Modeling (BEM). We propose to use the Performance Rating Method for all energy consuming systems served by the Landlords meter, including the building envelope enclosing those spaces. There are no Landlord controlled energy consuming systems in the parts of the building enclosing tenant space. We propose for the building envelope enclosing tenant space to conform to ASHRAE 90.1 2007. This will be done by the prescriptive method if possible; otherwise we will use the Energy Cost Budget Method to prove equivalence. For this project, the core and each tenant space is separately metered by utility company meters. The developer will control only the core space and the building envelope. The building envelope will conform to ASRAE 90.1 2007, but will not be relied upon for major energy cost saving by the developer or by tenants. If the CS BEM includes all energy consuming systems served by the Landlord\'s meter; and excludes all energy consuming systems served by the tenant meters, the energy conserving measures applied by the Landlord will earn the maximum available EA 1 credits, and the project will be eligible for CS certification. If the CS BEM also includes tenant energy consuming systems, with no tenant energy cost reduction measures, the Landlord cannot apply enough reasonable energy cost reduction measures to qualify for the EA prerequisite, and cannot qualify for CS certification. The basic question is, can the Landlord qualify for CS LEED certification based only on work under his direct control, or must he mandate tenant energy cost reduction measures, as required to reduce total building energy cost by the prescribed level? A secondary question is how to apply the floor area limits of various requirements to the building. The building functions as a series of small spaces, not as a total building. Should the area of each space be used, or the total building area?
The project is inquiring as to how to achieve credit for a prescriptive method under EAc1 for a Core and Shell Building in which the owner/developer will not require tenants to pursue increased performance measures. For Option 2, page 264 of the LEED Reference Guide for Green Building Design and Construction 2009 Edition (Updated June 2010) states "To apply for credit under this option, a Core and Shell Project must comply with all requirements for the ASHRAE Advanced Energy Design Guidelines, including those that may be in the tenant\'s scope of work. A sales agreement or tenant leases may be necessary." As a result, it does not appear the owner will have sufficient control over the future tenant installations to pursue Option 2. Also, for Option 3, it does not appear the project would comply with the credit requirements. Section 2 includes both lighting and mechanical system efficiency requirements which appear to be outside of the scope of owner control. If Option 3 is pursued, both Section 1 and Section 2 would need to be complied with to achieve credit. Please note, that there is a path available for credit under EAc1, Option 1 for Core and Shell buildings where the owner does not have control over the future tenant spaces. For these situations, owner/developer controlled spaces should be modeled in the proposed case as designed. For spaces/systems not controlled by the owner/developer, the proposed case should be modeled identically to the baseline case. A spreadsheet tool is available (here) which prorates the point threshold based on the owner/ developer controlled percentages. If the prescriptive options are pursued, documentation such as tenant requirements and a tenant lease agreement must be provided to verify the future tenants will meet the prescriptive requirements. The project also is inquiring as to how the floor area limits are applied to the various requirements to the building. The total building area within the scope of the LEED project submittal should be used to determine the building requirements. Applicable Internationally.
Is it acceptable to use research on potential efficiencies of data center equipment, as published in an ASHRAE Journal article, to demonstrate the difference between baseline and design performance of a data center?
The performance metrics in the article itself are based on models generated by authors to demonstrate "order of magnitude savings possible" and do not provide any confidence in the effectiveness of the measures listed. Efficiencies and energy savings should come from manufacturers\' documentation. Applicable internationally.
We are requesting clarification regarding what percentage of a building must be open 24 hours for the building to be considered a 24-hour facility. ASHRAE 90.1-2004, Section 6.5.6.2 requires condenser heat recovery for preheating service hot water for facilities operating twenty-four hours per day, when the total installed heat rejection capacity of the water-cooled systems servicing the building exceed 6,000,000 Btuh, and the design service water heating load exceeds 1,000,000 Btu/h. Our project is a large retail complex which most likely exceeds the total installed heat rejection and service water heating loads listed. However, only 17% of the complex (a large arcade facility) is open 24 hours per day. The rest of the complex will be closed for a portion of each day. We believe we are exempted from the heat recovery requirement since the domestic water heating loads are mostly coming from the areas of the building that are not open 24 hours, and since only a fraction of the complex is open 24 hours per day. We would like confirmation that our interpretation is correct.
The applicant is asking to confirm their interpretation of a specific ASHRAE 90.1-2004 requirement. Based on the description provided, if the project is served by a single system, it should be considered as a 24 hour facility. If the system used for the conditioning of only the 17% of the complex (open as a 24 hour facility) does not meet the heat rejection or service water heating requirement, it would be exempt from the requirements of ASHRAE 90.1-2004, Section 6.5.6.2. Table G3.1 section 11 of ASHRAE 90.1-2004 describes the modeling requirements for service water heating systems including those covered by ASHRAE 90.1-2004, Section 6.5.6.2.
Our project includes a 120,000SF addition/renovation to a 140,000SF office building. Lighting control systems were installed to provide increasing levels of energy performance savings by adjusting the initial foot-candle levels down to IESNA acceptable maintained foot-candle levels. The project includes expansion of the existing Eaton\'s POW-R-Command lighting control system. Our approach is not proprietary to the Eaton system and could be applied to any automatic lighting control system. Use of our lighting control approach results in energy savings beyond the default 10% energy savings limit identified in Table G2.3 within ASHRAE 90.1-2004, Appendix G. We are requesting the USGBC allow us to use the alternative method to modify the lighting schedules beyond the 10% limit in accordance with the standard as outlined below. Standard lighting foot-candle design is based on maintained foot-candle levels understanding that initial levels will be higher and will degrade over time. For this project, the light loss factor is 85% of initial fixture performance. This standard design approach typically results in initial lighting designs that are over-lit and a higher w/sf value. For this project, the lighting foot-candle design and layout provides roughly 20%+ more initial illuminance than IESNA Recommended Guidelines, however upon installation, the lighting levels are dimmed through the lighting control system to those foot-candle levels which meet the IESNA Guidelines for maintained lighting illuminance. Over time, as lamp depreciation occurs, the illumination performance is automatically increased to consistently maintain the IESNA Guidelines level. This control approach has been in use within the existing facility for the past ten years. Dimming control of the system is programmed and performed by facilities staff only and the individual occupants do not have control capabilities. This feature can not be overridden by the occupants. Controlling and operating the lamps in this manner in the existing building have resulted in a 33% reduction in electrical energy use plus additional cooling capacity savings when compared to an un-controlled lighting approach and have resulted in approximately 40% lighting energy savings within the new addition. ASHRAE 90.1 - 2004 Appendix G, Paragraph G.25 - Exceptional Calculation Methods, states "When no simulation program is available that adequately models a design, material, or device, the rating authority may approve an exceptional calculation method to demonstrate above-standard performance using this method". However, in Table G3.1, paragraph 6(g), the standards states "For automatic lighting controls in addition to those required for minimum code compliance under 9.2, credit may be taken for automatically controlled systems by reducing the connected lighting by the applicable percentages listed in Table G2.3. Alternatively, credit may be taken for these devices by modifying the lighting schedules used for the proposed design, provided that credible technical documentation for the modifications are provided to the rating authority. We believe our project approach meets the intent of the alternative modified schedule approach. The system, as installed: Exceeds the energy savings allowed using standard building modeling protocol Meets the intent of the credit Provides a creative method to produce additional measurable energy performance savings Reduces environmental impact
The project team is requesting an allowance to account for energy savings from lighting control above the 10% as defined in ASHRAE 90.1-2004. As stated in ASHRAE 90.1-2004 Table G3.1, No. 4 Baseline Building Performance, non-standard efficiency measures such as lighting controls can be modeled by modifying schedules. The schedule change and energy savings should be modeled and submitted as an exceptional calculation method (Section G2.5 of ASHRAE 90.1-2004, Appendix G), with documentation that supports the proposed lighting schedule. Applicable Internationally.
