Credit achievement rate
XX%
Upgrade to LEEDuser Premium to see how many projects achieved this credit. Try it free »
LEEDuser’s viewpoint
Frank advice from LEED experts
LEED is changing all the time, and every project is unique. Even seasoned professionals can miss a critical detail and lose a credit or even a prerequisite at the last minute. Our expert advice guides our LEEDuser Premium members and saves you valuable time.
Credit language
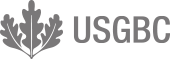
© Copyright U.S. Green Building Council, Inc. All rights reserved.
Requirements
Use materials with recycled content1 such that the sum of postconsumer2 recycled content plus 1/2 of the preconsumer3 content constitutes at least 10% or 20%, based on cost, of the total value of the materials in the project. The minimum percentage materials recycled for each point threshold is as follows:
See all forum discussions about this credit »What does it cost?
Cost estimates for this credit
On each BD+C v4 credit, LEEDuser offers the wisdom of a team of architects, engineers, cost estimators, and LEED experts with hundreds of LEED projects between then. They analyzed the sustainable design strategies associated with each LEED credit, but also to assign actual costs to those strategies.
Our tab contains overall cost guidance, notes on what “soft costs” to expect, and a strategy-by-strategy breakdown of what to consider and what it might cost, in percentage premiums, actual costs, or both.
This information is also available in a full PDF download in The Cost of LEED v4 report.
Learn more about The Cost of LEED v4 »Frequently asked questions
Can site materials, such as soil, be included in the MR credit calculations?The answer to this question is available to LEEDuser premium members. Start a free trial » (If you're already a premium member, log in here.) |
Are there recycled content claims that I should be wary of?The answer to this question is available to LEEDuser premium members. Start a free trial » (If you're already a premium member, log in here.) |
Can I count FSC-certified MDF toward both MRc4 and MRc7?The answer to this question is available to LEEDuser premium members. Start a free trial » (If you're already a premium member, log in here.) |
If I have one cut sheet that meets the LEED 2009 requirement to upload 20% of cut sheets by cost, for this credit, is that acceptable?The answer to this question is available to LEEDuser premium members. Start a free trial » (If you're already a premium member, log in here.) |
I have recycled content information for a product, but it doesn’t specify whether it is pre-consumer or post-consumer. What should I do?The answer to this question is available to LEEDuser premium members. Start a free trial » (If you're already a premium member, log in here.) |
The recycled content percentage on the product data sheet is given as a range. What should I do?The answer to this question is available to LEEDuser premium members. Start a free trial » (If you're already a premium member, log in here.) |
The manufacturer can't give me product-specific recycled content data, but they say that they fall within the national industry average. Can I use that?The answer to this question is available to LEEDuser premium members. Start a free trial » (If you're already a premium member, log in here.) |
Is the default average recycled content value of 25% for steel still allowed?The answer to this question is available to LEEDuser premium members. Start a free trial » (If you're already a premium member, log in here.) |
Checklists
Step by step to LEED certification
LEEDuser’s checklists walk you through the key action steps you need to earn a credit, including how to avoid common pitfalls and save money.
Documentation toolkit
The motherlode of cheat sheets
LEEDuser’s Documentation Toolkit is loaded with calculators to help assess credit compliance, tracking spreadsheets for materials, sample templates to help guide your narratives and LEED Online submissions, and examples of actual submissions from certified LEED projects for you to check your work against. To get your plaque, start with the right toolkit.
Get the inside scoop
Our editors have written a detailed analysis of nearly every LEED credit, and LEEDuser premium members get full access. We’ll tell you whether the credit is easy to accomplish or better left alone, and we provide insider tips on how to document it successfully.
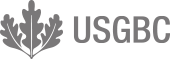
© Copyright U.S. Green Building Council, Inc. All rights reserved.
Requirements
Use materials with recycled content1 such that the sum of postconsumer2 recycled content plus 1/2 of the preconsumer3 content constitutes at least 10% or 20%, based on cost, of the total value of the materials in the project. The minimum percentage materials recycled for each point threshold is as follows:
XX%
Upgrade to LEEDuser Premium to see how many projects achieved this credit. Try it free »
Got the gist of MRc4 but not sure how to actually achieve it? LEEDuser gives step-by-step help. Premium members get:
- Checklists covering all the key action steps you'll need to earn the credit.
- Hot tips to give you shortcuts and avoid pitfalls.
- Cost tips to assess what a credit will actually cost, and how to make it affordable.
- Ideas for going beyond LEED with best practices.
- All checklists organized by project phase.
- On-the-fly suggestions of useful items from the Documentation Toolkit and Credit Language.
In the end, LEED is all about documentation. LEEDuser’s Documentation Toolkit, for premium members only, saves you time and helps you avoid mistakes with:
- Calculators to help assess credit compliance.
- Tracking spreadsheets for materials purchases.
- Spreadsheets and forms to give to subs and other team members.
- Guidance documents on arcane LEED issues.
- Sample templates to help guide your narratives and LEED Online submissions.
- Examples of actual submissions from certified LEED projects.
Can site materials, such as soil, be included in the MR credit calculations?The answer to this question is available to LEEDuser premium members. Start a free trial » (If you're already a premium member, log in here.) |
Are there recycled content claims that I should be wary of?The answer to this question is available to LEEDuser premium members. Start a free trial » (If you're already a premium member, log in here.) |
Can I count FSC-certified MDF toward both MRc4 and MRc7?The answer to this question is available to LEEDuser premium members. Start a free trial » (If you're already a premium member, log in here.) |
If I have one cut sheet that meets the LEED 2009 requirement to upload 20% of cut sheets by cost, for this credit, is that acceptable?The answer to this question is available to LEEDuser premium members. Start a free trial » (If you're already a premium member, log in here.) |
I have recycled content information for a product, but it doesn’t specify whether it is pre-consumer or post-consumer. What should I do?The answer to this question is available to LEEDuser premium members. Start a free trial » (If you're already a premium member, log in here.) |
The recycled content percentage on the product data sheet is given as a range. What should I do?The answer to this question is available to LEEDuser premium members. Start a free trial » (If you're already a premium member, log in here.) |
The manufacturer can't give me product-specific recycled content data, but they say that they fall within the national industry average. Can I use that?The answer to this question is available to LEEDuser premium members. Start a free trial » (If you're already a premium member, log in here.) |
Is the default average recycled content value of 25% for steel still allowed?The answer to this question is available to LEEDuser premium members. Start a free trial » (If you're already a premium member, log in here.) |