Background: The Eastside Recycling center in Iowa City, IA will be a campus of 10 buildings / structures owned by the City of Iowa City. These buildings will provide public facilities for post-consumer recycling, materials re-use and sustainability education. As part of this campus, there will be 4 pre-engineered metal buildings. Each will be used for storage of recycled materials, electronic waste, materials to be re-used, and other miscellaneous storage. Only one of the 4 pre-engineered metal buildings has a dedicated office space which will be located in one corner of the building. The campus of buildings will be LEED certified using the LEED-NC for Multiple Buildings and On-Campus Building Projects. It is our intent to include these 4 pre-engineered buildings as part of the LEED certification. Proposed Strategy: In order to reduce energy consumption and simplify building maintenance, these 4 pre-engineered buildings will not be conditioned. Each building will have dedicated large-diameter overhead fans to circulate air, but there will not be a dedicated heating or cooling system. There will be a small office space in one of the metal buildings which will have an operable window as well as an electrical service outlet for a fan in the summer or electric space heater in the winter. These buildings would be defined by ASHRAE 90.1 as an unconditioned space, having less than 3.4 Btu/h*ft2 of floor area (both heating and cooling). As such, these buildings would not fall under the envelope requirements of ASHRAE 90.1. The minimum energy efficiency standards for EA Prerequisite 2 must comply with ASHRAE 90.1, and the performance rating calculations (using a whole building project simulation) for EA Credit 1 must comply with the Building Performance Rating Method in Appendix G of ASHRAE 90.1-2004. Because ASHRAE 90.1 does not apply to envelopes of buildings that are unconditioned space, the 4 pre-engineered buildings do not fall within the requirements of this standard. It is proposed to exclude the 4 pre-engineered buildings in the composite campus energy performance calculations in EA Credit 1 (Option 1) for the group of buildings to be LEED certified. As such, these 4 pre-engineered buildings would be excluded from the minimum energy efficiency levels required by EA Prerequisite 2. Interpretation: Is it acceptable to exclude these 4 pre-engineered buildings from the minimum level of energy efficiency requirements in EA Prerequisite 2 and the building performance rating calculations for EA Credit 1 (OPTION 1)?
The applicant requests clarification regarding whether unconditioned buildings may be excluded from the energy efficiency prerequisite (EAp2) and the energy efficiency performance rating calculations for EA Credit 1. If the buildings are included as part of the LEED scope of work, then they must be included in the energy calculations for EA Credit 1, and must meet the applicable portions of the referenced standard for EAp2. Specifically, the lighting for these buildings must comply with the minimum requirements of ASHRAE 90.1-2004. For EAc1, these buildings would be treated very similarly to unconditioned parking garages, where the envelope does not necessarily need to be modeled, but the electric loads from the lighting and fans are included in the energy calculations. Lighting in the baseline case should be consistent with the interior lighting power allowance in Section 9.2. Applicable Internationally.
Our project is located in California. To pursue Option 1: Whole Building Simulation, is there a methodology for documenting additional energy performance for LEED v4 projects regulated by Title 24-2016?
Project Type1
Additional Percent Savings
NC-Office
7%
NC-Retail (except restaurant/grocery)
8%
NC-School
7%
NC-Health Care
0%
NC-Restaurant/Grocery
0%
NC-Hospitality
8%
NC-Warehouse
0%
NC-Multifamily
8%
NC-All Other
0%
CS-Office
5%
CS-Retail (except restaurant/grocery)
7%
CS-School
5%
CS-Health Care
0%
CS-Restaurant/Grocery
0%
CS-Hospitality
7%
CS-Warehouse
0%
CS-Multifamily
7%
CS-All Other
0%
CI-Office
6%
CI-Retail (except restaurant/grocery)
7%
CI-School
6%
CI-Health Care
0%
CI-Restaurant/Grocery
0%
CI-Hospitality
7%
CI-Warehouse
0%
CI-Multifamily
7%
CI-All Other
0%
Title-24 vs. ASHRAE 90.1 for LEED-NCv2.2 EA Credit 1: LEED has stated that it will accept Title 24-2005 as an equivalent replacement for the ASHRAE 90.1-2004 code for the EA credit 1. LEED 2.2 requires the total energy use of the building (regulated and process loads) be used in the energy savings calculation for EA1. Title 24-2005 uses only regulated loads in the energy calculation. Since LEED 2.2 accepts Title 24-2005 as an ASHRAE 90.1-2004 equivalent, do the process loads need to be included in the Title 24 model for the LEED 2.2 EA credit 1 calculation? Or is the standard Title 24 analysis that considers only regulated loads the appropriate comparison?
Process loads must be included in the Title 24 model for the LEED 2.2 EAc1 compliance. LEED NC v2.2 EAc1 requires that the "default process energy cost is 25% of the total energy cost for the baseline building". Since the Performance Rating Method in Appendix G of ASHRAE 90.1-2004 also considers total energy (regulated and process), it is only appropriate that process loads should be included in the Title 24 model for LEED NC v2.2 EAc1 compliance. Also, Title 24 is based on energy cost comparisons and these must be included with EAc1 documentation.
Conventional vented domestic clothes dryers require approximately 200 cfm of exhaust when operating. In large multi-story residential buildings, the dryer exhaust is typically provided by dryer exhaust risers that vertically link multiple units with a constant or variable speed exhaust fan. Several exhaust risers may be used to meet the needs of all apartments in a building. Variable speed fans typically modulate based on static pressure in the exhaust riser and are limited no less than 25 percent of design flow. Constant speed fans assume some diversity and do not modulate. Either fan operates 24 hours per day. The dryer exhaust requires continuous makeup air that must be conditioned either at an outside air handling unit or as in additional infiltration load in individual residences. An alternative to conventional vented dryers are ventless condenser dryers. Condenser dryers still use heated air to evaporate water from the clothes, but use an air-to-air heat exchanger to condense water from the humid air rather than exhausting the air and replacing it with fresh air from the room. Heat from the dryer remains in the room and no external venting or makeup air is required. Vented dryers are the "standard practice" in large residential buildings. This is probably due to the fact that (1) vented dryers are the more familiar technology, (2) drying times are shorter with conventional dryers than with condenser dryers, and also because (3) vented dryers are less expensive than condenser dryers. Based on a 1998 study by James Kao of the National Institute of Standards and Technology (NIST) titled "Energy Test Results of a Conventional Clothes Dryer and a Condenser Clothes Dryer," condenser clothes dryers use between 5 and 30 percent more energy per pound of laundry than a conventional vented dryer (depending on the size of each load). The NIST study only accounts for the energy to operate the dryer. The study does not account for the additional effects on the HVAC system due to the outside air requirements. The net effect of using condenser dryers in lieu of conventional dryers is a reduction in overall energy use in the climate zone for the building we are studying (New York City climate). We propose the following as an exceptional calculation methodology to simulate the performance of condenser dryers over standard vented dryers: Baseline Building: 1. Model typical dryer energy patterns based on standard washing machine use patterns from EnergyStar. 2. Model the dryer such that none of the dryer energy results in heat gain in the space. 3. Model the Baseline Building with 50 cfm of air exhausted from each residential unit with a dryer. To do this, include dryer exhaust fan energy assuming that the fan runs at an average of 50 cfm, 24 hours per day, at the same static pressure as the other rooftop exhaust fans. Include 50 cfm of additional infiltration 24 hours per day for every residence with a dryer. Proposed Building: 1. Increase the dryer energy use by 20 percent based on a conservative rounding of the average results from Kao\'s study of dryer energy use. 2. Model the dryer such that all of the dryer energy results in heat gain in the space. 3. Model the proposed building without the dryer exhaust fans and without the additional 50 cfm of infiltration. Is this exceptional calculation method acceptable for LEED EAc1 credit?
The applicant is inquiring about the acceptability of a proposed exceptional calculation method that takes credit for using domestic condensing dryers instead of standard vented dryers in a multi-family high rise residential project. Using an exceptional calculation method to determine energy savings is a generally acceptable pathway. However, the information presented is not sufficient to determine if this exact calculation is adequate enough to determine the correct amount of savings (if there is a savings). The design team must provide justification for their specific assumptions in both the baseline case and the proposed case. Baseline Building: 1. Model typical dryer energy patterns based on standard washing machine use patterns from EnergyStar. This is acceptable. 2. Model the dryer such that none of the dryer energy results in heat gain in the space. Assuming no heat gain to the space is not self evident. Documentation in the form of industry accepted studies indicating as such would be required to ensure that this is an acceptable assumption. 3. Model the Baseline Building with 50 cfm of air exhausted from each residential unit with a dryer. To do this, include dryer exhaust fan energy assuming that the fan runs at an average of 50 cfm, 24 hours per day, at the same static pressure as the other rooftop exhaust fans. Include 50 cfm of additional infiltration 24 hours per day for every residence with a dryer. Assuming 50 cfm of continuous ventilation per dwelling may be excessive. A study of use patterns combine with cfm values for expected dryer type applied to this particular building would be required. Calculations on static pressure that include data on the height of the building, the max. static pressure per dryer and the expected duct size would also assist the reviewer in determining appropriate energy savings. Proposed Building: 1. Increase the dryer energy use by 20 percent based on a conservative rounding of the average results from Kao\'s study of dryer energy use. 20 percent is not necessarily a conservative figure. Further justification needs to be provided. Provide manufacturers data on the units and their proposed energy use. 2. Model the dryer such that all of the dryer energy results in heat gain in the space. Again, assuming that all of the energy used in the drying cycle results in heat gain to the space is not self evident. Industry accepted studies would be required to ensure that this is an acceptable assumption. 3. Model the proposed building without the dryer exhaust fans and without the additional 50 cfm of infiltration. This is acceptable as long as the figures determine from # 3 in the baseline case are used. Also, since the design team is proposing energy savings for the entire building based on the use of condensing dryers, some assurances must be given that all units will use condensing dryers.
Our project is a new 174,786 square foot refrigerated warehouse with interior offices. The office area will comprise approximately 8,800 square feet of the total building. The refrigerated portion of the building will be unoccupied and fully automated, maintained at -10 degrees Fahrenheit, and will include a receiving dock area maintained at +40 degrees Fahrenheit. For the baseline and actual energy performance calculations utilized for EAc1, we are proposing to calculate the office area and equipment of the building only, and exclude the refrigerated portion of the building. To clarify, the portion of the building under consideration includes the following elements: 1. Freezer Storage Area 2. Receiving Area (cold dock) a. Rail Access Vestibule b. Maintenance Room c. Storage Room d. Refrigerator Equipment Mezzanine e. Fire Pump/Sprinkler Room f. Electrical Room ASHRAE 90.1-2004 Section 2.3 states that the standard does not apply to "(c) equipment and portions of building systems that use energy primarily to provide for industrial, manufacturing, or commercial processes." The ASHRAE 90.1-2004 User\'s manual reinforces the point "for example, the Standard does not apply to refrigerated warehouses that are cooled to maintain the quality of the goods stored in the warehouse." We wish to clarify that for a refrigerated warehouse, the baseline and actual energy calculations for prerequisite EAp2 and credit EAc1 will be based on the office portion of the building only. All energy used for refrigeration in the previously described areas will be excluded from the calculations nor contribute to the required 25% process load. Note however, the envelope portion of the refrigerated warehouse will remain in full compliance with ASHRAE 90.1-2004 section 5. Please confirm that this approach is correct.
The applicant is requesting a waiver from including the refrigerated warehouse from EAp2 and EAc1 calculations. ASHRAE 90.1-2004 does not apply to refrigerated warehouses. This means that there are no minimum efficiency requirements prescribed in ASHRAE 90.1-2004 for these spaces. However, this does not mean that it can be excluded from EAp2 and EAc1 calculations. As per the LEED-NC v2.2 Reference Guide, ALL energy end-uses must be included in the EAc1 calculations. Since the refrigerated warehouse portion of the project is not regulated under ASHRAE 90.1-2004, the applicant must maintain this portion as energy neutral i.e. keep the modeling inputs for that portion identical in both the proposed and baseline models. Applicable Internationally.
Background: Our project consists of a 4-story office building approximately 105,800 square feet in area. The building will be conditioned by a variable air volume system which includes a single, custom penthouse air handling unit on the roof. The project has been designed to meet ASHRAE Standards 62.1-2004 and 90.1-2004 including the application of demand controlled ventilation strategies. Each temperature control zone will include a series fan-powered terminal unit with electric reheat and each is equipped with an ECM motor. While the basic benefits of ECM motors include motor efficiencies nearly twice that of a traditional PSC motor, negligible heat gain from the motor to the airstream, and the ability to perpetually maintain a given supply airflow, the ability to modulate the terminal fan via the building automation system (BAS) is now feasible allowing control strategies never before possible. Series fan-powered terminal units have traditionally operated at a constant airflow during occupied periods. The proposed terminal unit control strategy for this project includes multiple, unique operating airflow levels: 1. During cooling demand, the fan will operate at the maximum cooling airflow condition (while the primary air damper modulates). 2. Under no call for heating or cooling, the fan will slow to the "deadband" airflow of approximately 50% of the peak cooling airflow. 3. At initial heating demand, the first stage of reheat will be energized and the terminal fan will increase to the first heating airflow setpoint. 4. On a call for additional heat, the second stage of reheat will be energized and the terminal fan will increase to the second heating airflow setpoint, and likewise with the third and final stage of reheat. Note that the heating airflow setpoints are specifically calculated to result in a consistent discharge temperature of 83F for optimum diffuser performance and blending in the space. Intent: Develop a strategy that accounts for the energy savings provided by series fan-powered terminal units with ECM motors. Proposed Strategy: A Whole Building Simulation and energy analysis has been performed towards LEED certification via the Building Performance Rating Method and in accordance with Appendix G of Standard 90.1-2004 utilizing the Trane Trace 700 analysis software (v6.1.3). In detailed review of the program input tables and output reports, we determined that the software was unable to model the control strategy proposed above. This was confirmed via direct communication with the software engineers. Through additional research, we further understand that Carrier HAP, EQuest, nor any other DOE-2 based energy simulation program has the algorithms or capability required. We are requesting confirmation that the following strategy conforms to the modeling requirements of Appendix G. 1. Utilize the Trace 700 energy program to perform a complete building analysis determining all energy consumption for both the proposed building and baseline comparison building in accordance with Appendix G. 2. Apply the Exceptional Calculation Method specifically and only to the terminal fan energy consumption as allowed by Paragraph G2.5 of Appendix G. The Exceptional Calculation Methodology will be as follows: a. Energy savings will be calculated for each individual terminal fan size and at each reduced operating speed based upon the manufacturers fan power data. b. Operating run time at each fan speed within the proposed control strategy will be determined using the heating and cooling load profiles from the Trace 700 output reports. c. Fan terminal energy savings will be calculated by multiplying the run time of the fan by the reduction in KW of fan energy at each specific operating condition. d. The terminal energy savings will be subtracted from the Trace 700 simulation output summary. Is the proposed strategy acceptable?
The project has requested clarification regarding the use of a specific method of computing the additional savings of using Fan-Powered Boxes with a 3-Stage Heating Coil and Electronically Commutated Motors (ECM motors) over traditional PSC motors. This approach is valid and acceptable, but more detailed information must be provided on how fan run time is determined at each of the three heating stages. The motor efficiency should be verified for each airflow condition chosen in the post-processing. Hourly simulation tools such as Trace 700 use complex computation routines and these should be accounted for in any hand calculations that are used to substitute for a Trace 700 energy simulation. Specifically, simply assigning the fans to run at full load (where they are far more efficient than their traditional PSC counterpart) continuously for a large portion of a season (i.e. peak heating months) would not be accurate. To calculate savings for ECM motors the following analysis should be done in the energy model to show compliance with ASHRAE Standard 90.1:
This project is located on a multi-building medical campus in Illinois. Typical of a campus, it is composed of numerous existing buildings, parking structures, surface lots and circulation streets. The campus is proposing to build, as separately bid projects, a new inpatient building, some additions to existing buildings, and a new parking structure. Our intent is to pursue LEED Certification for the new inpatient building, a new multi-level parking structure and new portions of site work on the campus, but not the additions to existing buildings. One of the buildings included in the project boundary is an open parking structure. The parking structure includes an enclosed combination stair/elevator lobby. We intend to heat this stair/elevator lobby as well as ventilate the space. A telecommunication closet along with an electrical room will be heated and conditioned as well. The parking garage is not required to be ventilated since it is classified as an open parking structure. The parking garage and stair/elevator lobby will have lighting as required. LEED for Multiple Buildings allows a weighted aggregate for the group of buildings based on their conditioned square footage or aggregate PRM calculation. We would like to confirm only the areas being heated and conditioned are required to be included in the square footage calculation for this particular structure when being considered into the overall aggregate or overall PRM. The lighting square footage will take into account the overall square footage being covered by lighting. Please confirm that we are using the correct calculation methodology for this point.
The applicant has requested confirmation that the weighted average building method from the Multiple Buildings Application Guide is based only on the conditioned area of each building. This is a correct assumption. The language from the EA Credit 1 Multiple language guide states that the "weighted average for the group of buildings (should) be based on their conditioned square footage." The definitions of space types from ASHRAE 90.1-2004, page 13, should be used to identify whether spaces are defined as "conditioned", "semi-heated", or "unconditioned". The ASHRAE 90.1 Performance Rating Method (Appendix G) should be used to model each building in the project boundary, including the parking structure. Therefore, all interior and exterior parking garage lighting, elevator energy, etc. should be included into the energy model for the parking structure, regardless of whether the spaces are conditioned or unconditioned. Applicable Internationally.
Our project is a 573,000 SF warehouse facility in a mild climate. The facility is designed to function as a distribution facility at a trucking hub used to store and transfer goods. The typical set-up for a project of this type in the region is to have no mechanical cooling, ventilation and heating (for freeze protection only, temperature set-point 45F) is provided by series of roof-top units with gas-fired furnace. These units are typically constant volume. Since this project is pursuing certification under the LEED-CS v 2.0 rating system, to attempt any points under EA credit 1, we have to follow ASHRAE 90.1-2004, Appendix G - Performance Rating Method. Following the ASHRAE 90.1-2004, Appendix G - Performance Rating Method for a project of this type and size, we will have to model the baseline system as a packaged rooftop VAV with reheat provided by a fossil fuel boiler. A project of this size and type would not have anything even close to this baseline system. Also the modeling protocol requires the project to be modeled with mechanical cooling. Due to the unique nature of the project and its sheer size, it appears that the credit requires the project to use more energy to show that it saves energy. To address this issue, we are proposing the following adjustment to the modeling protocol - Proposed building - Model as designed in terms of envelope, HVAC systems, lighting systems, power distribution and schedules of operations Baseline building - Use the ASHRAE 90.1 section 11 and model as system 11 without mechanical cooling. All other systems will be modeled at minimum required efficiencies as per ASHRAE 90.1-2004. All schedules will be modeled as in the proposed model. Also the outside air rates will be maintained as per the proposed model. We believe that this approach will allow the project to pursue energy efficiency and take credit for any measures that they may apply. We also believe that this variance will allow the integrity of the rating system as it will not require the team to spend extra energy and money to demonstrate achievement of a credit. While the team acknowledges that not all credits apply to all projects, it is very difficult to make a case for green building without demonstrating energy efficiency from the view-point of the owner.
The CIR is asking what to use for proposed and baseline systems to meet the requirements of ASHRAE 90.1-2004 while still fairly representing the warehouse nature of the project. The answer depends on whether the space is classified as conditioned, semi-heated, or unconditioned. As per the ASHRAE 90.1-2004 Users Manual, a space is "unconditioned" if it has no cooling and a heating system of less than 3.4 BTUH/SF. A space is considered "semi-heated" if it has a heating system with a capacity greater than 3.4 BTUH/SF, but less than the climate specific value that can be looked up on table 3.1 of the ASHRAE 90.1-2004 Standard. If a space contains a cooling system greater than 5.0 BTUH/SF or a heating system greater than that listed in Table 3.1, then it falls in the "conditioned" category. The above criteria are based on the total output capacity of the equipment. IF THE SPACE IS UNCONDITIONED OR SEMI-HEATED: ASHRAE 90.1 modeling protocol is based around typical occupied and conditioned buildings. It is not meant to address industrial/manufacturing "process" areas, which warehouses may fall under if they meet the requirements of unconditioned or semi-heated spaces. These spaces fall outside the realm of ASHRAE 90.1-2004 and the modeler is asked to include them in the model "as-is," meaning, in this case, including only a heating system and no cooling. The systems should be identical in both the baseline and proposed cases. If the project wishes to show energy savings due to the HVAC system in these areas, an Exceptional Calculation Method (ECM) must be used. See ASHRAE 90.1-2004 G2.5 for this procedure. IF THE SPACE IS CONDITIONED: If the heating provided to the space exceeds the thresholds set forth in Table 3.1 of ASHRAE 90.1-2004, then the standard modeling methodology should be used even if it results in systems that are different than the industry standard for the space type. Please note that typically in a warehouse facility there are some spaces that are fully conditioned (offices, break rooms, etc.). Please follow the standard ASHRAE 90.1-2004 Appendix G protocol for these areas. Applicable Internationally.
A centrifugal chiller, manufactured in Brazil, is specified for the project. The chiller is not AHRI certified and there is no laboratory in Brazil that can do this test. Since there is no laboratory in Brazil that can do this test, to comply with section 6.4.1.4 Verification of Equipment Efficiencies of ASHRAE 90.1-2007 Standard, would the equipment fall under option d (if no certification program exists for a covered product, the equipment efficiency ratings shall be supported by data furnished by the manufacturer)? Can this equipment be used in the project?
A supplier’s claims regarding energy efficiency would not be considered sufficient to document compliance with EA Prerequisite 2 (Minimum Energy Performance) and EA Credit 1 (Optimize Energy Performance) for a centrifugal HVAC unit that has not been tested and certified by a 3rd party in accordance with AHRI Standard 550-590. However, if the project team can provide documentation that the efficiency has been tested by a third party using an equivalent standard for HVAC efficiency, this testing would be sufficient in lieu of the AHRI Standard 550-990 testing. Any differences in test conditions and the resulting adjustments to the efficiency values claimed in the energy model would need to be described in the project submittal documentation. Alternatively, the project team may use the supplier’s claims regarding energy efficiency if the commissioning scope of work includes field testing of the equipment efficiency for the range of full- and part-load design conditions under which the building will operate; any adjustments related to altitude, etc. must be accounted for in the commissioning testing. In this case, the energy modeling documentation must include details about the commissioning functional testing method to confirm the performance of the chiller at full and part load operation. If the LEED submittal is provided as a split design / construction phase submittal, and the commissioning agent determines that the equipment efficiency does not meet or exceed the efficiency values claimed by the supplier, the energy documentation must be resubmitted at the construction phase with the values measured by the commissioning agent.
For a Distribution Center, is it acceptable to distribute lighting in a manner that takes into account shelve placement, eliminating unnecessary energy consumption illuminating the shelves\' tops?
Yes, design teams are encouraged to develop integrated lighting designs that improve efficiency while meeting the design intent of the owner. Strategic placement of lighting fixtures is an appropriate strategy for accomplishing improved lighting efficiency. Applicable internationally.
The intent of this credit is to "Achieve increasing levels of energy performance above the baseline in the prerequisite standard to reduce environmental and economic impacts associated with excessive energy use." The requirements of Option 1 of this credit are as follows: - Demonstrate a percentage improvement in the proposed building performance rating compared to the baseline building performance rating per ASHRAE/IESNA Standard 90.1-2004 (without amendments) by a whole building project simulation using the Building Performance Rating Method in Appendix G of the Standard. Per Appendix G of the Standard, table G3.1.3.7: The baseline requirement is as follows: - Since the conditioned floor area is greater than 240,000 square feet, the baseline building chiller plant shall consist of 2 centrifugal chillers minimum with chillers added so that no chiller is larger than 800 tons, all sized equally. The exception that we would like to take is as follows: - We recognize the baseline requirement for centrifugal chillers on this size of project. Our experience with a number of recent projects similar in size and use to this project indicates that air cooled chillers are more cost effective over the long term investment. When analyzed as a total system in comparison to water cooled chilling systems, air cooled chillers offer several cost advantages. Advantages include less equipment to purchase, less equipment to install, smaller space use requirements, less maintenance, less refrigerant, and less water use. - We are requesting that air cooled chillers are allowed to be used when modeling the baseline building performance for this project.
ASHRAE 90.1-2004, Appendix G, establishes the baseline HVAC system in Table G3.1.1.A. For this size facility, Appendix G requires that the baseline have a chilled water system with water-cooled chillers. Applicable Internationally.
Our project is a 75,348 sf existing 2-story office building to be renovated and constructed to achieve LEED NC2.2 certification. Tenant #1 will occupy more than 50% in the initial buildout, thereby establishing the project as a Major Renovation under LEED NC. The balance of the building will eventually be occupied by a second tenant, not yet identified. The HVAC system will be installed for Tenant #1, but not for Tenant #2. It is our intention to perform the Energy Model as though the entire building will be air conditioned although the actual equipment will not be installed for Tenant #2 initially. Documentation will be provided including lease agreements verifying that 100% of the leased square footage complies with LEED requirements and a statement signed by the Owner verifying that all lease agreements will comply with the Tenant Guidelines. The Tenant Guidelines will establish the lighting power density, minimum HVAC efficiencies, etc. Additionally a letter from the Owner outlining requirements exceeding ASHRAE 90.1-2004 will be provided to future tenants and will be strictly enforced. We seek confirmation that the approach we propose will be acceptable for LEED NC2.2 certification of the building without the remaining Tenant Space #2 being occupied, provided sufficient LEED credits are earned.
The applicant is requesting approval to model tenant fit-out portions of the building with identical HVAC systems, lighting power densities (LPDs), etc. to the occupied portion of the proposed building. No HVAC, lighting, etc. system will be provided for the tenant fit-out portions of the building prior to LEED certification. Therefore, energy simulation parameters for these spaces are not known and need to be documented very specifically in the \'tenant lease agreement\' and not just be general. Specifics should include all of the following - system type, equipment efficiency, controls, system capacity and square foot load assumptions. The tenant fit-out portions of the proposed building should be modeled using baseline parameters and methods specified in ASHRAE 90.1-2004 Appendix G. Please note, however, that the parameters of any installed components (e.g., building envelope, shading, etc.) that are within the scope of the building construction may be modeled using the parameters shown on design drawings. In order to document this approach, the project team should provide a narrative which clearly identifies what portion of the building will not be occupied by the owner and what parameters in the tenant fit-out portion will be modeled according to the design drawings. The LEED submittal template should include both the proposed case parameters and systems that correspond to the owner occupied space and the tenant fit-out space.
The project is a large mixed use complex which will include a high rise residential tower, a mid rise hotel, a theatre, retail base under each of the above 3 buildings and parking facilities associated with all of the above. The following important energy saving measures is being considered for a system which is not addressed in ASHRAE 90.1-2004 prescriptive requirements or appendix G. Please advise if the proposed approach to modeling is acceptable. 1. The high rise residential tower includes provisions for individual clothes dryers in each apartment and will include engineered dryer exhaust systems to serve the stacked clothes dryers. In accordance with manufacturer\'s recommendations and good engineering practice, the exhaust systems will be sized based on a 60% diversity factor to be able to function during periods of high usage. Typically such systems are constant volume systems that exhaust air continuously, even when most of the dryers are off. We are proposing to use a variable volume exhaust system which will modulate the fan speed to maintain the recommended pressure in the riser at all times. We are also proposing to use a variable volume make-up air system which will vary the make-up air volume to match the exhaust flow rate. Both systems will substantially reduce fan energy and also reduce the required make-up air heating and cooling costs. ASHRAE 90.1 - 2004 does not address requirements for such dryer exhaust systems therefore we believe it is justified to model the baseline system as constant volume dryer exhaust with constant volume make-up air system. The proposed design will reflect the discussion above and be modeled as variable volume exhaust with variable volume recovery. Neither the baseline nor proposed design will include heat recovery because applicable codes prohibit any obstruction in the dryer exhaust systems. Please confirm whether modeling the baseline as constant volume exhaust and constant make-up without heat recovery and the proposed design as variable volume exhaust and variable volume make-up air without heat recovery is an acceptable modeling approach.
The project team is requesting verification of whether a variable volume exhaust system and variable volume make-up air system for stacked dryers in a residential building can be compared to a constant volume exhaust system in the Baseline energy model. As indicated by the project team, this issue is not addressed in ASHRAE 90.1-2004 prescriptive requirements or in Appendix G. Credit for systems not specifically addressed in the Appendix G modeling methodology must be modeled using the Exceptional Calculation Method, and theoretical and/or empirical information supporting the accuracy of the calculation method must be included. If the project submits an Exceptional Calculation Method to document credit for variable volume exhaust system and variable volume make-up air system for stacked dryers, they would need to clearly document: 1. That the Baseline system defined (including both the constant volume controls and fan capacities) is consistent with standard practice for similarly sized, newly constructed high-rise residential buildings. 2. How the control sequences will be applied to the project to achieve a true reduction in make-up air and exhaust-air volume during periods of low dryer usage (it is unclear how the pressure in the riser will correlate to the quantity of dryers in use, or how the makeup air and exhaust air volumes will be tracked with one another). Applicable Internationally.
We are pursuing EA Credit 1, Option 2. We are using "Advanced Energy Design Guide for Small Office Buildings" (Achieving 30% Energy Savings over ASHRAE 90.1) in lieu of energy modeling, as allowed by LEED Reference. We are remodeling a historic building. Many "Envelope" items are existing conditions for this building. Would it be acceptable if we pursue an "overall" envelope that meets or exceeds the recommendations for envelope construction? For example, we will be able to exceed recommended R values in the roof, but we have some existing exposed brick that must remain un-furred. Or, can we exclude some existing conditions and historical conditions from our requirements for envelope R values and SHGC (for glass) values?
The existing building project is seeking EAc1 credit using Option 2: the "Design Guide for Small Offices" compliance approach. The project is seeking an alternate envelope compliance approach using either an "overall envelope" approach or exclusions for existing and historical conditions. Exceptions and/or alternate compliance approaches are not permitted under EAc1 Option 2. The Design Guide for Small Offices was compiled based on multiple energy performance simulations that confirmed the cost-benefit of the recommended measures. The comparative benefits achieved through alternative compliance methodologies cannot be verified without additional energy simulation. Unless the project team can document that the project fully complies with all the prescriptive measures of the Design Guide for Small Office Buildings, a separate compliance path (either Option 1, or Option 3) must be taken to document points under EAc1. Applicable Internationally.
This question is in regards to a nursery and greenhouse project located in Golden Gate Park in San Francisco. Our project intends to use an EPA certified wood-fired gasification boiler as the main heating source for heating hot water (HHW): http://www.epa.gov/woodheaters/models.htm. This HHW will be used for both space heating in the nursery support building and for process loads in the greenhouse and may be used for DHW. The project will be managed by the Recreation and Parks Department, which oversees numerous parks throughout the city and has a readily available supply of wood from fallen trees at no cost except for the costs of wood transportation within the park and maintenance of the boiler. Because 1) EA credit 1 calculates the energy savings through usage and cost of conventional fuels, 2) EA credit 2 accepts biomass as an alternative and renewable energy source, and, 3) we do not have a method to quantify the cost of the fuel we are using, it is unclear how to accurately compare fuel usage. Our team is working off this assumption: The wood fuel for the gasification unit comes from standard tree maintenance and naturally occurring processes of tree life cycle and tree loss resulting from storms. Trees are not removed for commercial purposes and are therefore not defined as part of forestry practices, rather they are part of the Park\'s responsible stewardship of San Francisco\'s public resource and also address public safety. In addition, the wood supply is constantly regenerative, and the carbon emissions are the same as those produced during natural decomposition, and any other emissions are minimized in accordance to EPA standards. We believe this fuel source constitutes a renewable energy source. Our question is: Because the cost of heating water with wood gasification, as compared to a natural gas or propane system, is essentially zero, would it be accurate to exclude all energy costs associated with the gasification boiler?
The applicant is asking a two-part question - 1) Since there is no cost associated with the wood is the heat free? 2) Can the applicant use the wood (as biomass) for renewable energy credits? 1) It appears that the applicant is attempting to compare a wood fired boiler with a natural gas and/or propane fire boiler. This assumption is not appropriate as ASHRAE 90.1-2004 prohibits fuel switching. If the applicant is proposing to use a wood fired boiler in the proposed case calculation, a wood fired boiler must be used in the ASHRAE case model. However, a different rate can be used in the baseline case. 2) The applicant can use the wood powered energy for renewable energy credits. The wood must be harvested from a site that is contiguous to the project site and has the same owner. Therefore this ruling is limited to Golden Gate Park, San Francisco.
The question is based on ASHRAE 90.1 requirements for Performance Rating Method for building modeling. This building has very high internal loads with the baseline process load at 49% of the total building energy based on actual equipment. The internal load is primarily computer desktops and monitors. Both baseline and proposed building energy usage numbers are based on a calculation worksheet as published by the US dept of Energy for computer desktops and monitors. The Energy Star usage value increases the proposed energy building performance reduction by 10-15%. This lower value for the process load is still above the 25% requirement for the total building energy amount as outlined in the LEED requirements of this point. The equipment in the new building that the owner will provide will consist of Energy Star computer desktops and monitors. We request clarification that we can run the baseline with standard energy load based on LBNL 2007 standards and proposed building with Energy Star energy loads.
The applicant is requesting clarification on how to account for energy savings due to Energy Star rated equipment. Plug in equipment falls under the Process Loads category and any savings claimed under process loads have to be taken as an Exceptional Calculation. Please model the same process loads in both the baseline and proposed building. Then run a separate run of the proposed building with the Energy Star rated equipment. Report savings from this run Exceptional Calculation table in the LEED Submittal Template. Be sure to include a detailed narrative with all assumptions and supporting calculations with the submittal. Applicable Internationally.
Background The Phoenix Sky Harbor International Airport Automated Train project consists of an automated electric train which travels on an open, elevated railway serving three train stations. One station is attached to the existing air terminal building #4, one makes connection to the municipal light rail station adjacent to the airport at 44th Street, and the third (the EEL Station) is located on the rail system part way between these stations and adjacent to an existing parking garage. The terminal #4 and 44th St. stations are enclosed and conditioned and the application of LEED criteria is fairly straightforward. It has been suggested by value engineering that the EEL station be constructed as an "open" or unenclosed, unconditioned structure with a roof and interior lighting, but no exterior walls. The station will include normally unoccupied, enclosed, and conditioned ancillary equipment rooms which house electrical and communications/security equipment. It is anticipated that these ancillary areas will constitute about 5% of the total building area. Credit Interpretation Request This question deals with how the unconditioned, unenclosed portions of this building can evidence compliance with EA prerequisites and credits. In researching past CIRs on the USGBC website several cases involving unconditioned buildings were found, but none matched our project sufficiently to provide a level of confidence in the interpretation of requirements. In the proposed design, the unconditioned, unenclosed portions of the building will be naturally ventilated with no HVAC equipment, while the enclosed ancillary equipment spaces will be conditioned with conventional A/C or evaporative cooling and electric heating equipment. It is desired that the entire building be considered for certification, not just the ancillary areas. In configuration, this building most resembles a parking garage where there is lighting, vertical transportation, and conditioned ancillary areas, but no conditioning or enclosure of the occupied areas. The LEED NC Version 2.2 Reference Guide (First Edition) indicates on page 181 under HVAC system types that "For areas of the project without heating or cooling systems (such as parking garages), there is no need to model heating or cooling systems in either the Proposed or Baseline designs. This was supported by the CIR ruling dated 1/29/2008 relating to a CIR submitted on 1/11/2008 that addressed energy use simulation of unconditioned buildings. The Ruling stated "For EAc1, these buildings would be treated very similarly to unconditioned parking garages, where the envelope does not necessarily need to be modeled, but the electric loads from the lighting and fans are included in the energy calculations." Will it be permitted to treat the EEL station in this fashion, where the energy simulation will include use by lighting, vertical transportation and other ancillary energy uses, but not HVAC systems in the unenclosed areas? The HVAC systems serving conditioned equipment rooms will be included in the simulation and their performance will be compared with the baseline systems specified by ASHRAE Std 90.1 - 2004, Appendix G. Since the envelope requirements of ASHRAE 90.1 - 2004 do not apply to unenclosed and unconditioned buildings, may we assume that EAp2 is automatically satisfied for the unconditioned portions of the buildings and only the conditioned, ancillary portions of the building must comply?
The project team is requesting guidance on modeling an unenclosed structure under EAc1 - Whole Building Simulation, and how to satisfy EAp2 for the same building. For the unenclosed portions, the project team may follow the instruction given in the cited CIR (dated 1/29/2008); treating the unenclosed portion similarly to an unenclosed parking garage. The enclosed portions should be modeled as conditioned and adhere to the ASHRAE 90.1-2004 standard Appendix G modeling guidelines. For EAp2, as stated in the referenced CIR, the applicable minimum requirements of ASHRAE 90.1-2004 must be met under EAp2. This holds true for both the unenclosed and enclosed portions of the structure. The project must also include occupied interior space in order to be eligible for certification. Applicable Internationally.
Our project is a 50,000 sq.ft. speculative office building applying for LEED-CS v 2.0 certification. When the design process began, no tenant space was leased. Presently, a potential tenant is proposing altering the base building. For example, the client wishes to add skylights to the building as part of their tenant fit-up (not as a part of our contract). Since this is not part of our scope of work, we would like confirmation that this kind of change is not to be included in our energy model and overall application.
The inquiry is seeking clarification on how to distinguish between the core and shell scope and the tenant portion of scope for a project. If the work performed is not within the core and shell scope, it can be excluded from the all relevant prerequisite and credit calculations and should be modeled as energy neutral. A clear delineation of the scope of the core and shell project relative to the tenant portion should be provided with the LEED submission, including a list of all the alterations requested by the tenant. Applicable Internationally.
We have a question concerning how to draw the LEED project boundary of the C&S project described below. The goal of our client is to develop a sustainable shopping center and therefore planning has been executed with high standards of green building design. The scope of the project is a shopping center that is being built on a previously developed site in an urban environment. Some areas of the shopping center are built under ground level and one part extends underneath an old office building located on the site. There are also two residential buildings being constructed as a separate project on top of the shopping center. This is an example of building stacking, which increases development density and enhances community connectivity. Question: Can the office and residential buildings left outside the LEED project boundary despite the fact that the buildings are physically attached to the shopping center? Justification: The shopping center, the office building and the residential buildings form their own legal entities. In the country where the project is located the real estate register is 3-dimensional and the buildings are legally seen as separate real estate. Therefore the shopping center developer does not have control over the office building located and the residential buildings being built on top of the shopping center. The bottom floor of the office building is detached from the office building, rebuilt and attached to the new shopping center, but the rest of the office building is not within the scope of the shopping center development project and will be left as it is. The construction of the residential buildings is a totally separate project with a different time schedule and constructor. If the buildings were built side by side there would not be any doubt about project boundaries. Locating the office and residential buildings on top of the shopping center instead of being built side by side increases development density and enhances community connectivity. We see that the shopping center solely forms a LEED project in this case.
Based on your description of this specific project, the office and residential buildings could be excluded from the LEED project boundary, as long as the separate buildings do not commonly share energy systems. For energy modeling purposes, the shopping center would need to consider any potential energy reduction benefits (shading, blocking wind, etc.), from the existing office building or projected residential buildings, in the baseline and proposed case. It is essential that these “unregulated” components are consistent between the two models. It is pertinent to note that the exclusion of the office and residential buildings from the analysis is purely related to their location vis-à-vis the shopping center, and not based on the ownership of these entities.
For a new library project, if an Automated Retrieval System is installed, and therefore less building square footage is required, can the estimated energy savings of that eliminated floor space be taken into account for EAc1?
As per ASHRAE 90.1-2007, Appendix G Table G3.1, No. 1 a., the baseline building design must be modeled with the same number of floors and identical conditioned floor area as the proposed design. The exceptional calculation approach suggested is not acceptable. Applicable internationally.
Our question deals with selecting the most appropriate space usage and HVAC baseline equipment for non typical rooms for EAc1. The project involves the construction of an airplane hangar facility with a gross area of 26,000 square feet and 2 stories high. The building is comprised of office spaces, metal shops, mechanical room, electrical room, foam room (for fire protection equipment), telecom room and a hangar(with an area of 12200 square feet). A gas fired boiler will provide heating and chiller will provide cooling. The design building systems are as follows: -the office spaces are served by a VAV system with reheat coils -the metal shops are served by constant volume air handling units; the metal shops also have exhaust hoods with dedicated exhaust fans that are interlocked with dedicated 100% make-up air units equipped only with gas fired heat exchanger. -the hangar is heated by an under floor heating system and cooled by 2 rooftop units with direct expansion coils and each sized for half of the total load; the rooftop units are equipped with a gas fired heat exchanger that serves as a backup for the under floor heating system; the hangar will be used as a retrofitting space, meaning that an airplane will be brought in and equipped with various equipment; only attachment/detachment of equipment is performed in the hangar; actual work(preparation, manufacturing) on the equipment is performed in the metal shop rooms adjacent to the hangar. -the foam room is ventilated via a dedicated exhaust fan and outside air intake louver; heating is provided by unit heaters; no cooling provided -the mechanical room is ventilated by a dedicated exhaust fan and outside air intake louver; heating is provided by unit heaters; no cooling provided -the electrical room is ventilated by a dedicated exhaust fan and heated by a unit heater; no cooling provided -the telecom room is cooled and heated by a dedicated heat pump split system -stairways are heated by finned tube radiators; no cooling provided -the elevator machine room is cooled by a fan coil unit; no heating provided -janitors room and toilets are provided with a dedicated exhaust system; no cooling or heating is provided; -mixed shower/toilet rooms are provided with a heating and cooling system through a VAV box. For EAc1 we will use ASHRAE 90.1 Performance Rating Method make the following assumptions: 1. Baseline HVAC System: System 3 PSZ-AC 2. Space usage classification for the hangar is: "wood/metal shop" for ventilation and "workshop" for lighting 3. The dedicated 100% outside air make-up air units that serve the metal shops and are interlocked with the exhaust fans will be included in "process loads" category together with the exhaust fans. 4. Process loads generated by the metal shop rooms and hangar equipment will be the same in both baseline and proposed building performance. We have the following questions: 1. In the baseline building performance: should the janitors rooms, toilets, mechanical, foam and electrical rooms and stairways be served, individually, by system 3? 2. If the telecom room will be served by a heat pump system can the baseline building system be system 4 PSZ-HP (only for this room)? 3. Is our space usage classification for the hangar correct? Due to the fact that the metal shop work is performed not inside the hangar area, can the hangar room be classified as a "warehouse"(for ventilation purposes only)? 4. If our space usage classification for the hangar area is incorrect, please recommend one, for both lighting and ventilation. 5. Are our assumptions correct?
The applicant is requesting clarification regarding baseline HVAC system selection and space usage classifications for a manufacturing assembly and office facility. Responses to the individual questions are as follows: 1. Please refer to the zoning requirements in Table G3.1 Numbers 7 and 8 of ASHRAE 90.1-2004 for additional clarification regarding designation of thermal blocks in the energy simulation. 2. All zones with electricity as the primary heating energy source (or un-heated zones) must be modeled using System 4 - Packaged Single Zone Heat Pump per Table G3.1.1A of ASHRAE 90.1-2004. All zones with electricity as the primary heating energy source must be modeled using System 3 - Packaged Single Zone Air Conditioner with a fossil fuel furnace. 3. The "warehouses" occupancy category from ASHRAE 62.1-2004 is a reasonable assumption for determining the minimum required ventilation in the hangar space. 4. Not applicable per the response to question 3
The project includes two indoor swimming pools - one lap pool and one recreational pool. We plan to claim energy savings for the pools and natatorium. ASHRAE 90.1 will be used as the baseline for those elements that are covered by the standard; pool heating boiler performance, space ventilation fans, and lighting. For the performance of other pool equipment not addressed by the standard, specifically pool circulating pumps, the pool filtration systems, and the natatorium humidification control, we are proposing the baseline to be a recently completed pool that is owned and operated by the same entity as this project. We will quantify the baseline through field measurements and interviews as appropriate. Baseline pool circulation rates will be determined by the local health code and heating energy and evaporation rates will be calculated using the Energy Smart Pools software (see http://www.rlmartin.com/rspec/). Adjustments will be made to the baseline to account for each pool\'s temperature and activity rate impacts on evaporation in order to calculate natatorium dehumidification requirements. Pool and natatorium energy efficiency measures that we plan to carefully consider include optimum selection of pool circulating pumps for maximum efficiency, minimizing the total pressure drop through the pool circulation systems, variable speed circulation pumps, dehumidification (either mechanical or with outside air) with heat recovery, and a solar make up air preheating system. The savings for the potential pool and natatorium measures will be calculated from the baseline described above. Is this an acceptable methodology to establish the baseline and energy savings for the non-regulated loads in the pools and natatorium?
Per the LEED NC 2.2 Reference Guide, page 183, "project teams may follow the Exceptional Calculation Method (ASHRAE Std 90.1- G2.5) to document measures that reduce process loads. If credit is taken for process loads, the calculation must include reasonable assumptions for the baseline and proposed case." ASHRAE 90.1-2004, G2.5 further states "Applications for approval of an exceptional method shall include documentation of the calculations performed and theoretical and/or empirical information supporting the accuracy of the method." In the above request, there isn\'t sufficient information supporting the accuracy of the method or describing how to document calculations performed. Information from only one recently built pool does not constitute "empirical" data. In this case, the USGBC certification reviewer serves as the "rating authority" described by ASHRAE Std 90.1- G2.5 and will make rulings on a case by case basis. The pool system savings fall under the process load category and thus the Exceptional Calculation Method should be used to take credit for energy savings, per ASHRAE 90.1 G2.5. The burden of proof regarding what constitutes "information supporting the accuracy of the method" rests with the project team. As far as energy savings from the natatorium (space) measures, this should be addressed within the confines of the Performance Rating Method of ASHRAE 90.1-2004, per the exception made under G3.1.1(b). Applicable Internationally.
This project is a remodeling of an existing office building that will include the addition of a Data Center. The Data Center will make extensive use of server virtualization to save energy, space and money. Server virtualization is the technique of replacing multiple servers with one server running multiple "virtual servers" on one larger, high performance server. In their existing Data Center, our client runs an average of 8 virtual servers on each high-performance server. Although the high performance server uses more energy than any one of the low to medium performance servers that it replaces, this results in a net energy savings of between 60-75%. Our question is: Under EAc1, Option 1, may we use the Exceptional Calculation Method to model the energy savings accountable to server virtualization?
The applicant may use the Exceptional Calculation Method to take credit for any energy savings available from the server virtualization technology. Be sure to include as supporting documentation under EAc1 all assumptions made in the calculations, detailed data, any actual measurements taken to support the savings claims and any other pertinent information. Please note that the actual amount of credit will be determined by the review team at the time of the review. Applicable Internationally.
Recently, USGBC approved a CIR regarding savings from key cards in hotel rooms (5/14/07 - see attached). We are requesting that under LEED-NC savings from submetering of multi-family buildings be accepted as an exceptional calculation method. There are no code requirements for submetering of apartment or condominiums in multi-family buildings. Submetering of utilities for individual tenants or owners in multi-family buildings is an added construction cost, but significant energy savings result. Studies have shown that a minimum of 10% energy savings are achieved once individual metering is implemented. Research done by the New York State Energy Research and Development Authority (NYSERDA: http://www.nyserda.org/publications/SubmeterManual.pdf) estimates that installing sub-meters in a master-metered building can reduce building-wide electricity consumption by 10-26%. In Ontario, Canada, non-electrically heated submetered apartments have shown a 16-22% reduction in electricity consumption while electrically heated apartments with submetering showed a reduction in consumption of 30% (http://www.frpo.org/Document/Topics&Issues/UtilitiesEnergy/Options%20to%...). Based on these studies and the fact that submetering is not required by the energy codes, we request that USGBC allow an exceptional calculation method to account for the savings from submetering. We are proposing that 10% cost savings of all submetered end uses be allowed by the calculation method. So, if a living unit is submetered for electricity and gas, the project can assume 10% cost savings for each of these fuel sources based on the energy use within the unit. Energy use in common areas of the building would be excluded from the calculation. Is this acceptable? Related CIR\'s 4/12/2007 - Credit Interpretation Request Per ASHRAE 90.1-1999 and 2004 mandatory requirements, hotel guestrooms must include a master control device at the main room entry that controls all permanently installed luminaires and switched receptacles. We are considering automating this lighting control with the use of a key card-activated master switch. The control would turn off all permanently installed and switched receptacle lighting after the guestroom is unoccupied for more than 30 minutes. The controls may also be configured to allow the interior window shades to be closed automatically when the guestroom is unoccupied. Monitored data for hotel lighting usage patterns is provided in a 1999 Research study by Erik Page and Michael Siminovitch entitled "Lighting Energy Savings in Hotel Guestrooms." This study indicates an average daily usage of nearly 8 hours for the bathroom light, 2 hours for the desk table lamp, 5 hours for the bedside lamp, and 3 hours for a floor lamp. The study also showed that the high use fixtures (the bathroom fixture and bed lamp) did not experience a significant drop during typically unoccupied periods. Instead, these lights were 20% - 25% on during these periods; and the lighting energy consumed during these periods accounted for about 60% of the total guestroom lighting energy consumption. Another study for ACEEE entitled the "Emerging Energy-Savings Technologies and Practices for the Building Sector as of 2004" projects an energy savings for key card lighting controls of 30%. Based on the information provided in these two studies, it seems reasonable to credit hotel guestroom lighting fixtures with a 30% energy savings for automated control based on room occupancy. We propose to model the energy savings achieved through automated control of lighting and interior window shades as an exceptional calculation measure. The lighting savings would be calculated by adjusting the proposed case lighting schedules for all permanently installed and switched receptacle fixtures to 50% lower than the budget case for the percentage of guestrooms modeled as unoccupied. Lighting during all occupied periods will be modeled identically to the budget case. The guestroom lighting energy savings achieved through this measure for the affected lighting fixtures would be 30%. Automated control of the blinds is intended to limit solar heat gains, since the building is in a hot dry climate. The blinds will be modeled identically during the occupied periods as 50% open during daylit hours, and 25% open during evening hours. During unoccupied periods, the shades will be modeled as 25% open. As with all exceptional calculation measures, the savings for this automated control measure will include a narrative documenting the lighting and interior shading schedules and assumptions, and the calculation methodology, and will include a separate line item on the ECB report documenting the savings achieved from this measure. We would like confirmation whether the proposed modeling methodology is acceptable, or direction regarding any modifications that would need to be made to the proposed modeling methodology in order to comply with LEED ECB modeling requirements. 5/14/2007 - Ruling The applicant is requesting confirmation on the proposed strategy for two exceptional calculations. Based on the description of the lighting assumptions, the proposed approach is acceptable. In the LEED submittal please include a narrative documenting the lighting schedules and assumptions and the calculation methodology. Also include a separate line item on the ECB report documenting the savings achieved from this measure. Please provide enough detail in the documentation to allow the review team to ascertain the amount of credit claimed. Based on the description of the automated blinds, the assumptions concerning blind control are insufficient to model the proposed building.
The project team is inquiring as to whether or not sub-metering of multi-family residential buildings would be acceptable as an exceptional calculation method. The energy savings associated with sub-metering are due to a change in occupant behavior and not due to building efficiency. As a result, the schedules in the baseline case must be modeled identically to those in the design case. Therefore project teams may not claim credit for sub-metering of a multi-family residential building through the exceptional calculation method.
The project is a new City and County Courthouse in Denver. Many architectural spaces have high ceilings to bring additional daylight into spaces. To provide the required levels of lighting by IESNA with spaces with high ceilings, additional lighting must be provided. Title 24-2005, the California enegy code, can be utilized for energy compliance for projects in California. Title 24 has a lighting power density allowance for ceiling height. Additonally, a previous credit interpretation ruling found that the ASHRAE 90.1-1989 version of the energy code also had this lighting power allowance for ceiling height. Since Title 24-2005 can be used for energy compliance for projects in California, can the ceiling height lighting power density allowance also be applied to projects that are not in California? Height in feet above finished floor Multiply LPD by 12 or less 1.0 13 1.05 14 1.10 15 1.15 16 1.21 17 1.47 18 1.65 19 1.84 20 or more 2.04 Source: California Title 24-2005
The applicant is requesting clarification whether certain components of the Title-24 2005 energy code can be applied to projects that are not in California. Title-24 2005 energy code may only be used for compliance by projects that are in California. Furthermore, the prescriptive requirements for Title-24 standards may not be applied to ASHRAE 90.1 models, and prescriptive requirements for ASHRAE 90.1 standards may not be applied to Title-24 models. The project may not use the Title-24 lighting multipliers described above for projects that are not in California.
Station Lands - Phase 1 - EPCOR Tower: CIR for Energy and Atmosphere: Optimize Energy Performance (Credit 1) This CIR pertains to the appropriate Baseline system choice for a heated parkade, as per ASHRAE 90.1-2004. The building in question is a 29-storey office building with a 4-level underground parkade located in Climate Zone 7 (very cold, with \'5000-7000 annual heating degree days\'). The parkade is 26,500 sq.m. and requires 5,000 kW of heating capacity to heat the outdoor air (to ventilate the parkade) to above freezing point on the coldest day. The parkade will be heated to 4 \'degC\' in winter, and will not be cooled. In ASHRAE 90.1-2004, 189 W/sq.m. of heating output classifies this as a heated space according to Table 3.1 Heated Space Criteria, and the size of 26,500 sq.m. classifies it as requiring a System 7 - VAV w/ Reheat system in the Baseline according to Table G3.1.1A Baseline HVAC System Types. However, the parkade is a single thermal zone (earth on all walls and underneath, and a fully conditioned office space above), which makes a system choice of VAV seem inappropriate. The Proposed Design is a Built-up Single Zone system with natural gas furnace heat, and no cooling. Guidance from ASHRAE Technical personnel has been that "the Baseline is to provide a simpler system than the Proposed design." Question: In accordance with the actual thermal zoning of the parkade and the guideline that it is to be, generally, an equally simple or more simple system than the Proposed Design, should the Baseline system be a single zone system? If not, what is a proper system choice for the parkade in the Baseline case?
Under Section 3, "Definitions, Abbreviations, and Acronyms of ASHRAE Standard 90.1-2004 the definition of unconditioned space is as follows: an enclosed space within a building that is not a conditioned space or a semi-heated space. Crawlspaces, attics, and parking garages with natural or mechanical ventilation are not considered enclosed spaces." The parkade equates to a parking garage and is not considered an enclosed space therefore there is no baseline system. Heating for the space should be modeled identically in both the proposed case and the baseline as process energy. An acceptable baseline would be another single zone natural gas furnace with the minimum efficiency prescribed by ASHRAE Standard 90.1-2004. You can claim energy savings for proposed case via Exceptional Calculation Methodology with all the required documentation. Applicable Internationally.
Checklists
Step by step to LEED certification
LEEDuser’s checklists walk you through the key action steps you need to earn a credit, including how to avoid common pitfalls and save money.
Documentation toolkit
The motherlode of cheat sheets
LEEDuser’s Documentation Toolkit is loaded with calculators to help assess credit compliance, tracking spreadsheets for materials, sample templates to help guide your narratives and LEED Online submissions, and examples of actual submissions from certified LEED projects for you to check your work against. To get your plaque, start with the right toolkit.
Get the inside scoop
Our editors have written a detailed analysis of nearly every LEED credit, and LEEDuser premium members get full access. We’ll tell you whether the credit is easy to accomplish or better left alone, and we provide insider tips on how to document it successfully.
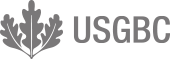
© Copyright U.S. Green Building Council, Inc. All rights reserved.
Requirements
Select 1 of the 3 compliance path options described below. Project teams documenting achievement using any of the 3 options are assumed to be in compliance with EA Prerequisite 2: Minimum Energy Performance.
Option 1. Whole building energy simulation (3-21 points)
Demonstrate a percentage improvement in the proposed building performance rating compared with the baseline building performance rating. Calculate the baseline building performance according to Appendix G of ANSI/ASHRAE/IESNA Standard 90.1-2007 (with errata but without addenda1) using a computer simulation model for the whole building project. Projects outside the U.S. may use a USGBC approved equivalent standard2. The minimum energy cost savings percentage for each point threshold is as follows:New Buildings |
Existing Building Renovations |
Points |
---|---|---|
12% |
8% |
3 |
14% |
10% |
4 |
16% |
12% |
5 |
18% |
14% |
6 |
20% |
16% |
7 |
22% |
18% |
8 |
24% |
20% |
9 |
26% |
22% |
10 |
28% |
24% |
11 |
30% |
26% |
12 |
32% |
28% |
13 |
34% |
30% |
14 |
36% |
32% |
15 |
38% |
34% |
16 |
40% |
36% |
17 |
42% |
38% |
18 |
44% |
40% |
19 |
46% |
42% |
20 |
48% |
44% |
21 |
- Compliance with the mandatory provisions (Sections 5.4, 6.4, 7.4, 8.4, 9.4 and 10.4) in Standard 90.1-2007 (with errata but without addenda) or USGBC approved equivalent.
- Inclusion of all the energy costs within and associated with the building project.
- Comparison against a baseline building that complies with Appendix G of Standard 90.1-2007 (with errata but without addenda) or USGBC approved equivalent. The default process energy cost is 25% of the total energy cost for the baseline building. If the building’s process energy cost is less than 25% of the baseline building energy cost, the LEED submittal must include documentation substantiating that process energy inputs are appropriate.
OR
Option 2. Prescriptive compliance path: ASHRAE Advanced Energy Design Guide (1 point)
Comply with the prescriptive measures of the ASHRAE Advanced Energy Design Guide appropriate to the project scope, outlined below. Project teams must comply with all applicable criteria as established in the Advanced Energy Design Guide for the climate zone in which the building is located. Projects outside the U.S. may use ASHRAE/ASHRAE/IESNA Standard 90.1-2007 Appendices B and D to determine the appropriate climate zone.Path 1. ASHRAE Advanced Energy Design Guide for Small Office Buildings 2004
The building must meet the following requirements:- Less than 20,000 square feet (1,800 square meters).
- Office occupancy.
Path 2. ASHRAE Advanced Energy Design Guide for Small Retail Buildings 2006
The building must meet the following requirements:- Less than 20,000 square feet (1,800 square meters).
- Retail occupancy.
Path 3. ASHRAE Advanced Energy Design Guide for Small Warehouses and Self Storage Buildings 2008
The building must meet the following requirements:- Less than 50,000 square feet (4,600 square meters).
- Warehouse or self-storage occupancy.
OR
Option 3. Prescriptive compliance path: Advanced Buildings™ Core Performance™ Guide (1-3 points)
Comply with the prescriptive measures identified in the Advanced Buildings™ Core Performance™ Guide developed by the New Buildings Institute. The building must meet the following requirements:- Less than 100,000 square feet (9,300 square meters).
- Comply with Section 1: Design Process Strategies, and Section 2: Core Performance Requirements.
- Health care, warehouse or laboratory projects are ineligible for this path (for NC & CS Projects).
- 1 point is available for all projects (office, school, public assembly, and retail projects) less than 100,000 square feet (9,300 square meters) that comply with Sections 1 and 2 of the Core Performance Guide.
- Up to 2 additional points are available to projects that implement performance strategies listed in Section 3: Enhanced Performance. For every 3 strategies implemented from this section, 1 point is available.
- The following strategies are addressed by other aspects of LEED and are not eligible for additional points under EA Credit 1:
- 3.1 — Cool Roofs
- 3.8 — Night Venting
- 3.13 — Additional Commissioning
Pilot ACPs Available
The following pilot alternative compliance path is available for this credit. See the pilot credit library for more information. EApc95: Alternative Energy Performance Metric ACPXX%
Upgrade to LEEDuser Premium to see how many projects achieved this credit. Try it free »
Got the gist of EAc1 but not sure how to actually achieve it? LEEDuser gives step-by-step help. Premium members get:
- Checklists covering all the key action steps you'll need to earn the credit.
- Hot tips to give you shortcuts and avoid pitfalls.
- Cost tips to assess what a credit will actually cost, and how to make it affordable.
- Ideas for going beyond LEED with best practices.
- All checklists organized by project phase.
- On-the-fly suggestions of useful items from the Documentation Toolkit and Credit Language.
In the end, LEED is all about documentation. LEEDuser’s Documentation Toolkit, for premium members only, saves you time and helps you avoid mistakes with:
- Calculators to help assess credit compliance.
- Tracking spreadsheets for materials purchases.
- Spreadsheets and forms to give to subs and other team members.
- Guidance documents on arcane LEED issues.
- Sample templates to help guide your narratives and LEED Online submissions.
- Examples of actual submissions from certified LEED projects.